When selecting a globe valve for optimal performance, several factors should be considered to ensure it meets the specific requirements of your application. Here are some key factors to consider:
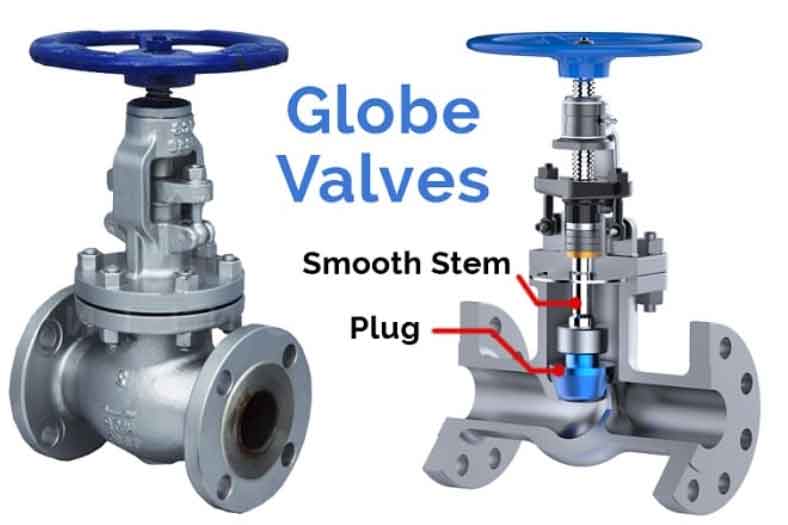
1. Valve Size and Pressure Rating: Determine the appropriate valve size and pressure rating based on the flow rate and pressure conditions of your system. The valve should be capable of handling the maximum flow rate and pressure without causing excessive pressure drop or compromising system performance.
2. Valve Type: Globe valves come in various types, including straight pattern, angle pattern, and Y-pattern. Consider the flow characteristics and space constraints of your system to choose the most suitable valve type. Angle pattern globe valves are commonly used for high-pressure applications, while straight pattern and Y-pattern valves are suitable for general applications.
3. Flow Characteristics: Evaluate the flow characteristics of your system, such as whether it requires linear or equal percentage flow control. Globe valves can offer either linear or equal percentage flow characteristics, depending on the design of the plug and seat. Select the appropriate flow characteristic to achieve the desired control and stability in your system.
4. Valve Material: Consider the compatibility of the valve material with the fluid being conveyed. Different materials offer varying resistance to corrosion, erosion, and temperature. Ensure the valve material is compatible with the fluid properties to prevent degradation and ensure long-term durability.
5. End Connections: Determine the appropriate end connections of the globe valve based on the piping system requirements. Common end connections include threaded, flanged, or welded connections. Ensure the valve’s end connections align with the existing or planned piping system for proper installation and integration.
6. Actuation Requirements: Determine whether manual or automated operation is needed for your application. Manual operation involves a handwheel or lever for opening and closing the valve, while automated operation utilizes actuators such as electric, pneumatic, or hydraulic actuators. Consider the control system requirements, speed of operation, and remote control capabilities to determine the suitable actuation method.
7. Seat Type: Globe valves can have different seat types, such as composition, metal, or soft seats. Consider the temperature, pressure, and fluid compatibility requirements to select the appropriate seat material. Soft seats provide better sealing but may have limitations in high-temperature applications.
8. Standards and Certifications: Ensure that the globe valve complies with relevant industry standards and certifications. Common standards include those set by the American Petroleum Institute (API), American Society of Mechanical Engineers (ASME), and International Organization for Standardization (ISO). Compliance with these standards ensures the valve’s quality, performance, and safety.
9. Maintenance and Repair: Consider the ease of maintenance and availability of spare parts for the chosen globe valve. Look for valves that are designed for easy access and maintenance, with readily available spare parts to minimize downtime during maintenance or repairs.
10. Supplier and Support: Choose a reputable valve supplier that provides reliable technical support, after-sales service, and a warranty. A reputable supplier can offer guidance in selecting the right valve and provide assistance throughout the lifecycle of the valve.
By considering these factors, you can select a globe valve that is well-suited for your specific application, ensuring optimal performance, reliability, and longevity. Consulting with valve manufacturers, industry experts, or experienced professionals can provide additional guidance in choosing the right globe valve for your needs.