1. Electrochemical test
The results of electrochemical polarization test of grey cast iron and nodular cast iron are shown in Figure 1.
According to the polarization curve, solid grid and hollow triangle correspond to gray cast iron and nodular cast iron respectively. Cview2.0 is used to analyze the tafei fitting data of the polarization curve.
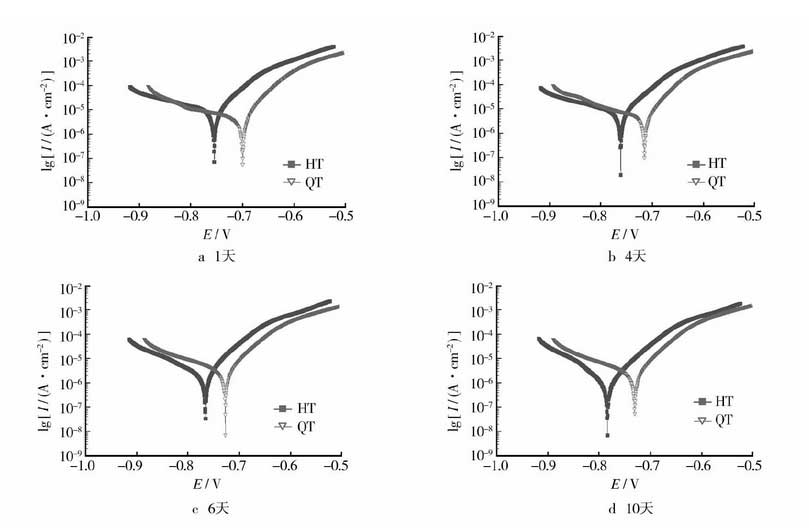
Figure 1 shows that the corrosion potential of nodular cast iron is higher than that of gray cast iron in the same group of tests. Combined with the data shown in Table 2, the corrosion potential, corrosion current and corrosion rate of nodular cast iron and gray cast iron can be quantitatively obtained. The corrosion rate behavior of the polarization curve on the 10th day was different from that of the previous groups, which may be caused by the too fast scanning rate of the polarization curve (1.00mv / s). In general, the corrosion potential of nodular cast iron is higher than that of gray cast iron, the corrosion current is smaller than that of gray cast iron, and the corrosion rate is smaller than that of gray cast iron. It can be seen that the slower the corrosion of ductile iron in 3% NaCl solution, the better the corrosion resistance.
It can be seen from Figure 2 that the impedance arc of nodular cast iron is larger than that of gray cast iron, which indicates that the corrosion resistance of nodular cast iron is greater than that of gray cast iron. According to the data analysis in Table 3, the RP value of nodular iron is larger than that of gray iron at the same time, indicating that the corrosion resistance of nodular iron is better than that of gray iron.
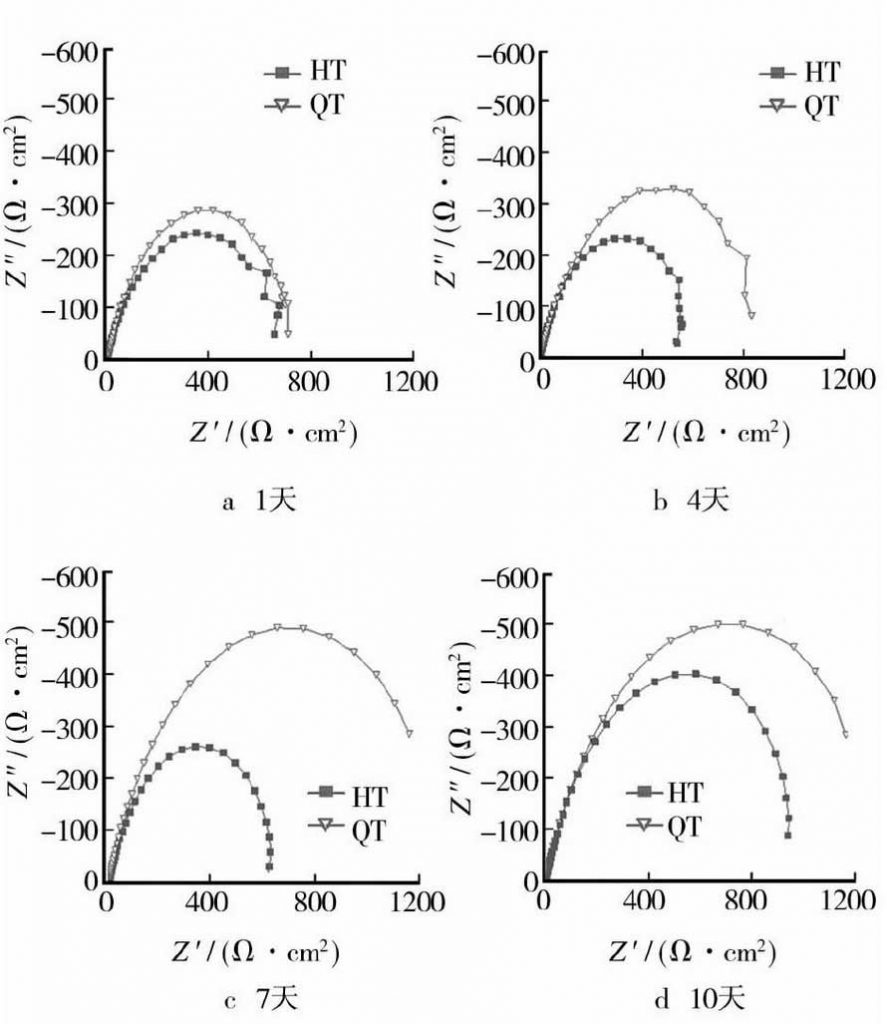
It can also be seen from the data of electrochemical test that the influence of electrochemical corrosion rate is also related to time. The corrosion rate of both gray cast iron and nodular cast iron is very high at the initial stage of corrosion. With the extension of time, the corrosion rate decreases gradually. Yang Haiyang and Huang Guiqiao [8] summarized the corrosion and fouling law of carbon steel in seawater with time. Literature [9-10] points out that this is related to the corrosion rust layer formed. The corrosion behavior and influencing factors of the metal under the rust layer are analyzed, which will not be discussed in this paper. In order to judge the corrosion resistance of nodular cast iron and gray cast iron more accurately, the hanging piece mass loss method is also used.
2. Coupon test
The macro corrosion of grey cast iron and nodular cast iron coupon test samples after cleaning and drying is shown in Figure 3.
In Figure 3, H1, H2 and H3 are all gray iron samples, Q1, Q2 and Q3 are ductile iron samples. It is obvious that the corrosion of two kinds of cast iron is all over the sample surface, and three samples of each kind of cast iron are corroded to the same extent, which all accord with the typical characteristics of uniform corrosion. In addition, the corrosion of gray cast iron is more obvious than that of nodular iron. Data obtained from the corrosion rate formula.
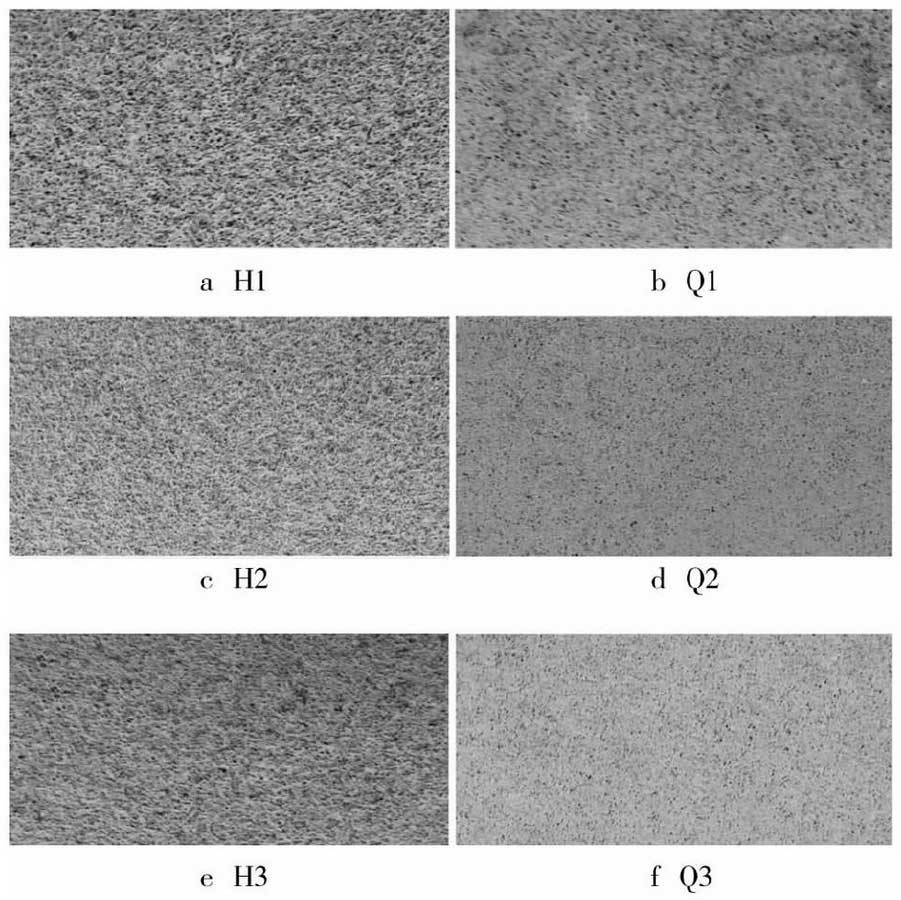
Both gray cast iron and nodular cast iron have mass loss, and the difference is obvious. The average mass loss of gray cast iron is about 1.7 times of that of nodular cast iron.
It can be seen from the above tests that although there is a certain difference in the corrosion rate between the electrochemical test and the coupon test of cast iron, the conclusion showing the corrosion performance of the two materials is the same. The corrosion rate of nodular cast iron is lower than that of grey cast iron, that is to say, the corrosion resistance of nodular cast iron is better than that of grey cast iron.
3. Result analysis
The mass fraction of salt in sea water is about 3.5%, which is a strong electrolyte solution with large conductivity and small resistance block. It has not only large micro battery activity, but also large macro battery activity. The corrosion rate of cast iron in sea water is quite high, because a large number of Cl – ions in sea water can hinder the production of anode passivation of cast iron, so the anode passivation of cast iron in sea water is difficult. Sodium chloride solution is not directly involved in the electrochemical reaction in the process of cast iron corrosion, but as a corrosion medium, it is used to transport electrons for the electrochemical reaction. The increase of the amount of electrons transferred by NaCl increases, and the corrosion rate increases.
The corrosion of cast iron in seawater is mainly the electrochemical corrosion process of oxygen depolarization, which is the main link of corrosion reaction.
Anode reaction: Fe → Fe2 + + 2e
Cathode reaction: 1 / 2O2 + H2O + 2e → 2OH-
In solution: Fe2 + + 2OH – → Fe (OH) 2
Further oxidation: 4Fe (OH) 2 + O2 + 2H2O → 4Fe (OH) 2
Iron hydroxide partially dehydrates to rust: 2Fe (OH) 2-2H2O → Fe2O3 · H2O or Fe (OH) 2-h2o → FeOOH
This is the main electrochemical corrosion process in cast iron [12-13]. It can be seen that the electrochemical corrosion of cast iron in seawater is mainly caused by the corrosion of metal matrix, and graphite does not participate in the reaction.
Graphite in gray cast iron is distributed in matrix structure in network form. In salt water and soil, the potential of iron is low, and it is corroded preferentially. There is only a sponge composed of graphite and rust, which is called graphitization and belongs to selective corrosion structure. There is no graphite skeleton like gray iron in nodular cast iron, so graphitization will not happen. However, graphitization corrosion is a slow process. If it is in the environment of rapid corrosion, gray cast iron will have uniform corrosion on the whole surface, rather than graphitization corrosion.
The matrix near the graphite on the surface of cast iron is corroded deeply. In a seawater spray corrosion test, cast iron is in an active corrosion state. The corrosion rate of various graphite forms cast iron from low to high is as follows: ductile iron, vermicular iron, A type graphite cast iron and dendrite graphite cast iron [14]. In cast iron, the potential of graphite is the highest, while that of cementite, pearlite and ferrite is decreased in turn. The microstructure of gray cast iron used in this paper is lamellar graphite and pearlite, while nodular iron is globular graphite and ferrite.
Pearlite is a mechanical mixture of ferrite and cementite. In the electrolyte solution, the gray cast iron based on pearlite is mainly composed of graphite and pearlite, and the ductile iron used in the test is mainly composed of graphite and ferrite. Obviously, there are more micro cells in gray iron than in nodular iron. As the cementite in pearlite can also become cathode, which accelerates the corrosion of its neighboring ferrite, the corrosion of gray cast iron is faster and stronger than that of nodular iron in seawater. According to the principle of thermodynamics, it can be concluded that a single structure is more stable than a variety of structures, and ferrite is more stable than pearlite. In conclusion, the corrosion resistance of nodular iron in NaCl solution is better than that of gray iron.
The larger the surface area of graphite in contact with the matrix, the higher the rate of electrochemical corrosion [16]. The graphite morphology of gray cast iron is uniform, fine and continuous, while that of nodular cast iron is spherical and isolated. Fe electrode, graphite electrode and surrounding electrolyte solution constitute numerous micro cells. Under the same conditions, the relative contact area of nodular cast iron is much smaller than that of gray cast iron. This means that the cathode area of nodular iron is smaller than that of gray iron, which leads to a smaller electrochemical corrosion rate of nodular iron. Therefore, the electrochemical corrosion tendency of nodular iron is lower than that of gray iron, and the corrosion resistance is higher.
conclusion
1) In 3% sodium chloride solution, nodular cast iron and gray cast iron are corroded uniformly, mainly the metal matrix structure. The corrosion is uniform and comprehensive, and there is no selectivity.
2) In 3% NaCl solution, the corrosion rate of nodular cast iron is lower than that of grey cast iron, and the corrosion resistance of nodular cast iron is better than that of grey cast iron.