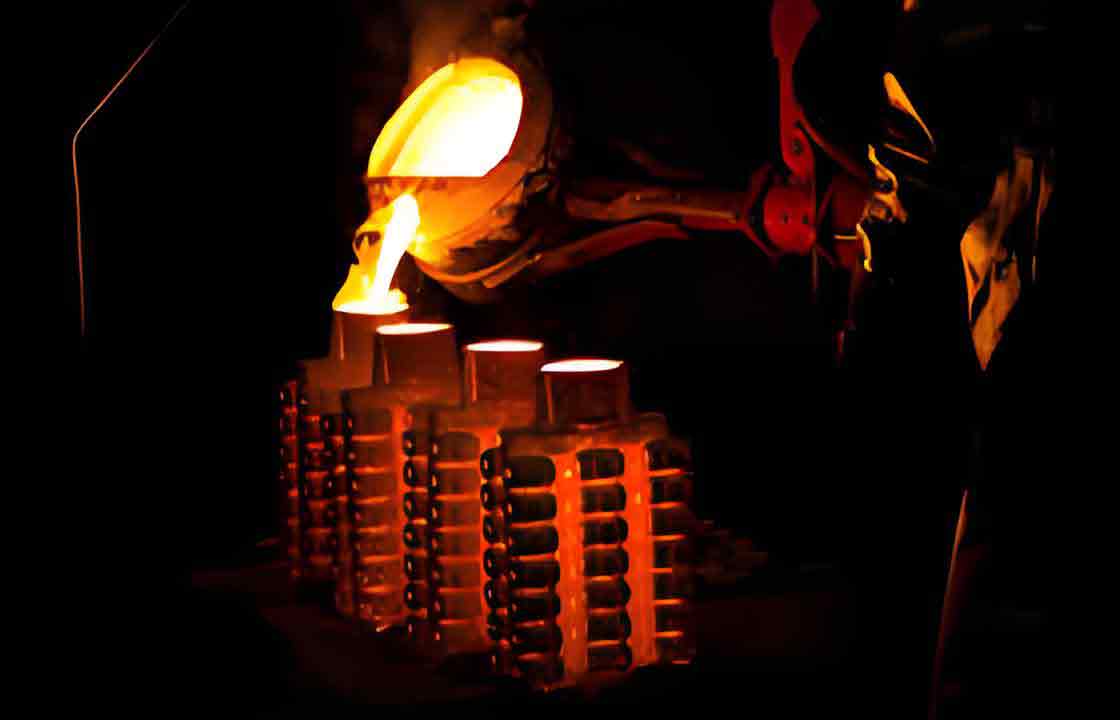
Investment casting is a manufacturing process renowned for its ability to produce intricate and high-precision components. The success of investment casting is heavily dependent on the choice of alloys used in the process. Different alloys offer distinct properties and performance characteristics, making them suitable for various applications across industries. This article provides a comparative analysis of investment casting alloys, focusing on their properties, performance, and applications.
Introduction to Investment Casting Alloys
Investment casting can utilize a wide range of alloys, each offering unique mechanical properties, corrosion resistance, and thermal stability. The selection of an alloy depends on the specific requirements of the component being produced, such as strength, weight, resistance to environmental factors, and cost.
Key Properties of Investment Casting Alloys
1. Mechanical Strength
The mechanical strength of an alloy determines its ability to withstand forces without deforming or breaking. This includes tensile strength, compressive strength, and yield strength.
2. Corrosion Resistance
Corrosion resistance is crucial for components exposed to harsh environments, such as chemicals, moisture, and extreme temperatures. Alloys with high corrosion resistance ensure longevity and reliability.
3. Thermal Stability
Thermal stability refers to an alloy’s ability to retain its properties at high temperatures. This is particularly important for applications involving heat, such as turbine blades and engine parts.
4. Machinability
Machinability describes how easily an alloy can be machined into the desired shape with minimal wear on tools and optimal surface finish.
5. Density
Density impacts the weight of the final component. Lightweight alloys are preferred in industries like aerospace and automotive for improved fuel efficiency and performance.
Comparative Analysis of Common Investment Casting Alloys
1. Stainless Steel Alloys
Properties: Stainless steel alloys are known for their excellent corrosion resistance, high strength, and good machinability. They also offer good thermal stability.
Performance: Stainless steels perform well in environments exposed to moisture and chemicals. Their strength and durability make them suitable for structural and load-bearing applications.
Applications: Stainless steel is used in aerospace components, medical devices, automotive parts, and industrial machinery. Specific grades like 316L and 17-4 PH are commonly used for their respective advantages in corrosion resistance and mechanical strength.
2. Aluminum Alloys
Properties: Aluminum alloys are lightweight, with good corrosion resistance and excellent machinability. They offer moderate strength and thermal stability.
Performance: Aluminum alloys perform exceptionally well in applications where weight reduction is critical. They also exhibit good resistance to corrosion in atmospheric conditions.
Applications: Aluminum is widely used in aerospace (airframe components), automotive (engine parts, wheels), and consumer electronics (housings, heat sinks).
3. Titanium Alloys
Properties: Titanium alloys are known for their high strength-to-weight ratio, excellent corrosion resistance, and good thermal stability. They are also biocompatible.
Performance: Titanium alloys are ideal for applications requiring high strength and low weight, as well as in environments with aggressive corrosive elements.
Applications: Commonly used in aerospace (aircraft components, fasteners), medical (implants, surgical instruments), and automotive (high-performance parts) industries.
4. Superalloys (e.g., Inconel)
Properties: Superalloys, such as Inconel, exhibit excellent high-temperature strength, corrosion resistance, and thermal stability. They are designed to retain mechanical properties in extreme environments.
Performance: Superalloys perform exceptionally well in high-temperature and high-stress conditions, maintaining their strength and resistance to oxidation and creep.
Applications: Used extensively in aerospace (turbine blades, combustion chambers), power generation (gas turbines), and chemical processing (reactor components).
5. Magnesium Alloys
Properties: Magnesium alloys are the lightest structural metals, with good strength and machinability. They have moderate corrosion resistance and thermal stability.
Performance: Magnesium alloys are suitable for applications where weight reduction is crucial, although they require protective coatings to improve corrosion resistance.
Applications: Widely used in automotive (gearbox casings, steering wheels), aerospace (aircraft interiors), and electronics (laptop cases, camera bodies).
Comparative Table of Investment Casting Alloys
Alloy Type | Mechanical Strength | Corrosion Resistance | Thermal Stability | Machinability | Density | Common Applications |
---|---|---|---|---|---|---|
Stainless Steel | High | Excellent | Good | Good | Moderate | Aerospace, Medical, Automotive, Industrial |
Aluminum | Moderate | Good | Moderate | Excellent | Low | Aerospace, Automotive, Electronics |
Titanium | High | Excellent | Good | Moderate | Low | Aerospace, Medical, Automotive |
Superalloys | Very High | Excellent | Excellent | Poor | High | Aerospace, Power Generation, Chemical |
Magnesium | Moderate | Moderate | Moderate | Excellent | Very Low | Automotive, Aerospace, Electronics |
Applications of Investment Casting Alloys in Various Industries
Aerospace
Investment casting is critical in aerospace for producing components that require high precision, strength, and resistance to extreme conditions. Titanium alloys are often used for structural parts and fasteners, while superalloys like Inconel are employed in turbine blades and combustion chambers due to their ability to withstand high temperatures and stress.
Medical Devices
The medical industry relies on investment casting for creating surgical instruments, implants, and dental devices. Stainless steel and titanium alloys are preferred for their biocompatibility, corrosion resistance, and strength.
Automotive
In the automotive sector, investment casting produces engine components, transmission parts, and lightweight structures. Aluminum and magnesium alloys are favored for their low weight, contributing to improved fuel efficiency and performance.
Power Generation
Superalloys are essential in power generation, particularly in gas and steam turbines, where high-temperature performance and resistance to oxidation are crucial. Investment casting ensures these components meet stringent performance standards.
Electronics
The electronics industry uses investment casting for producing components like heat sinks, housings, and structural parts. Aluminum and magnesium alloys are commonly used due to their good thermal conductivity, machinability, and lightweight properties.
Future Trends in Investment Casting Alloys
Development of New Alloys
Research is ongoing to develop new alloys that offer enhanced properties, such as higher strength, better thermal stability, and improved corrosion resistance. These advancements will expand the applications of investment casting in emerging industries like renewable energy and advanced manufacturing.
Sustainable Materials
The focus on sustainability is driving the development of eco-friendly alloys and processes. Recyclable materials, reduced energy consumption, and environmentally friendly practices are becoming increasingly important in investment casting.
Additive Manufacturing Integration
The integration of additive manufacturing with investment casting is revolutionizing the production of complex geometries and customized parts. This synergy allows for greater design flexibility, reduced lead times, and cost savings.
Conclusion
Investment casting remains a cornerstone of modern manufacturing, offering unparalleled precision, versatility, and efficiency. The choice of alloy plays a crucial role in determining the performance and suitability of cast components for specific applications. By understanding the properties and benefits of various investment casting alloys, manufacturers can select the best materials to meet the demanding requirements of industries such as aerospace, medical, automotive, power generation, and electronics.
As technology continues to evolve, the development of new alloys, sustainable practices, and the integration of additive manufacturing will further enhance the capabilities of investment casting. These advancements will drive innovation, improve performance, and expand the applications of investment casting in the future, ensuring its continued importance in the manufacturing landscape.