Lost wax casting is widely used in various industries due to its ability to produce high-precision components. However, the process can be costly, and optimizing these costs is crucial for maintaining competitiveness in the market. This article explores several strategies for cost optimization in lost wax casting, providing detailed insights and practical approaches for industrial applications.
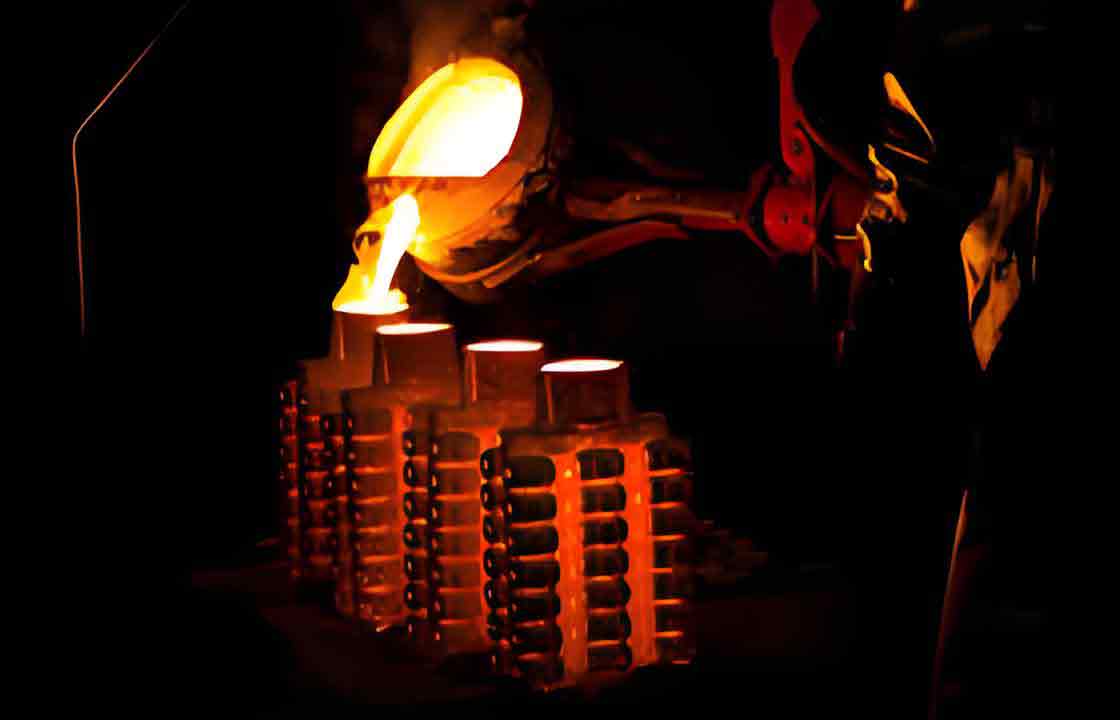
Introduction
Lost wax casting involves creating a wax pattern, which is coated with a refractory ceramic material to form a mold. Once the ceramic mold hardens, the wax is melted and drained away, leaving a cavity into which molten metal is poured. This process allows for the production of intricate and precise components, but it can be expensive due to material, labor, and energy costs. Implementing cost optimization strategies can significantly reduce expenses while maintaining or improving the quality of the castings.
Key Cost Optimization Strategies
- Material Efficiency
- Process Automation
- Energy Management
- Waste Reduction
- Supply Chain Optimization
- Quality Control Improvements
Material Efficiency
Strategies:
- Recycling Wax: Implementing a wax recycling system can reduce the need for new wax materials. Recycled wax can be cleaned and reused for pattern making.
- Optimizing Alloy Composition: Using cost-effective alloys that meet performance requirements can reduce material costs. Substituting expensive elements with cheaper alternatives without compromising quality is essential.
Benefits:
- Significant reduction in material costs.
- Enhanced sustainability through recycling and efficient use of resources.
Process Automation
Strategies:
- Robotic Pattern Assembly: Utilizing robots for assembling wax patterns can reduce labor costs and improve precision.
- Automated Mold Making: Automation in mold making can ensure consistency and reduce errors, leading to less rework and scrap.
Benefits:
- Reduced labor costs.
- Increased production speed and consistency.
- Lower defect rates and associated costs.
Energy Management
Strategies:
- Energy-Efficient Furnaces: Using modern, energy-efficient furnaces for melting metal can reduce energy consumption.
- Heat Recovery Systems: Implementing systems to recover and reuse heat from the casting process can lower overall energy costs.
Benefits:
- Lower energy bills.
- Reduced environmental impact.
Waste Reduction
Strategies:
- Lean Manufacturing Principles: Applying lean manufacturing techniques to minimize waste in the production process.
- Precision Casting Techniques: Improving the precision of casting techniques to reduce excess material usage and scrap.
Benefits:
- Reduced material waste.
- Lower disposal and recycling costs.
Supply Chain Optimization
Strategies:
- Strategic Sourcing: Partnering with reliable suppliers to negotiate better prices and ensure a steady supply of materials.
- Inventory Management: Implementing just-in-time (JIT) inventory systems to reduce holding costs and minimize waste from obsolete materials.
Benefits:
- Lower material costs.
- Reduced inventory carrying costs.
Quality Control Improvements
Strategies:
- In-Line Inspection Systems: Using real-time inspection systems to detect defects early in the production process, reducing rework and scrap.
- Statistical Process Control (SPC): Implementing SPC to monitor and control the casting process, ensuring consistent quality.
Benefits:
- Reduced rework and scrap costs.
- Improved product quality and customer satisfaction.
Comparative Table of Cost Optimization Strategies
Strategy | Key Actions | Benefits |
---|---|---|
Material Efficiency | Recycling wax, optimizing alloy composition | Reduced material costs, enhanced sustainability |
Process Automation | Robotic pattern assembly, automated mold making | Lower labor costs, increased production speed and consistency |
Energy Management | Energy-efficient furnaces, heat recovery systems | Reduced energy bills, lower environmental impact |
Waste Reduction | Lean manufacturing, precision casting techniques | Reduced material waste, lower disposal and recycling costs |
Supply Chain Optimization | Strategic sourcing, inventory management | Lower material costs, reduced inventory carrying costs |
Quality Control Improvements | In-line inspection, statistical process control (SPC) | Reduced rework and scrap costs, improved product quality |
Detailed Analysis
Material Efficiency
Recycling wax and optimizing alloy composition are fundamental strategies for reducing material costs. By setting up a wax recycling system, manufacturers can reclaim wax from used patterns and reuse it, significantly cutting down on the purchase of new wax. Optimizing the alloy composition involves substituting expensive elements with more cost-effective alternatives, provided that the substitution does not compromise the mechanical properties or performance of the castings.
Process Automation
Automation is a powerful tool for cost optimization. Robotic pattern assembly and automated mold making not only reduce labor costs but also enhance the precision and consistency of the casting process. This leads to fewer defects and less rework, contributing to overall cost savings. Moreover, automation can increase production speed, allowing manufacturers to meet higher demand without proportionally increasing labor costs.
Energy Management
Energy consumption is a significant cost factor in lost wax casting. Utilizing energy-efficient furnaces can substantially reduce energy bills. Additionally, implementing heat recovery systems allows manufacturers to capture and reuse waste heat, further lowering energy costs. These strategies not only reduce expenses but also align with environmental sustainability goals.
Waste Reduction
Applying lean manufacturing principles and improving precision in casting techniques can minimize waste. Lean manufacturing focuses on eliminating non-value-added activities, thereby reducing waste and increasing efficiency. Precision casting techniques ensure that the exact amount of material needed is used, reducing scrap and excess material.
Supply Chain Optimization
Strategic sourcing and inventory management are critical for optimizing supply chain costs. By partnering with reliable suppliers and negotiating better prices, manufacturers can secure materials at lower costs. Implementing JIT inventory systems reduces the need for large inventory stocks, minimizing holding costs and the risk of material obsolescence.
Quality Control Improvements
Investing in in-line inspection systems and SPC can significantly enhance quality control. Real-time inspection systems detect defects early, reducing the need for rework and scrap. SPC helps in monitoring and controlling the casting process, ensuring consistent quality and reducing the likelihood of defects. These improvements lead to lower costs associated with defective products and customer returns.
Practical Applications and Case Studies
Automotive Industry
In the automotive industry, cost optimization in lost wax casting is crucial for producing cost-effective and high-quality components such as engine parts and transmission housings. Implementing robotic pattern assembly and automated mold making has led to significant reductions in labor costs and improvements in production consistency.
Case Study:
- Transmission Housings: Automation in the production of transmission housings resulted in a 20% reduction in labor costs and a 15% increase in production speed, with a corresponding improvement in product quality.
Aerospace Industry
The aerospace industry demands high-precision and high-quality components. Utilizing energy-efficient furnaces and heat recovery systems has been effective in reducing energy consumption and costs while maintaining the stringent quality standards required.
Case Study:
- Turbine Blades: Implementing energy-efficient furnaces and heat recovery systems in the production of turbine blades led to a 25% reduction in energy costs and a significant improvement in the environmental footprint of the manufacturing process.
Industrial Machinery
For industrial machinery, components such as pump housings and valve bodies require durability and precision. Lean manufacturing principles and precision casting techniques have proven effective in reducing material waste and improving overall efficiency.
Case Study:
- Pump Housings: The adoption of lean manufacturing techniques in the production of pump housings resulted in a 30% reduction in material waste and a 10% increase in production efficiency.
Future Trends and Research
- Advanced Materials:
- Development of new alloy compositions that are cost-effective and meet performance requirements.
- Research into recyclable and biodegradable materials for wax patterns and ceramic molds.
- Smart Manufacturing:
- Integration of IoT and AI for real-time monitoring and optimization of the casting process.
- Use of predictive analytics to anticipate and mitigate potential defects and inefficiencies.
- Sustainable Practices:
- Adoption of more sustainable practices in the entire casting process, from material sourcing to waste management.
- Development of closed-loop systems to recycle and reuse materials and energy.
Conclusion
Cost optimization in lost wax casting is essential for maintaining competitiveness in the industrial market. By focusing on material efficiency, process automation, energy management, waste reduction, supply chain optimization, and quality control improvements, manufacturers can significantly reduce costs while maintaining or enhancing the quality of their products. Implementing these strategies not only improves profitability but also aligns with sustainability goals, ensuring the long-term viability of the lost wax casting process.