1. Introduction
In the field of engine manufacturing, the cylinder head is a crucial component that directly affects the performance and reliability of the engine. The 12V190 cylinder head, used in a certain gas engine, is made of compacted graphite iron (CGI) due to its excellent heat resistance and fatigue resistance properties. However, the complex internal structure and thin-wall features of the cylinder head pose significant challenges in the casting process. This article focuses on the casting process design and production practice of the 12V190 cylinder head, aiming to achieve high-quality castings while reducing production costs.
2. Casting Process Design
2.1 Overall Casting Process
- Molding and Core-making: The casting process is designed with two castings per mold. Special tooling is used for the sand box, maintaining a sand-to-iron ratio of 1.66:1. The casting linear shrinkage rate is set at 1%. Machining allowances of 5 mm are designed for the combustion, intake, and exhaust surfaces. A combination of machine molding, machine core-making, and manual core-making methods is employed. The mold is sprayed with a water-based graphite coating, and the sand cores are brushed and dipped with an alcohol-based graphite coating. The mold assembly uses a layered core assembly process.
2.2 Core Materials and Processes
- Core Material Selection: Based on the product structure and existing process capabilities, the upper and lower molds and outer contour filling sand cores are made of furan resin sand. The internal cavities such as the water chamber and air passages are formed using precoated sand cores. The use of precoated sand cores ensures better dimensional accuracy of the internal cavities and facilitates easier removal of core sand during post-processing, ensuring the cleanliness of the water chamber and air passages.
- Bolt Hole Core: The cylinder head has six evenly distributed bolt connection holes from top to bottom, which are directly cast. The bolt hole cores are made of electrode graphite material. This not only provides sufficient strength to prevent core breakage during mold assembly but also has a chilling effect, preventing local porosity in the casting and ensuring a dense internal structure.
2.3 Mold Venting Process Design
- Venting Requirements: During the casting process, gases are generated when the furan resin sand and precoated sand are in contact with the high-temperature molten iron. If these gases cannot be effectively discharged from the mold cavity, porosity defects may occur in the casting. Therefore, proper mold venting is crucial.
- Venting Design: Five 30 mm×10 mm×300 mm flat risers are designed on the upper mold for gas escape. ø10 mm×300 mm vent holes are designed at the top of the triangular core, spark plug core, and auxiliary water chamber core. An exhaust groove is designed on the sidewall of the lower mold to assist in gas discharge from the side of the water chamber core head. Additionally, manual drilling of exhaust holes on the sidewall of the lower mold can be done if necessary to enhance the venting capacity during casting.
2.4 Gating System Design
- Gating System Principles: Considering the complex internal water chamber surfaces and thin-wall sections of the cylinder head, the gating system is designed based on the principle of balanced solidification. The aim is to achieve smooth filling of the molten iron, good slag removal, and a uniform temperature distribution in the mold.
- Gating System Components: A direct runner with a filter function and a runner well are designed. Slow-flowing horizontal runners are distributed on the upper and lower molds, with the molten iron flowing through the “overlapping” connection of the upper and lower molds. A layered and dispersed “stepped” ingate system is designed to allow the molten iron to enter the cylinder head casting. The sectional area ratio of the gating system is ∑A_inner:∑A_cross:∑A_down = 1:1.5:0.53. This design ensures smooth filling, effective slag removal, and a uniform temperature field in the mold cavity, reducing the risk of casting defects such as slag inclusions, cold shuts, and porosity.
2.5 Melting and Pouring Process
- Melting Composition Control: The melting process aims to achieve a high carbon equivalent, low phosphorus and sulfur content, and a certain manganese content. Considering the thin-wall sections of the cylinder head, the carbon content is controlled at the upper limit.
- Inoculation and Vermicularizing Treatment: The tapping temperature is controlled between 1510°C and 1550°C. Vermicularizing treatment is carried out by adding the treatment agent into the ladle during tapping. After vermicularizing, an inoculant is added on the surface of the molten iron for inoculation. Once the inoculation is complete, 0.1% – 0.15% of cryolite powder is added on the surface of the molten iron, and the slag is removed at least 4 – 5 times using perlite. The pouring temperature is controlled between 1360°C and 1390°C, with a pouring speed of 20 – 25 s per mold and a pouring weight of 200 kg per mold. During pouring, attention is paid to gas venting and slag blocking to ensure a smooth and orderly process. After pouring, the mold is cooled for 12 hours before opening and cleaning.
3. Process Testing and Validation
3.1 Mold and Tooling Preparation
After the casting process design, molds and tooling such as metal molds are fabricated. Subsequent process testing and validation are carried out based on the actual situation.
3.2 Molding, Core-making, and Coating Operations
All operations in the molding, core-making, and coating processes are carried out in accordance with the requirements of the process design. The mold assembly follows the principle of “from outside to inside, from bottom to top,” with the internal resin sand filling cores and precoated sand cores assembled in four layers. The outer contour filling sand cores are placed first, followed by the placement of round steel chaplets at the center of the lower mold core seat. Then, the cores are placed layer by layer according to the process requirements. The joint surfaces between the lower water chamber core head and the lower core seat, and between the auxiliary water chamber core and the lower water chamber core, are bonded with foundry glue. The amount of glue used is carefully controlled to ensure a firm bond without any overflow. During the core-setting process, a wall thickness gauge is used to check the wall thickness of key internal parts, and any issues are promptly addressed. After core-setting, the assembled mold is stacked and transported to a drying oven for drying.
3.3 Melting and Pouring
Melting is carried out in a 5 t medium-frequency induction furnace. The initial pouring temperature is set at the upper limit of the pouring temperature requirement, which is 1390°C. The pouring process follows the principle of “slow-fast-slow” to ensure a smooth and stable pour. The actual pouring time is 23 s per mold. The gas venting and slag blocking operations during pouring are correct, and no common problems such as “boiling” of the riser (commonly known as “riser gas blow”) occur.
3.4 Product Validation
- Chemical Composition and Mechanical Properties: According to the technical requirements and test specifications of the cylinder head, a series of tests are carried out on the trial-produced products. The chemical composition, mechanical properties, and microstructure of the separately cast samples are tested and found to meet the relevant requirements of the product material specifications. The results are shown in Tables 1 and 2 and Figure 5.
- Dimensional Inspection: The dimensions of the trial-produced cylinder head are inspected using a coordinate measuring machine. The results show that the contour dimensions of the cylinder head meet the process design requirements, and the machining allowances on the combustion, intake, and exhaust surfaces are reasonable.
- Internal Structure Inspection: The internal density of the first trial-produced cylinder head is inspected by dissection. The inspection reveals that the internal structure of the dissected section is dense, with no porosity or other casting defects. However, during the measurement of the internal water chamber and air passage dimensions, it is found that the local wall thickness between the spark plug hole and the air passage in the lower water chamber of the cylinder head is relatively thin, with an actual measured thickness of only 3 mm (Figure 6), while the product technical requirements specify a minimum thickness of 8 mm. This indicates a risk of thin-wall thickness in future production and non-compliance with the drawing requirements.
3.5 Analysis and Improvement of Wall Thickness Issue
- Problem Analysis: The reason for the thin wall thickness is that there is no sand core positioning at the bottom of the spark plug hole core in the cylinder head. The round steel chaplet only provides support for the sand core, and after core-setting, the position of the sand core may deviate in the mold cavity. During pouring, the spark plug hole core is prone to shifting due to the static pressure and buoyancy of the molten iron, resulting in a thinner wall thickness between the spark plug hole and the air passage in the lower water chamber.
- Improvement Measures: The structure of the spark plug hole sand core is improved by designing a process core head (Figure 7). A core rod is pre-placed in the hot box during core-making to increase the strength of the core head. At the same time, the process of using round steel chaplets to support the sand core is eliminated. This improvement ensures accurate positioning of the spark plug hole sand core during core-setting and enables the core head to provide support, preventing core displacement during pouring due to the static pressure and buoyancy of the molten iron.
3.6 Re-verification after Improvement
After implementing the improvement measures, another trial production of the cylinder head is carried out. During the mold assembly process, the spark plug hole sand core can be accurately positioned after bonding with the auxiliary water chamber core. The dissected inspection of the trial-produced cylinder head shows that the wall thickness of the water chamber and air passage is uniform, with an actual measured thickness of approximately 7 – 8 mm (Figure 8). The improvement measures are effective, successfully resolving the issue of thin wall thickness between the spark plug hole and the air passage in the lower water chamber of the cylinder head.
4. Conclusion
4.1 Significance of the Casting Process
- The use of multiple core materials such as furan resin sand, precoated sand, and electrode graphite in the casting process effectively addresses the challenges of complex internal cavities and high dimensional accuracy requirements of the cylinder head. The combination of machine molding, hot box core shooting, and manual core-making methods improves production efficiency and reduces production costs to some extent.
- The application of the slow-flowing, layered, and dispersed “stepped” gating system with a molten iron filtering function effectively solves the problem of molten iron purification during pouring, reduces local overheating in the mold, ensures a uniform temperature field, and reduces the risk of casting defects such as slag inclusions, cold shuts, and porosity.
- Reasonable control of the chemical composition, especially precise control of carbon, silicon, and sulfur content, improves the casting processability of the CGI material, facilitates the casting of thin-wall structures, ensures a dense internal structure of the cylinder head, effectively controls the vermicularization rate within 85% – 95%, and enhances the thermal conductivity of the CGI material, thereby improving the heat fatigue resistance of the cylinder head.
- The improvement of the sand core structure ensures the stability of individual sand cores during pouring, effectively solves the critical issue of local thin-wall thickness affecting the performance of the cylinder head, and lays a solid process foundation for the mass production of the cylinder head.
4.2 Future Prospects
Through the design and verification of the casting process for the compact and thin-wall 12V190 cylinder head, a cylinder head that meets the customer’s technical standards has been successfully developed. The overall process design concept is reasonable, and effective measures have been taken to solve the practical problems encountered during the trial production process, achieving the expected results. This research provides valuable experience and reference for the casting process design and production of similar cylinder head products in the future. It is expected that further optimization and innovation in the casting process will continue to improve the quality and performance of cylinder head castings, meeting the increasingly stringent requirements of the engine manufacturing industry.
In summary, the casting process design and production practice of the 12V190 cylinder head have achieved significant results in terms of product quality and cost control. The continuous improvement and innovation in the casting process will contribute to the development and application of high-performance engine components.
Table 1. Chemical Composition Analysis Results
C | Si | Mn | P | S | Cu | |
---|---|---|---|---|---|---|
Technical Requirements | 3.65 – 3.85 | 2.2 – 3.0 | 0.5 – 0.8 | ≤0.040 | ≤0.030 | 0.5 – 0.7 |
Test Results | 3.77 | 2.63 | 0.73 | 0.031 | 0.010 | 0.66 |
Table 2. Mechanical Properties and Metallographic Test Results
Rp0.2/MPa | Rm/MPa | A/% | Vermicularization Rate/% | Matrix Structure | Hardness (HB) | |
---|---|---|---|---|---|---|
Technical Requirements | 300 | 240 | 1.5 | 60 | F + P | 170 – 217 |
Test Results | 402 | 330 | 4.0 | 85 | F + 45%P | 187 |
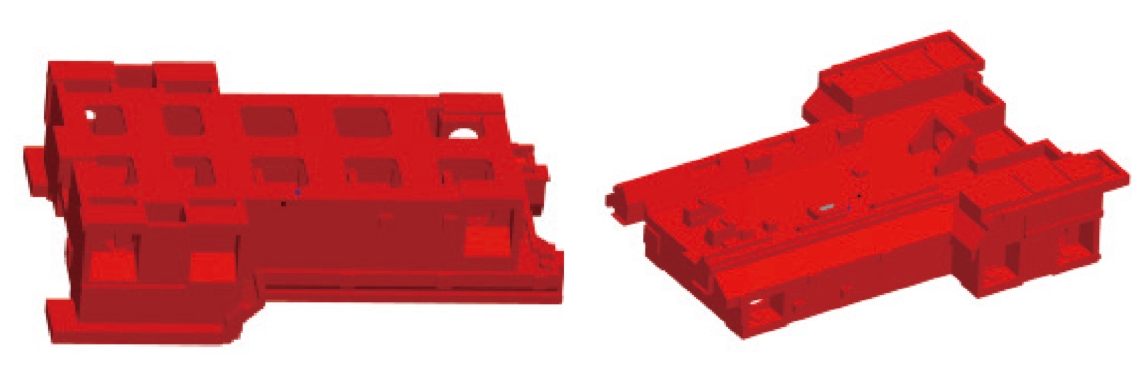