When selecting a gate valve for your application, several factors should be considered to ensure optimal performance and reliability. Here are key factors to consider when choosing the right gate valve:
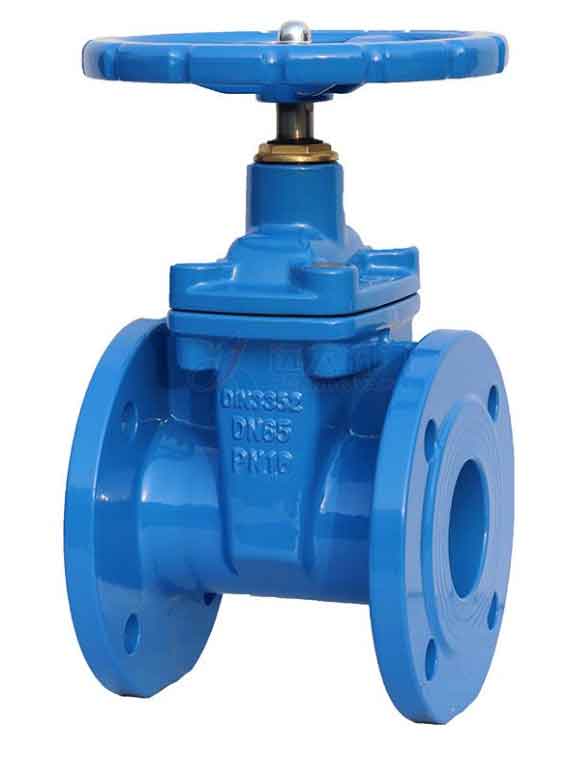
1. Valve Size and Pressure Rating: Determine the appropriate valve size based on the pipe diameter and flow requirements of your system. Consider the pressure rating needed to handle the maximum operating pressure in your application. Ensure the selected valve size and pressure rating match your system requirements to prevent flow restrictions or valve failure.
2. Valve Type: Gate valves come in different types, such as rising stem, non-rising stem, or slab gate valves. Consider the specific requirements of your application and select the appropriate valve type. Rising stem valves provide visual indication of the valve position, while non-rising stem valves are suitable for applications with limited space.
3. Material Selection: Choose the right valve material based on the compatibility with the media and the operating conditions. Consider the nature of the fluid (corrosive, abrasive, high temperature), and select a material that offers suitable corrosion resistance and mechanical strength. Common materials include cast iron, ductile iron, carbon steel, stainless steel, and various alloys.
4. Sealing Mechanism: Gate valves typically use either metal-to-metal or resilient (soft) seating mechanisms. Metal-to-metal seats provide excellent sealing but may be more susceptible to leakage in lower-pressure applications or when debris is present. Resilient seats, such as rubber or elastomer, offer better sealing in low-pressure or dirty service conditions. Consider the media characteristics, pressure, and temperature requirements to choose the appropriate sealing mechanism.
5. Operating Conditions: Evaluate the specific operating conditions of your system, including temperature, pressure, flow rate, and media properties. Ensure that the selected gate valve is designed to handle these conditions without compromising performance, integrity, or longevity. Consider any potential variations or fluctuations in operating conditions that may impact valve selection.
6. End Connections: Gate valves come with various end connection options, such as flanged, threaded, or welded ends. Select the appropriate end connections that match your piping system and installation requirements. Consider factors such as pipe material, system compatibility, and installation convenience.
7. Actuation and Automation: Determine if manual operation or automated actuation is required for your application. Manual handwheel operation is suitable for smaller valves or applications where frequent operation is not necessary. For larger or automated systems, consider pneumatic, electric, or hydraulic actuators for remote control and automated operation.
8. Standards and Certifications: Ensure that the selected gate valve complies with industry standards and certifications relevant to your application. Look for certifications such as API, ANSI, ISO, or specific regulatory requirements. Compliance with standards ensures that the valve meets quality, performance, and safety criteria.
9. Maintenance and Serviceability: Consider the ease of maintenance and serviceability of the gate valve. Look for features such as accessibility for maintenance, availability of spare parts, and ease of disassembly and reassembly. Valve designs that simplify maintenance tasks can help reduce downtime and extend the valve’s service life.
10. Budget Considerations: Evaluate the cost implications of different gate valve options, including the initial purchase cost, installation expenses, and long-term maintenance costs. Balancing performance requirements with budget constraints is essential to select a gate valve that provides the desired functionality and reliability within your allocated budget.
By carefully considering these factors, you can choose the right gate valve that meets the specific needs of your application, ensuring optimal performance, longevity, and reliability in your fluid handling system. Consulting with valve manufacturers, industry experts, or engineers can provide valuable guidance in the selection process.