The forming method and equipment of composite squeeze casting are studied theoretically and experimentally. The main research contents and conclusions are as follows:
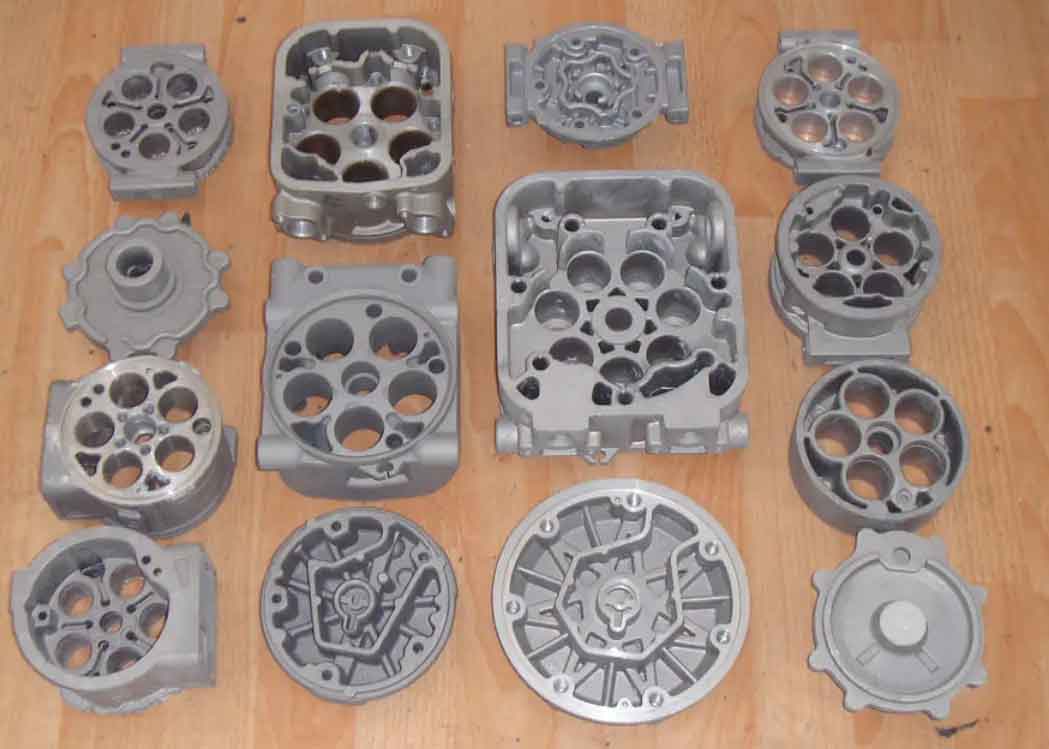
(1) The technical characteristics of direct squeeze casting and indirect squeeze casting and the problems easily occurred in the preparation of large parts are comprehensively analyzed. The forming method of composite squeeze casting is put forward. The overall design of the forming equipment of composite squeeze casting is carried out according to the characteristics of metal melt transmission in closed space and mold pre closing, The system model of composite squeeze casting forming system was established based on the prototype of composite squeeze casting forming equipment.
(2) The molten liquid conveying system is designed and manufactured according to the characteristics of large infusion volume, long infusion path, complex system and high requirements for heat preservation during the forming of large parts. The system includes pneumatic driving device, infusion pipeline and corresponding control software and hardware. The molten liquid conveying system is designed in detail, the temperature control model of the infusion pipeline is established, and the relevant parameters of the temperature maintaining device are determined. The gas pressure control test results of the molten liquid conveying system show that the actual pressure in the furnace basically coincides with the set pressure curve in the pressure boosting stage, and the actual pressure curve fluctuates around the design value in the pressure maintaining stage; The temperature of the infusion pipe is calibrated and the temperature of the pipe during infusion is tested. The test results show that the temperature of the molten metal flowing through the infusion pipe does not decrease significantly, the flow is normal and there is no blockage. The test results of the system show that the infusion problem of extrusion casting of large parts is well solved.
(3) A floating rigid support die is proposed for the composite squeeze casting of large parts. The modeling and analysis of the helix angle and extrusion compression of the floating structure are carried out. The design method of this kind of die and the calculation method of key parameters are summarized. ADAMS software is used to simulate and analyze the motion of floating structure. The simulation results show that the motion of the moving coil is relatively stable under the condition of self weight or pressure drive, which is suitable for the forming of large parts.
(4) Based on the system model of the composite squeeze casting forming system, the simulation model of the production logistics system for large parts is established. The time sequence relationship of various devices in the production logistics system of composite squeeze casting and the idle rate of equipment are analyzed, and the technical ways to improve the productivity and equipment utilization are discussed. The simulation results show that the idle rate of auxiliary devices such as spraying hands and picking hands is relatively high, There is a large optimization space in the production logistics system, but the vacancy rate of each auxiliary device has little difference, which proves that these devices have good coordination. The simulation analysis of different large parts shows that the same production logistics system has good adaptability to different castings, and the utilization rate of each device is basically the same. Therefore, the loss degree of each device and the overall energy consumption of the system tend to be consistent, which is helpful to further improve the composite squeeze casting system of large parts.
(5) According to the system design scheme, the composite squeeze casting forming system was designed and manufactured, and the forming test of large Al Cu wheel hub was carried out. The test results show that the appearance of the formed casting is complete and smooth, and there are no shrinkage cavity, air hole and other defects inside, and the average tensile strength basically meets the requirements. The composite squeeze casting method has a faster pressure build-up speed, which is beneficial to improve the quality of castings. On the premise of giving full play to the characteristics of the floating rigid support mold, the quantitative mold filling is basically ensured. The precision and performance index of the large wheel hub parts formed by the system basically meet the design requirements, which verifies the feasibility, effectiveness and practicability of the system.