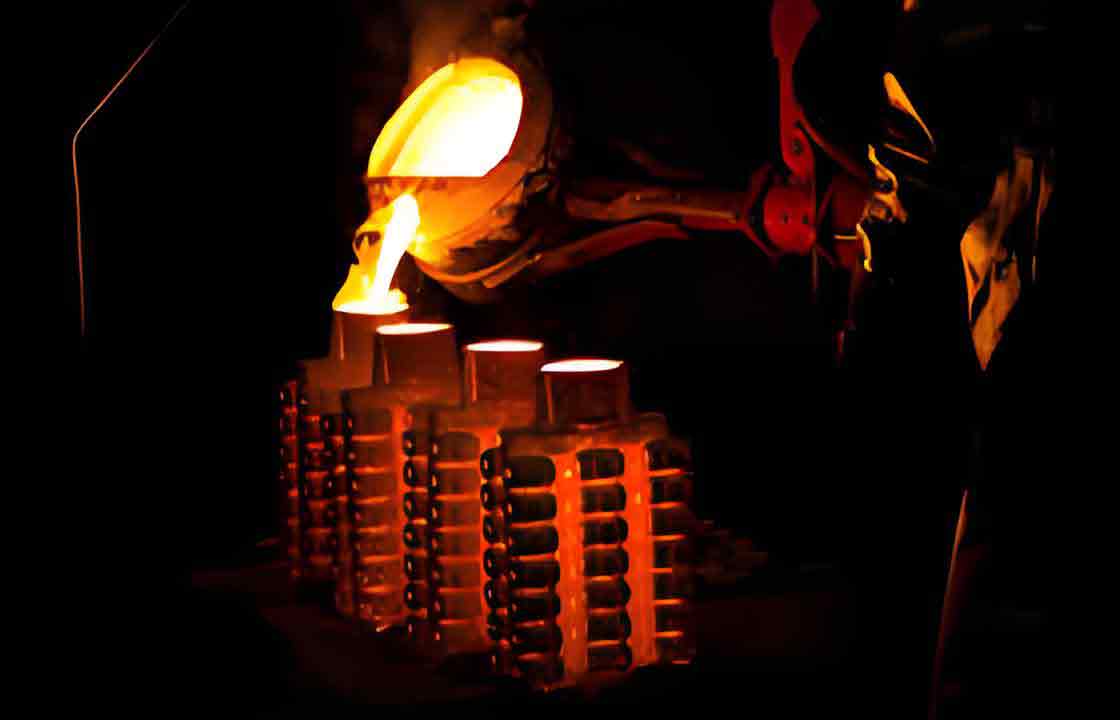
Investment casting is versatile and precise manufacturing process used to produce intricate metal parts. For industries that require large quantities of complex components, finding cost-effective solutions for high-volume production is essential. This article explores various strategies and techniques to optimize investment casting production, reduce costs, and maintain high quality.
Introduction to Investment Casting
Investment casting is a process that involves creating a wax model of the desired part, coating it with a ceramic shell, and then melting out the wax to create a mold cavity. Molten metal is poured into this cavity, and once the metal solidifies, the ceramic shell is removed to reveal the cast part. This process is ideal for producing components with intricate geometries and fine details.
Key Steps in Investment Casting
- Pattern Creation: Making a wax model using injection molding or manual carving.
- Assembly: Attaching multiple wax models to a central wax sprue to form a tree-like structure.
- Shell Building: Dipping the wax assembly into a ceramic slurry and coating with sand to build a strong ceramic shell.
- Dewaxing: Heating the ceramic shell to remove the wax, leaving a hollow cavity.
- Metal Pouring: Pouring molten metal into the ceramic mold.
- Shell Removal: Breaking away the ceramic shell to reveal the metal casting.
- Finishing: Cleaning and removing any excess material from the casting.
Strategies for Cost-Effective High-Volume Production
To achieve cost-effective high-volume production in investment casting, it is important to focus on optimizing each step of the process. Here are some key strategies:
1. Optimizing Pattern Creation
Techniques:
- Injection Molding: Using high-quality injection molds to produce wax patterns quickly and accurately.
- Automation: Implementing automated wax injection systems to reduce labor costs and improve consistency.
Benefits:
- Reduced labor costs.
- Increased production speed.
- Consistent and precise wax patterns.
2. Efficient Shell Building
Techniques:
- Rapid Shell Building: Using advanced ceramic materials and automated dipping systems to accelerate the shell building process.
- Process Optimization: Implementing process controls to ensure consistent shell thickness and strength.
Benefits:
- Faster shell production.
- Improved shell quality and consistency.
- Reduced material costs.
3. Advanced Dewaxing Techniques
Techniques:
- Autoclave Dewaxing: Using autoclaves to remove wax efficiently and reduce the risk of shell cracking.
- Microwave Dewaxing: Implementing microwave technology for faster and more energy-efficient dewaxing.
Benefits:
- Reduced energy consumption.
- Minimized shell damage.
- Faster dewaxing process.
4. Optimized Metal Pouring
Techniques:
- Automated Pouring Systems: Using robotic pouring systems to ensure precise and consistent metal pouring.
- Temperature Control: Implementing advanced temperature control systems to maintain optimal metal pouring temperatures.
Benefits:
- Reduced metal waste.
- Consistent casting quality.
- Improved process efficiency.
5. Efficient Finishing Processes
Techniques:
- Automated Finishing: Using automated grinding, polishing, and cleaning systems to reduce labor costs and improve consistency.
- Surface Treatment: Implementing surface treatments such as shot blasting and chemical finishing to enhance surface quality.
Benefits:
- Reduced finishing time.
- Improved surface quality.
- Lower labor costs.
Cost-Effective Techniques in Investment Casting
Table: Cost-Effective Techniques and Their Benefits
Technique | Description | Benefits |
---|---|---|
Injection Molding | Producing wax patterns using high-quality molds | Reduced labor costs, increased speed, consistent patterns |
Rapid Shell Building | Using advanced ceramics and automation | Faster production, improved shell quality, reduced costs |
Autoclave Dewaxing | Efficient wax removal using autoclaves | Reduced energy use, minimized shell damage, faster process |
Automated Pouring Systems | Robotic systems for precise metal pouring | Reduced waste, consistent quality, improved efficiency |
Automated Finishing | Automated grinding, polishing, and cleaning | Reduced labor costs, improved consistency, better surface quality |
List: Key Benefits of Cost-Effective Investment Casting
- Reduced Production Costs: Lower material and labor costs through automation and process optimization.
- Increased Production Speed: Faster production cycles enable higher output and meet high-volume demands.
- Improved Quality: Consistent and precise manufacturing processes result in higher quality castings.
- Energy Efficiency: Advanced techniques such as microwave dewaxing and temperature control reduce energy consumption.
- Minimized Waste: Optimized pouring and finishing processes reduce material waste and enhance sustainability.
Case Studies: Successful Implementation of Cost-Effective Solutions
Case Study 1: Automotive Industry
An automotive manufacturer implemented automated wax injection and robotic metal pouring systems to produce high-precision engine components. By optimizing the pattern creation and metal pouring processes, they achieved significant cost savings and improved production speed. The use of advanced dewaxing techniques further reduced energy consumption and enhanced the overall efficiency of the production line.
Case Study 2: Aerospace Sector
A leading aerospace company adopted rapid shell building techniques and autoclave dewaxing to produce complex turbine blades. The use of advanced ceramics and process automation enabled faster shell production and improved shell quality. Additionally, automated finishing systems ensured consistent surface quality and reduced labor costs, resulting in high-quality castings at a lower overall cost.
Case Study 3: Medical Device Manufacturing
A medical device manufacturer utilized automated grinding and polishing systems to produce orthopedic implants. By implementing efficient finishing processes, they reduced production time and improved the surface finish of the implants. The use of surface treatments such as shot blasting and chemical finishing further enhanced the corrosion resistance and biocompatibility of the implants, ensuring high-quality products for the healthcare industry.
Conclusion
Achieving cost-effective high-volume production in investment casting requires a comprehensive approach to optimizing each step of the process. By implementing advanced techniques and automation in pattern creation, shell building, dewaxing, metal pouring, and finishing, manufacturers can significantly reduce production costs, increase output, and maintain high-quality standards. Continuous advancements in investment casting technologies and processes ensure that manufacturers can meet the growing demands of various industries while remaining competitive in the market.
Investment casting remains a vital and versatile manufacturing method for producing complex and high-precision metal components, and with the right cost-effective strategies, it can deliver exceptional value and performance for high-volume production needs.