The main valve holes of multi-way valves, change-over valves and other valves are thin, with many oil grooves and different cross-section shapes and sizes. In actual production, sand cores are designed by the method of lengthening the core head to produce castings. This kind of sand core bonding is not positioned correctly, resulting in defects such as inclined oil grooves of castings and unequal thickness of castings. In addition, due to the low overall strength of sand cores designed by this method, poor bending resistance and productionCasting defects such as drifting and bending of main valve bore often occur in the casting, which causes serious leakage inside the valve and the casting is scrapped.
During the valve body casting process, when the gas generated during the final filling stage remains on the top surface of the cavity and is adsorbed with the slag floating on the surface of molten iron, pit defects of different sizes and uneven distribution usually occur on the top surface of the casting and the side near the top surface, with the pit depth of 2-3 mm as shown in the figure.
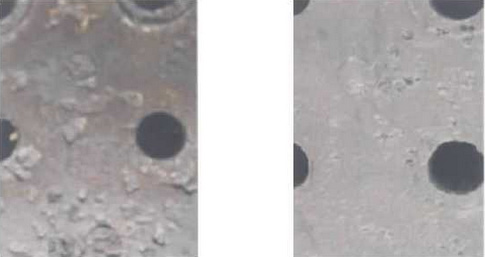
When the material of valve body casting is ductile iron, the unreasonable design of casting system will lead to uneven distribution of temperature field inside the casting, which makes it impossible to make full use of graphitized expansion in the solidification process of the casting. Moreover, due to the complex structure of the sand core, it is difficult to compensate the hot joint due to the large flow resistance of the metal liquid, resulting in the defects of shrinkage holes at the final solidified part of the hot joint.In addition, the unreasonable pouring system causes the irregular flow of molten iron in the mold, even causes the splash of molten iron and the interaction with air in the mold to be oxidized, resulting in slag inclusion defects in the casting; the excessive content of sulfur and oxygen in the molten iron and the low pouring temperature will cause slag inclusion defects.
Adhesive sand is also a common casting defect in valve body castings, i.e. sand grains which are difficult to remove from the surface of the castings or compounds formed by metal oxides and moulding sand.Sand sticking usually occurs at the parts with strong heat action on the surface of mold and core (such as thick wall surface, near pouring risers, grooves and hot joints etc.). The thermal conductivity of sand mold is poor. The liquid metal on the surface of casting stays in liquid state for a long time, which makes the deep part of mold wall close to or reach the temperature above the freezing point of metal. The liquid metal penetrates into the deep part of mold wall and forms bonded sand [13].Adhesive defects bring great difficulties to the cleaning process and increase the wear of cutting tools during subsequent processing.