Lost wax casting, also known as investment casting, is a sophisticated process that has been utilized for centuries to create precision parts, from jewelry to industrial components. With the rise in demand for high-volume production, manufacturers face the challenge of maintaining quality while minimizing costs. This article explores several cost-effective strategies that can be implemented in lost wax casting production to enhance efficiency and reduce expenditure.
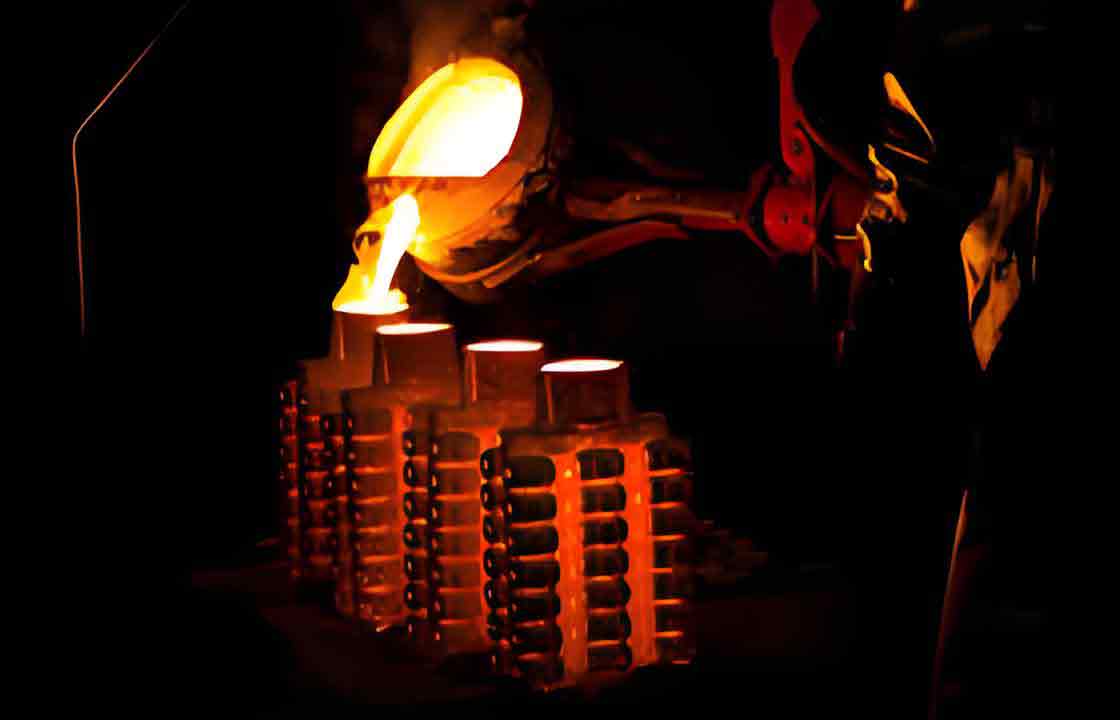
1. Optimization of Material Usage
Selecting the Right Materials
The choice of materials in lost wax casting has a significant impact on both the cost and quality of the finished products. Here are key considerations:
- Wax Selection: Using reusable waxes can reduce material costs significantly.
- Metal Selection: Opt for metals that melt at lower temperatures to reduce energy costs.
Material Efficiency Techniques
Efficient use of materials not only reduces waste but also lowers costs:
- Recycling Wax: Implement systems for wax recovery and reuse.
- Sprue Optimization: Design sprues to minimize metal usage without compromising the mold integrity.
2. Technological Advancements
Automation in Lost Wax Casting
Automation can streamline various stages of the casting process, from wax pattern production to the assembly of molds. Key benefits include:
- Reduced Labor Costs: Automation decreases the need for manual labor, which is often the most significant expense in manufacturing.
- Increased Consistency: Automated processes ensure that each part is cast with the same specifications, reducing the rate of defects.
Innovative Software Solutions
Using advanced software for simulation and process management can significantly enhance production efficiency:
- Simulation Software: Predicts defects and allows for mold adjustments before casting.
- Process Management Software: Monitors production stages to optimize workflow and resource allocation.
3. Energy Efficiency
Improving the energy efficiency of the casting process can lead to substantial cost savings. Consider the following strategies:
- Energy-Efficient Furnaces: Invest in furnaces that use less energy to reach casting temperatures.
- Optimized Heating Cycles: Tailor heating cycles to specific metals to avoid excessive energy use.
4. Workforce Training and Management
Well-trained staff can significantly enhance production efficiency and product quality. Key strategies include:
- Skill Development Programs: Regular training sessions to improve the skills of the workforce.
- Incentive Programs: Motivational programs that encourage workers to meet or exceed production targets.
5. Scale Economies
Taking advantage of economies of scale can reduce costs in high-volume lost wax casting production. Strategies to consider:
- Bulk Purchasing: Buy materials in bulk to negotiate lower prices.
- Shared Resources: Collaborate with other manufacturers to share facilities and resources.
6. Quality Control and Reduction of Waste
Implementing rigorous quality control measures can reduce the cost incurred from defective parts. Consider the following methods:
- Advanced Inspection Techniques: Use high-precision tools to inspect castings.
- Continuous Improvement Programs: Implement feedback loops to improve the process continuously.
Conclusion
By adopting these cost-effective solutions, manufacturers engaged in high-volume lost wax casting production can achieve significant savings while maintaining, or even enhancing, the quality of their products. The key to success lies in the strategic integration of technology, efficient resource management, and continuous improvement. Through these methods, the lost wax casting process remains a viable and competitive manufacturing technique in the modern industrial landscape.