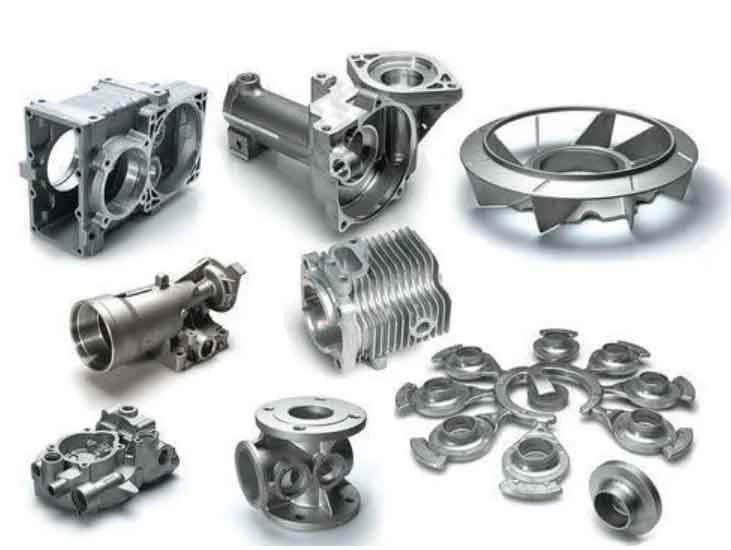
When selecting a casting material for a specific application, it is essential to consider the properties and characteristics of various materials to make the right choice. Grey cast iron is one of several casting materials available, and its selection should be based on the specific requirements of the application. Let’s compare grey cast iron with other common casting materials:
- Grey Cast Iron vs. Ductile Cast Iron:
- Grey Cast Iron: Offers good machinability, wear resistance, and vibration damping due to its graphite flakes. However, it is relatively brittle and has lower tensile strength compared to ductile cast iron.
- Ductile Cast Iron (Nodular Cast Iron): Provides better ductility, impact resistance, and tensile strength than grey cast iron due to its nodular graphite microstructure. Ductile cast iron is suitable for applications requiring higher strength and toughness.
- Grey Cast Iron vs. Steel:
- Grey Cast Iron: Offers good casting properties, cost-effectiveness, and machinability. It is suitable for applications where vibration damping, wear resistance, and low-cost casting are essential. However, it has lower tensile strength and impact resistance compared to steel.
- Steel: Provides higher tensile strength, toughness, and ductility than grey cast iron. Steel is suitable for load-bearing and high-stress applications, where high strength and impact resistance are critical. However, casting steel can be more challenging and costly compared to grey cast iron.
- Grey Cast Iron vs. Aluminum:
- Grey Cast Iron: Offers better wear resistance and thermal conductivity than aluminum. It is suitable for applications involving heat transfer, vibration damping, and wear resistance.
- Aluminum: Provides a higher strength-to-weight ratio and better corrosion resistance than grey cast iron. Aluminum is often preferred in lightweight and corrosion-prone applications, such as automotive components and aerospace parts.
- Grey Cast Iron vs. Cast Steel:
- Grey Cast Iron: Offers good castability, machinability, and vibration damping. It is more cost-effective for large castings and applications where the benefits of graphite flakes are essential.
- Cast Steel: Provides higher strength, toughness, and ductility than grey cast iron. It is suitable for applications requiring high mechanical properties and where cast iron’s brittleness is a concern.
- Grey Cast Iron vs. Brass/Bronze:
- Grey Cast Iron: Offers higher wear resistance and machinability compared to brass and bronze. It is preferred in applications where high strength and wear resistance are essential.
- Brass/Bronze: Provides better corrosion resistance and higher electrical conductivity compared to grey cast iron. Brass and bronze are often used in applications requiring good corrosion resistance and electrical properties.
The choice between grey cast iron and other casting materials depends on factors such as mechanical requirements, cost considerations, casting complexity, and environmental conditions. Engineers should thoroughly assess the specific needs of the application and consider the advantages and limitations of each material to make the most appropriate selection. Additionally, casting process capabilities and available foundry expertise should also be considered when making the final decision.