Dimensional issues, such as warping and distortion, are common challenges in heat treatment processes. These problems can affect the dimensional accuracy, fit, and functionality of the treated components. Here are some approaches to dealing with dimensional issues in heat treatment:
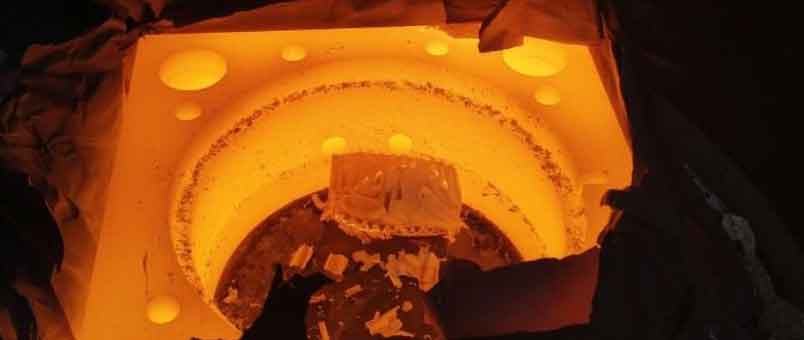
1.Proper Fixture Design:
Designing and using appropriate fixtures or jigs can help control the movement and shape of the components during heat treatment. Fixtures can restrict distortion and minimize warping by providing support and maintaining the desired shape.
2.Controlled Heating and Cooling Rates:
Implementing controlled heating and cooling rates can help minimize thermal gradients and reduce the likelihood of distortion. Gradual and uniform heating and cooling can promote even expansion and contraction, minimizing dimensional changes.
3.Symmetrical Loading:
Load components symmetrically in the heat treatment equipment to promote balanced heating and cooling. Uneven loading or asymmetrical placement can lead to differential thermal expansion, resulting in warping or distortion.
4.Stress Relief Annealing:
Conduct stress relief annealing after heat treatment to minimize residual stresses that can cause distortion. Stress relief annealing involves heating the component to a specific temperature and holding it for a sufficient time to relieve internal stresses.
5.Post-Heat Treatment Machining:
Incorporate post-heat treatment machining operations to correct dimensional deviations. Machining can help remove excess material, adjust dimensions, and achieve the desired tolerances and geometry.
6.Quenching Optimization:
Optimize the quenching process to minimize distortion. Consider factors such as quenching media selection, quench tank design, agitation methods, and part orientation to achieve uniform cooling and minimize thermal gradients.
7.Controlled Atmospheres or Protective Coatings:
Use controlled atmospheres or protective coatings during heat treatment to minimize the potential for surface oxidation or decarburization. Surface defects caused by these issues can contribute to dimensional problems.
8.Pre- and Post-Heat Treatment Machining Allowances:
Design components with appropriate pre- and post-heat treatment machining allowances to account for dimensional changes during the heat treatment process. This approach allows for subsequent machining operations to achieve the desired final dimensions.
9.Process Simulation and Modeling:
Utilize process simulation and modeling techniques to predict and optimize the heat treatment process, including potential dimensional changes. These tools can aid in understanding and minimizing distortion and warping issues.
10.Continuous Process Improvement:
Establish a feedback loop and continuously improve heat treatment processes. Analyze dimensional deviations, gather data, and implement corrective actions based on root cause analysis. Regular monitoring and process optimization can help mitigate dimensional issues.
It’s important to note that the specific approach to address dimensional issues will depend on factors such as the material being treated, component geometry, heat treatment method, and desired final dimensions. Collaborating with heat treatment experts, metallurgists, and design engineers can help develop effective strategies to minimize dimensional problems and achieve the desired dimensional accuracy.