Understanding and resolving casting defects requires a comprehensive approach that covers various aspects of the casting process. Here is a comprehensive guide that outlines the key steps involved in understanding and resolving casting defects:
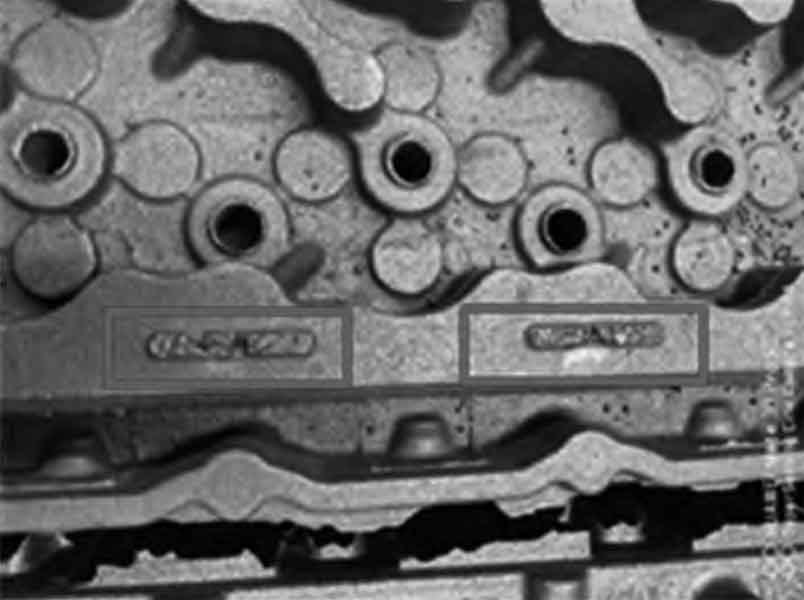
- Defect Identification:
- Familiarize yourself with common casting defects, including porosity, shrinkage, gas inclusions, cold shuts, misruns, sand inclusions, cracks, and dimensional inaccuracies.
- Conduct thorough visual inspections, employ non-destructive testing (NDT) techniques, such as radiography, ultrasonic testing, and liquid penetrant testing, to identify defects.
- Utilize advanced techniques like computerized tomography (CT) scanning or 3D scanning for in-depth defect analysis.
- Defect Classification:
- Categorize casting defects based on their types, causes, and locations within the casting.
- Classify defects as internal or external, surface or subsurface, and categorize them as shrinkage-related, gas-related, or solidification-related defects, among others.
- Determine the severity of defects based on their impact on structural integrity, functionality, and appearance.
- Root Cause Analysis:
- Perform a detailed root cause analysis to identify the underlying factors contributing to casting defects.
- Consider various aspects, including design flaws, process parameters, material characteristics, mold preparation, and environmental conditions.
- Utilize tools like the 5 Whys technique, fault-tree analysis, or fishbone diagrams to systematically analyze the causes and their interdependencies.
- Process Optimization:
- Utilize computer simulation software to optimize the casting process and minimize defects.
- Conduct solidification analysis, flow simulation, and thermal modeling to optimize gating and riser design, identify potential defects, and improve process parameters.
- Fine-tune process variables such as pouring temperature, cooling rates, mold coatings, and inoculants to optimize the casting process.
- Material Selection and Quality Control:
- Select suitable materials based on the casting requirements and characteristics of the final product.
- Ensure proper material specifications and work with reputable suppliers to maintain consistent material quality.
- Implement stringent material testing and inspection protocols to verify compliance with specifications and identify potential material-related defects.
- Mold Preparation and Maintenance:
- Pay attention to mold preparation and maintenance practices to minimize defects caused by mold interactions, inadequate venting, or erosion.
- Clean molds thoroughly, apply appropriate coatings, and ensure proper drying to prevent defects like surface roughness or metal/mold reactions.
- Regularly inspect and maintain molds to address wear, damage, or degradation issues that could impact casting quality.
- Quality Assurance and Control:
- Establish a comprehensive quality assurance program that includes documented procedures, inspection protocols, and testing methodologies.
- Conduct in-process inspections, dimensional checks, and non-destructive testing at critical stages of the casting process.
- Implement statistical process control (SPC) techniques to monitor process variability and detect deviations from acceptable quality standards.
- Corrective and Preventive Actions:
- Implement effective corrective and preventive actions (CAPA) to address identified defects and prevent their recurrence.
- Document and communicate lessons learned from defect analysis and root cause investigations.
- Continuously improve the casting process by implementing process modifications, training programs, and ongoing monitoring and evaluation.
- Collaboration and Continuous Learning:
- Foster collaboration among casting engineers, designers, operators, and quality control personnel to exchange knowledge and insights.
- Encourage continuous learning and professional development to stay updated with new technologies, materials, and best practices in the casting industry.
- Participate in industry forums, conferences, and workshops to learn from experts and share experiences with peers.
By following this comprehensive guide, manufacturers can gain a deeper understanding of casting defects, effectively resolve them, and continuously
Pages: 1 2