The production methods of engine connecting rods in China include traditional forging, casting and powder metallurgy, and the research and development of composite connecting rods. Since the 1990s, more than 90% of connecting rods have been produced by die forging. The casting process has basically not been adopted, and the rest are made by powder metallurgy. The materials of die forged connecting rod are mainly quenched and tempered steel and non quenched and tempered steel. In 1993, FAW consumed 35MnVS non quenched and tempered steel 2500t to produce CA6102 engine connecting rod, basically replacing the quenched and tempered steel connecting rod. As a kind of long shaft precision forging, connecting rod has strict requirements in shape, dimension, weight tolerance, internal organization and so on. Therefore, it has been regarded as a part that is difficult to forge.
At present, the new technologies of connecting rod forging mainly include:
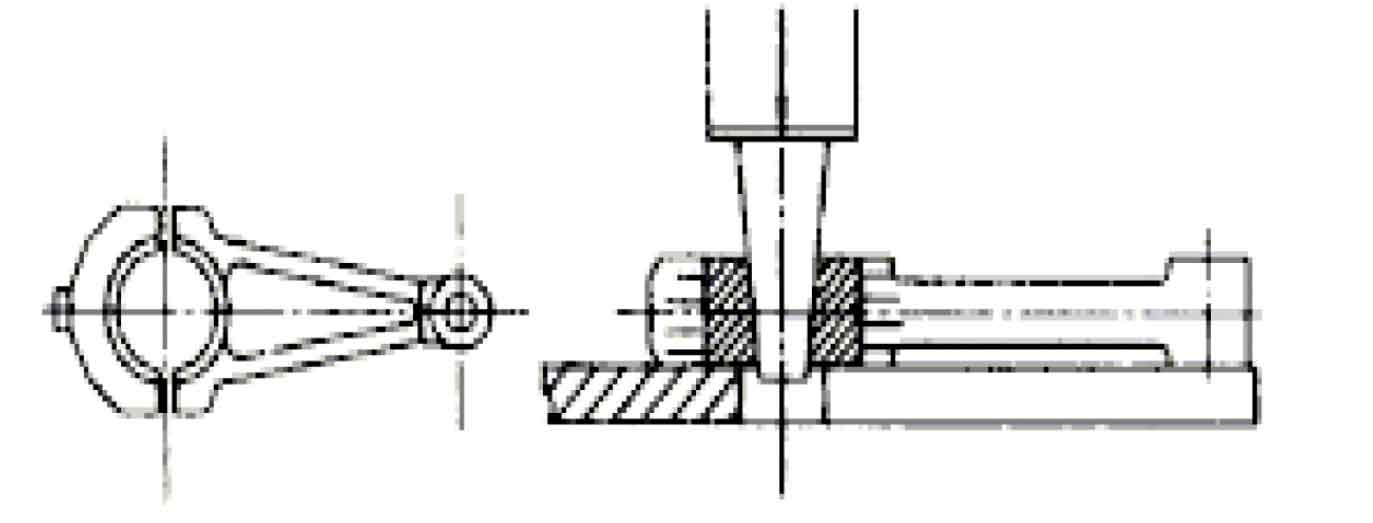
- The cross wedge rolling technology is used to make billets before die forging, which has the advantages of energy saving, material saving, high productivity and long die life. Using special CAD software, the computer aided design of cross wedge rolling die is realized, which can significantly improve the design efficiency and accuracy.
- The automation from vibration feeding of heating furnace, induction heating, material temperature sorting to cross wedge rolling machine blank is realized, which saves manpower, reduces labor intensity, and improves the internal quality of forgings.
- A compound die for cutting edge, punching skin and thermal correction is designed and developed, which can significantly improve the dimensional accuracy of connecting rod and save the number of processes and equipment.
- The connecting rod is made of non quenched and tempered steel, eliminating the heat treatment process of quenched and tempered steel. Non quenched and tempered steel is suitable for cracking processing, which changes the key production process of connecting rod processing, replaces split processing with overall processing, saves broaching and grinding processes of separation surface, and reduces the machining accuracy requirements of bolt holes. It has the advantages of less processing procedures, saving finishing equipment, saving materials and energy, high product quality and low production cost. The cracking process is a new process adopted by the connecting rod separation surface – the expanding and breaking process of the connecting rod separation surface, that is, the connecting rod cap is broken from the body and separated. It is not a traditional cutting method such as milling, sawing or pulling. Instead, two stress concentration grooves are pre machined at the fracture line of the connecting rod big end hole, and then a wedge-shaped indenter is used to move down and enter the connecting rod big end hole (there is a pair of semicircular sleeves between the connecting rod big end hole and the indenter). When the indenter moves down, a radial force is generated on the connecting rod big end hole, which causes cracks at the tip of the stress concentration groove, Under the continuous action of radial expansion force, the crack also continues to expand, and finally the connecting rod cap is separated from the connecting rod body. As shown in the figure. The practicability of connecting rod expanding and breaking process depends on the assembly of its separation surface. The ideal separation surface of the connecting rod and the connecting rod cap is brittle fracture without any plastic deformation, so its assembly ability is the best. The results show that sintered powder metal has good expandability. After the big end of connecting rod is expanded and broken, their separation surface is fully meshed, so there is no influence of separation surface and bolt hole processing error. The deformation of the big end of the connecting rod is related to the depth of the concentrated groove. The new technology of connecting rod splitting machining (also known as “expanding fracture” and “propping fracture”) developed in developed countries in the 1990s has changed the traditional connecting rod machining mode and is a major change to the traditional connecting rod machining, with its novel conception, economic operation and remarkable benefits.
- The traditional common die forging and machining methods have been difficult to meet the requirements of high quality, high precision, high efficiency, low consumption and low cost in today’s automobile, motorcycle and other industrial production. Therefore, in the mid-1960s, a new type of metal plastic forming process, powder forging, was initially developed and successfully forged into connecting rod and other parts for the first time. Powder forging technology is a highly competitive metal processing method with less and no cutting developed by the organic combination of conventional powder metallurgy process and precision forging. It takes metal powder as raw material, through pre forming and pressing, heating and sintering in protective atmosphere and as forging blank, and then it is forged on the press at one time and realizes precision die forging without flash. It has the same density as common die forgings Precision forgings with complex shapes. It not only has the advantages of good powder metallurgy formability, but also exerts the characteristics of forging deformation to effectively change the microstructure and properties of metal materials, making a new breakthrough in the production of powder metallurgy and forging technology. It is especially suitable for mass production of high-strength and complex structural parts. Therefore, it has a great development prospect of popularization and application in various industrial departments.
- It is predicted that the development trend of gasoline engine in the future is to give consideration to high output power and low fuel consumption. Therefore, the connecting rod requires lighter and lower friction loss while maintaining high reliability. However, considering the cost and productivity of these parts, it is very difficult to design light connecting rod with significantly reduced wall thickness compared with current products. Therefore, for example, the controllable forging (without casting defects) using high-strength aluminum alloy (powder metallurgy, etc.) is adopted. The fatigue strength is 2-2.5 times higher than the general one, and the quality dispersion of the blank is very small. In addition, the sintered aluminum alloy connecting rod has been applied in vehicles other than four-wheel vehicles.