When the chemical composition of molten iron is constant, the smaller the casting modulus, the higher the amount of P in nodular iron matrix. According to the equilibrium phase diagram of Fe-C, there is about 11.2% high carbon phase Fe3C in P, which will have a significant effect on the austenitizing process and the dissolution and diffusion of carbon atoms in austenite. As shown in the figure is the correlation between matrix type of as cast ductile iron and carbon content in austenite.
It can be seen that when t γ is low (880 ℃), the carbon content in austenite of nodular iron with pearlite matrix is higher than that of nodular iron with ferrite matrix after austenitizing treatment. However, when the t γ is high (920 ℃, 960 ℃), more carbon elements are more easily enriched in the high temperature austenite after austenitizing the nodular iron with ferrite matrix. This is mainly due to the fact that pearlite preferentially decomposes and releases carbon atoms above the upper limit temperature of AC in the process of austenitizing, thus forming a high concentration of carbon rich region in the matrix Due to the low T γ, high activation energy of carbon atom diffusion and limited thermal movement ability, more carbon is dissolved in austenite. Therefore, the carbon content in high temperature austenite of nodular iron with pearlite as the main structure is higher than that of nodular iron with ferrite as the main structure.
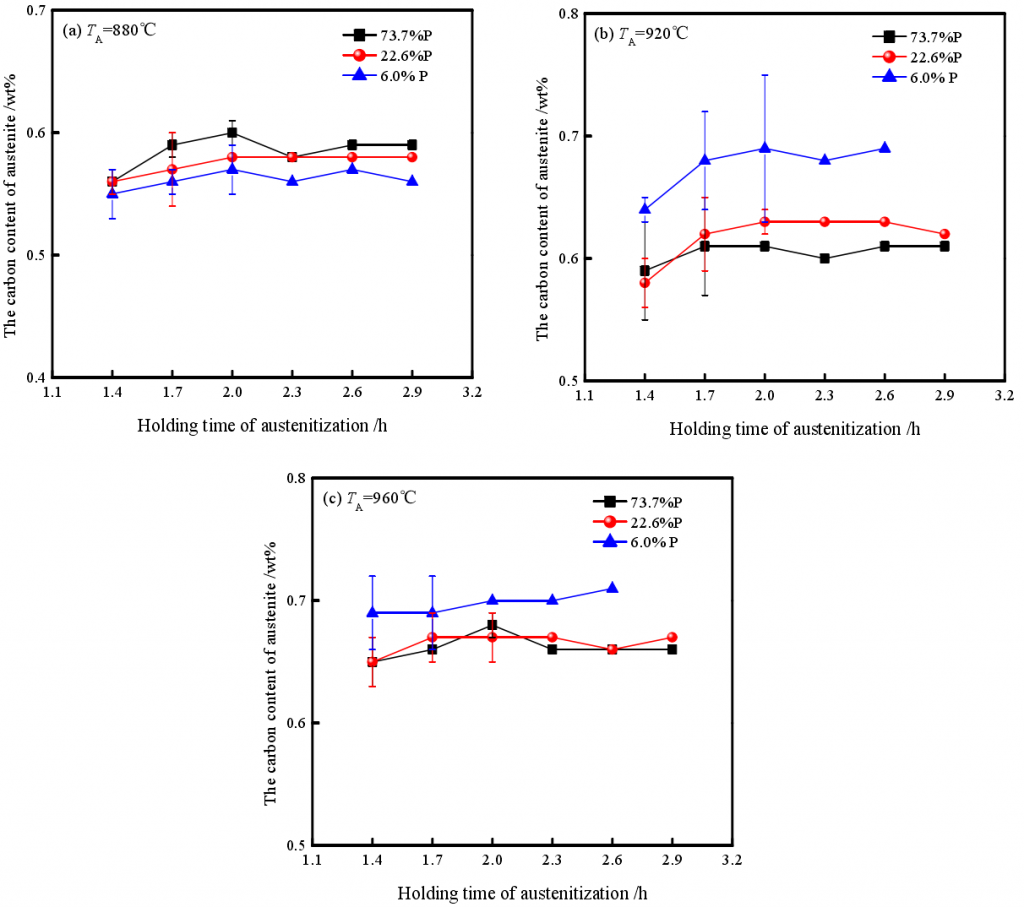
When t γ is high, on the one hand, the solid solubility of C element in austenite increases, on the other hand, the number of activated C atoms increases, and its diffusion ability is significantly enhanced. The dissolution and diffusion process of graphite surface, especially the fine spot graphite, is accelerated, which leads to the increase of solubility in austenite. This process is also aggravated by the increase of casting modulus, the increase of carbon content in ferrite, the decrease of graphite ball number, the increase of ball spacing, and the decrease of carbon atom deposition probability on the surface of large graphite ball.
In addition, no matter how the casting modulus and the amount of pearlite change, the carbon concentration in austenite does not change significantly after 1.7h holding time. This indicates that austenitizing temperature is a significant factor to determine the carbon concentration in austenite. Moreover, the maximum solid solubility of C in high temperature austenite is only 0.71% when t γ = 960 ℃, which is obviously lower than 0.6% ~ 1.2% (800 ~ 920 ℃) predicted in Fe-C equilibrium phase diagram. This is mainly due to the fact that silicon atoms occupy some positions in the austenite lattice, which causes the phase boundary of austenite to shift to the left, and the solubility of carbon in austenite decreases. For example, when the content of silicon in Fe-C alloy is 2% or 4%, the carbon content at eutectoid point is reduced to 0.6% and 0.4%. This is consistent with the carbon content of 0.57% ~ 0.71% in high temperature austenite when silicon content is 2.78%.