The intermediate diaphragm / horizontal vertical pouring refers to that the mold is molded at the horizontal position, the cavity turnover is used for vertical pouring during pouring, and the intermediate diaphragm is inserted at the joint of the two liquid metals, as shown in the figure is the schematic diagram of flat vertical pouring bimetallic composite wear-resistant casting.
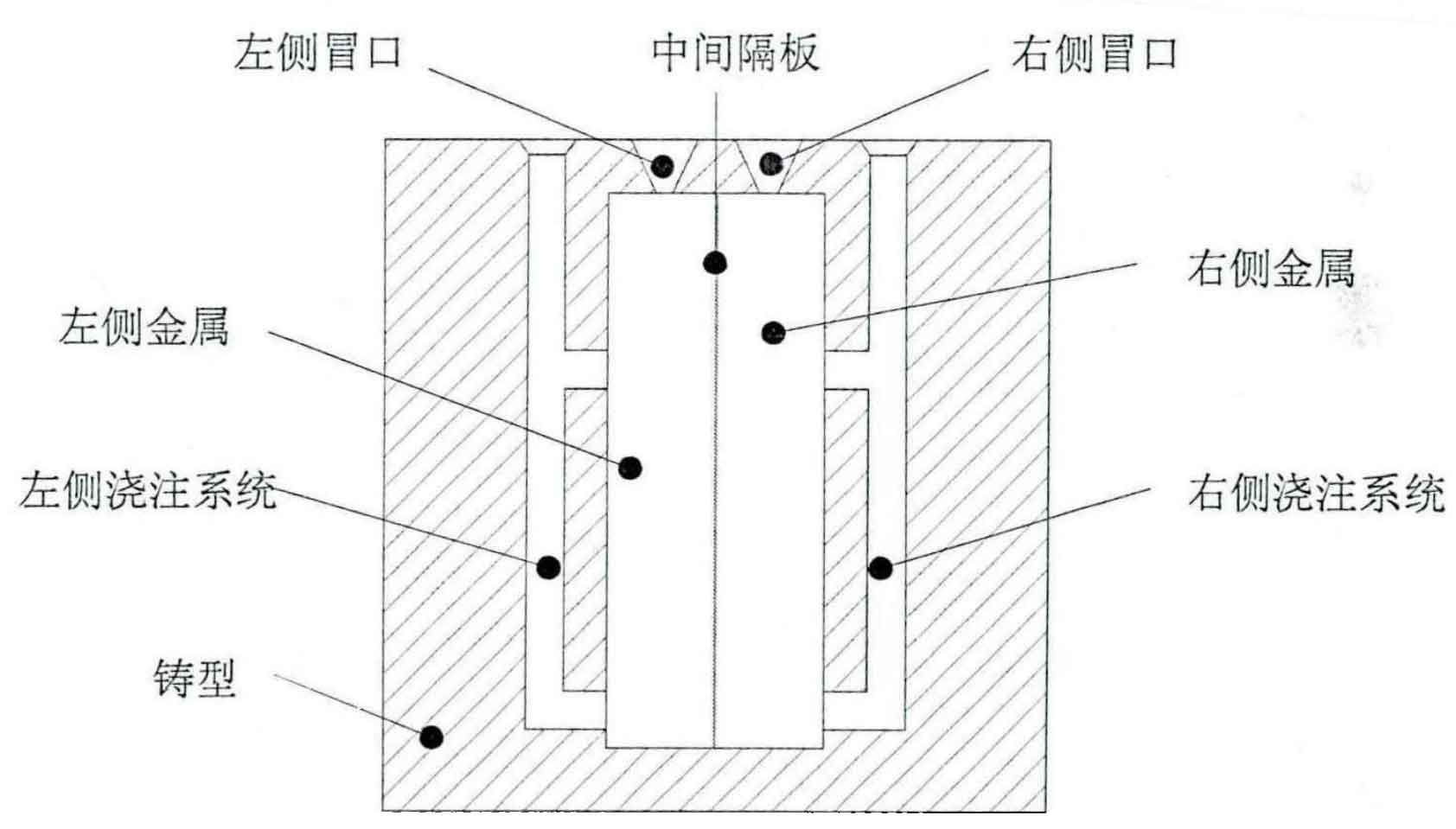
The process is characterized by the use of intermediate diaphragms. This material connection will be completed by the diaphragms heated in the casting process. A pouring riser system is set on both sides of the intermediate diaphragms to form a double pouring riser system. When designing the gating system, the direct impact of liquid metal on the intermediate diaphragm should be avoided. The pouring speed of the two metals is the process parameter that needs to be strictly controlled in the composite process. The metal liquid level on both sides of the diaphragm should rise slowly at an equal speed, and ensure that the two metal liquid levels maintain the same height at any moment, so as to reduce the liquid pressure difference on both sides of the diaphragm. The inclination of the diaphragm caused by the pressure difference will lead to the uneven thickness of the wear-resistant layer. In serious cases, it will make the high liquid level metal flow through the gap between the diaphragm and the mold cavity to the side with low liquid level, affecting the composition and microstructure uniformity of the casting.
In addition, when the two liquid metals rise at the same time, the rising speed also has a great impact on the quality of the bonding layer. If the rising speed is too fast, the inclusions and gases at the junction of the diaphragm and the liquid metal are not easy to be discharged and remain at the junction, affecting the strength of the bonding layer.