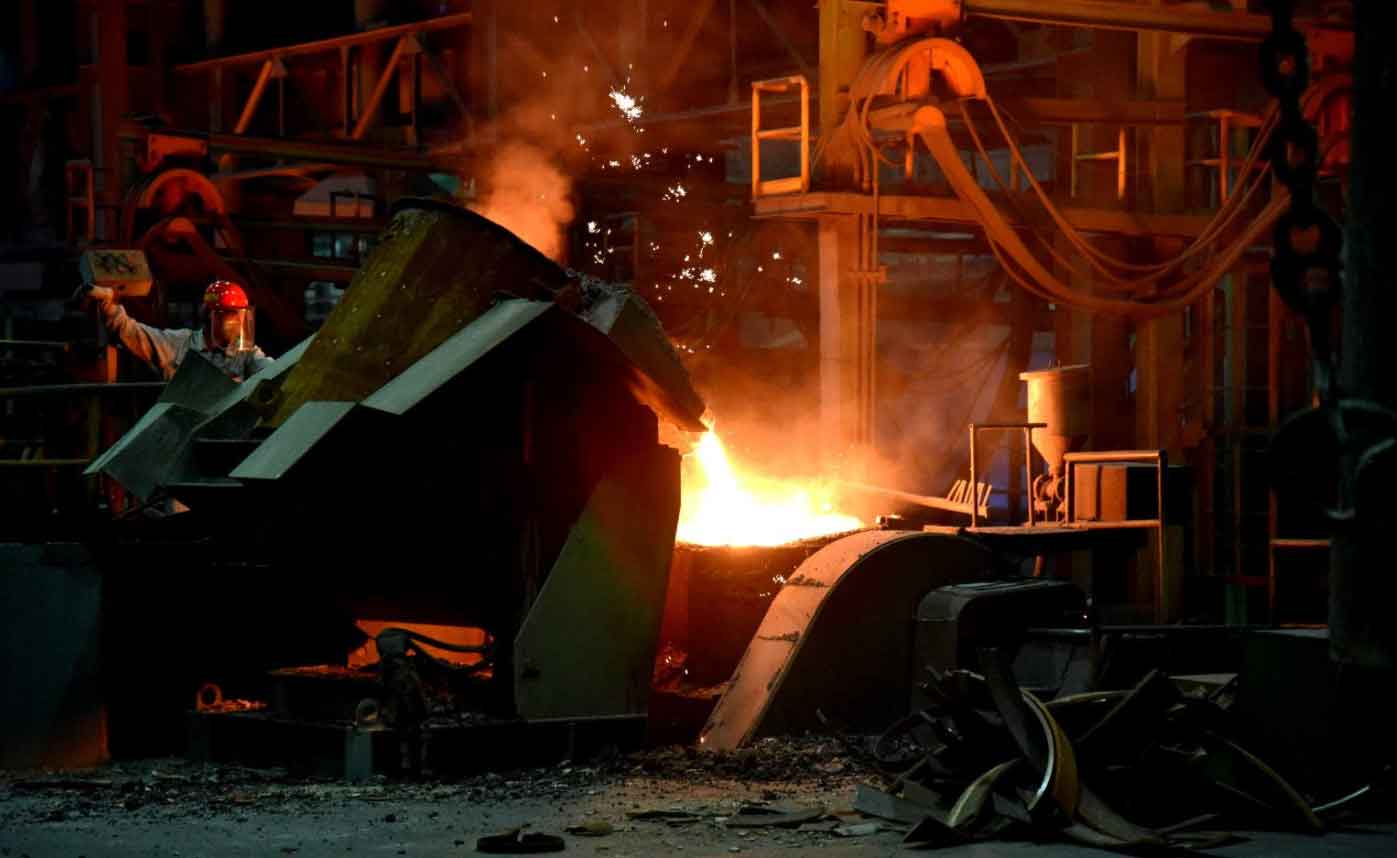
The production management and product control of castings in a foundry should gradually establish data-based and intelligent production under industry 4.0. Casting production is a relatively complex system engineering, during which there are physical and chemical changes, and many factors participate. In the traditional casting process, the process parameters involved in the process are a relatively wide range, and the experience of the production and management personnel also plays a great role. Therefore, our casting production is not particularly stable. After all, the production factors that people’s minds pay attention to are limited, and there are differences in personality due to different personnel involved in management and production. Therefore, we may not be able to accurately detect and correct the product quality fluctuations caused by changes in certain factors during casting production. At this time, the AI intelligent system is required to collect, display and analyze a large amount of production data, so that on the basis of a large amount of data, the system will open the self-learning function to find and correct the changed data, and achieve the goal of stable product quality.
1. Data collection
For the green sand mechanized molding casting process, the production data of five production departments (melting, molding, sand treatment, cleaning and core making) are collected in an all-round way. For example, the sand treatment department starts from the unpacking and desanding: the unpacking temperature of the casting, the temperature and humidity of the old sand after desanding. Collect these data and store them in a certain standard format. Of course, some data cannot be collected in real time and automatically, such as the mud content in the old sand. We can manually collect and input these data at a certain time. But more data will be obtained by installing sensors or by digital to analog conversion. In short, we will collect the data related to the casting production process first. The early stage of data collection requires a process. After 3-6 months of data collection, the database will gradually form and then gradually play its role.
All the collected data will form a huge database over time, and mathematical operations such as comparison and calculation will be carried out among the parameter data. Generally, we will upload the data to the cloud for data storage and calculation in the cloud space.
2. Data display
Data in the cloud space can be accessed at any time, but not all people have access to all data. The data owner can set access permissions according to the user group category. The web-based dashboard can display visual data in real time and generate reports automatically. Visitors can read real-time and historical real data within the right of access. The system will automatically draw tables, curves and other presentation forms on the basis of various data, so that huge data can be displayed to visitors intuitively and effectively, so that visitors can understand the development trend of each link and give research and judgment on possible future conditions.
The data system can support various portable communication ports, and users can easily understand and master the production dynamics of the foundry at any time. Strong database support provides a strong guarantee for our casting production. First of all, the process data identified by artificial intelligence will establish a link with the product quality data. There is a broader and more precise data base in the cloud space.
3. Data analysis
Cloud spatial data is not simply stored and displayed, but also has the functions of analysis and self-learning. Large scale casting is a production mode based on product quality and the yield of castings is the ultimate goal. Only in this way can the products have lower manufacturing costs and higher market competitiveness. The data-based AI intelligent system with the ability of analysis and self-learning will make the collected data effective. It can coordinate all the parameter data, deal with the infinitely complex logical relations, accurately find the changes of the parameter data collected during production and the impact on the product quality, and put forward suggestions on optimizing the overall process.
This principle of parameter data analysis and optimization is still based on the relatively successful casting formation theory that we have used for many years. The participation of AI data intelligent system is to compare and optimize these stored parameter data affecting casting production, which can give full play to its powerful analysis and calculation ability. And the data base is also a dynamic existence. The data collected in real time in our production will also be added to it, constantly enriching and improving the data base, so that we can obtain more powerful data support.
4. Intelligent control
The ultimate goal of AI data intelligent system is intelligent control, so as to realize black light factory. Based on the strong data support, the system will list all the most relevant parameters for the problems in casting production, and analyze and correct the relevant parameters until they return to the circle. When the equipment used does not have the automatic adjustment and correction function, we need to manually assist in the correction. If the mechanical equipment has the correction function, the system will automatically adjust and complete the correction. For example, in the process of mixing green molding sand, the compaction rate and wet compression strength of molding sand will be detected in real time. Once the compaction rate of molding sand is qualified but the wet compression strength is low, the system will make automatic correction adjustment based on the mud content of old sand, the proportion of effective clay and dead clay, the proportion of new sand added to the sand system in the near future, the strength and permeability of sand mold and other relevant parameters: the system will issue instructions to adjust the electric damper of the dust removal system, Increase the air volume to remove more dead ash; Start the new sand adding system to add new sand; Adjust the proportion of clay in molding sand mixing to make the deviation parameters tend to the normal value. Such changes of relevant parameters affecting casting quality in casting production can be automatically adjusted and corrected by the system.
The basic principle and application of the digital intelligent system in the production of modern foundry under industry 4.0 are briefly introduced in order to turn the data of foundry production into value and provide an idea for the development of modern foundry production.