1. Introduction
Crankshafts are crucial components in engines, especially in mining vehicles where they endure high – load and long – term operation conditions. The QT900 – 5 ductile iron crankshaft, with its specific mechanical properties, is widely used. However, the occurrence of fractures in these crankshafts can lead to serious consequences, such as equipment failures and production disruptions. In this study, we focus on a case where a mining vehicle’s crankshaft broke at the 7th and 8th cranks after 1269 hours of operation. By conducting a series of analyses, we aim to identify the root cause of the failure and propose effective improvement measures to enhance the quality of castings.
2. Failure Case Background
In July 2021, a four – cylinder crankshaft of a mining excavator suddenly fractured after 1269 hours of operation. After disassembly, it was found that the crankshaft broke into three parts at the 7th and 8th cranks. Additionally, the cylinder block’s rear end cracked, and the 4th connecting rod bent. The failed crankshaft was made of QT900 – 5 ductile iron and had undergone a strengthening process of fillet grooving and rolling + journal medium – frequency induction hardening.
Component | Condition |
---|---|
Crankshaft | Broken at 7th and 8th cranks |
Cylinder Block | Rear end cracked |
Connecting Rod | 4th connecting rod bent |
3. Experimental Methods and Instruments
To comprehensively analyze the failure of the crankshaft, a variety of experimental methods and advanced instruments were employed.
3.1 Experimental Instruments
- HX – HW8B High – Frequency Infrared Carbon – Sulfur Analyzer: Used to analyze the carbon and sulfur content in the crankshaft material, following the national standard GB20123 – 2006 “Determination of Total Carbon and Sulfur Content in Steel and Iron – Infrared Absorption Method after Combustion in a High – Frequency Induction Furnace”.
- Plasma 3000 ICP Spectrometer: Applied to analyze the content of other elements in the material, in accordance with the national standard GB/T 20125 – 2006 “Determination of Multi – Element Content in Low – Alloy Steels – Inductively Coupled Plasma Atomic Emission Spectrometry”.
- Hitachi S 3400 N Scanning Electron Microscope (SEM): Utilized to observe the surface morphology of the fracture and defect areas at a high magnification.
- JED – 2200 Energy – Dispersive Spectrometer (EDS): Combined with SEM, it was used to analyze the micro – area composition of the fracture and defect areas.
- Metallographic Microscope: Employed to examine the metallographic structure of the samples taken from the fracture area.
- E45 – 305 Electronic Universal Material Testing Machine: Used to test the mechanical properties of the crankshaft material.
- THBS – 3000DD Brinell Hardness Tester: Applied to measure the hardness of the crankshaft material.
3.2 Experimental Procedures
- Sampling: Samples were carefully taken from the fracture areas of the 7th and 8th cranks, including areas around the suspected defect and normal areas for comparison.
- Chemical Composition Analysis: The carbon, sulfur, and other element contents in the samples were determined using the corresponding spectrometers.
- Macroscopic Analysis: The fracture surfaces of the crankshaft were visually inspected to identify the fracture origin, propagation direction, and any obvious macroscopic defects.
- SEM and EDS Analysis: The samples were observed under SEM to obtain detailed surface morphology information. EDS was used to analyze the chemical composition of specific areas, especially the substances in the defect areas.
- Microscopic Organization Analysis: The samples were prepared for metallographic analysis. The metallographic structure around the defect and in normal areas was observed under a metallographic microscope to understand the material’s microstructure characteristics.
- Performance Testing: Tensile test bars were cut from the 6th crank, and hardness samples were taken from the large disc position to test the mechanical properties of the material.
4. Test Results and Analysis
4.1 Chemical Composition Analysis
The chemical composition analysis results of the failed crankshaft are presented in Table 1. By comparing the measured values with the technical requirements, it can be seen that the chemical composition of the crankshaft material meets the specified standards.
Element | Measured Value (%) | Technical Requirement (%) |
---|---|---|
C | 3.64 | 3.60 – 3.90 |
Mn | 0.5 | 0.30 – 0.50 |
Si | 2.16 | 1.90 – 2.40 |
P | 0.017 | ≤0.060 |
S | 0.004 | 0.004 – 0.02 |
Cr | 0.04 | ≤0.10 |
Mg | 0.04 | 0.02 – 0.06 |
Ce | 0.005 | ≤0.025 |
Cu | 0.55 | 0.40 – 0.60 |
4.2 Macroscopic Analysis
- Fracture Origin and Propagation: The crack source of the 7th crank was located at the intersection of the 7th crank and the 4th connecting rod lower dead – center rolling groove edge, near the surface of the 7th crank. The crack propagated at an approximately 45° angle to the axial direction of the crankshaft and finally led to instantaneous fracture near the 4th main journal fillet rolling groove edge. The fracture surface of the 7th crank showed distinct regions of crack source, propagation, and instantaneous fracture. The crack source was in the shape of a hole, which was elliptical, large inside and small outside, with a size of about 3mm x 7mm.
- Fracture Characteristics: The fracture surface of the 7th crank was smooth, flat, with no obvious plastic deformation, a bright color, and a metallic luster. There were few friction and impact marks, indicating that the 7th crank fractured rapidly after the engine was overloaded. The 8th crank’s fatigue cracks originated from the 4 – connecting rod fillet. The fracture surface was rough in the middle, with a dark color, no crystalline particles, and no metallic luster. The 8th crank also showed signs of rapid fracture, and its instantaneous fracture area was near the 5th main journal.
4.3 Scanning Electron Microscope (SEM) Analysis
- 7th Crank Hole Area: Under SEM, the hole at the crack source of the 7th crank was composed of two small holes, with smooth hole walls. There were several small cracks around the hole, and a small number of friction marks and fatigue stripes were visible at the hole edge. The bottom area of the hole was dark. EDS analysis showed that the main elements of the dark substance in the hole were C, O, and Fe, indicating the presence of oxidation in the hole.
- 7th Crank Raised Area: The raised area of the 7th crank fracture was severely worn, with most areas showing friction marks.
- 8th Crank: The fracture surface of the 8th crank near the 4 – connecting rod fillet showed a “river pattern” under SEM, with obvious cleavage characteristics, indicating cleavage fracture. The middle area of the 8th crank had a mixed fracture surface of cleavage and dimple, and there were no obvious casting defects such as shrinkage porosity and pores, suggesting that the fracture of the 8th crank was caused by instantaneous overload.
4.4 Microscopic Organization Analysis
- 7th Crank Hole Area: The metallographic structure around the hole of the 7th crank showed that the graphite was numerous, evenly distributed, and had a good roundness. The graphite nodularity grade was 2, and the graphite nodule diameter was 6. The area near the hole was composed of flake – like pearlite + a small amount of ferrite + graphite, with a pearlite content of 95%. A dark – colored substance with a thickness of 5 – 10μm was observed at the bottom of the hole. EDS analysis confirmed that the dark – colored substance was mainly composed of C, O, and Fe, and there was no problem of slag inclusion.
- 7th Crank Raised Area: The graphite in the raised area of the 7th crank was severely deformed due to friction, collision, and extrusion during the fracture process, changing from spherical to flaky. A martensite layer was found on the surface of the raised area after corrosion, indicating severe friction. There were also irregular holes in the area slightly below the surface of the raised area, which were connected to the surface by small worm – like holes, and the holes also contained oxide substances.
Crank | Sampling Area | Metallographic Structure | EDS Analysis Results |
---|---|---|---|
7th Crank | Hole area | Numerous graphite, evenly distributed, good roundness, graphite nodularity grade 2, graphite nodule diameter 6, flake – like pearlite + a small amount of ferrite + graphite, pearlite content 95%, dark – colored substance at the bottom of the hole | Main elements of dark – colored substance: C, O, Fe |
7th Crank | Raised area | Deformed graphite, martensite layer on the surface, irregular holes below the surface, holes contain oxide substances | Main elements of subs |
4.5 Performance Testing
The mechanical property test results of the crankshaft material are shown in Table 2. The measured values of yield strength, tensile strength, elongation, and hardness all meet the technical requirements.
Item | Yield Strength (MPa) | Tensile Strength (MPa) | Elongation Percentage (%) | Hardness (HBW) |
---|---|---|---|---|
Measured Value | 521 | 916 | 7.4 | 302 |
Technical Requirement | ≥460 | ≥820 | ≥4.5 | 250 – 320 |
5. Failure Cause Analysis
5.1 Formation of Invasive Porosity
The analysis results indicate that the casting defect at the fracture position of the 7th crank is an invasive porosity. The gas sources mainly come from the water in the molding sand and core sand, and the combustion of organic substances such as coal powder, starch in the molding sand, and resin and curing agent in the core sand, which produce water vapor, carbon monoxide, carbon dioxide, and other gases. These gases invade the surface layer of the casting at the intersection of the 7th crank and the 4th connecting rod lower dead – center rolling groove edge. At the beginning of metal solidification, the gas invades the liquid metal. As the casting shell starts to cool and solidify, and the gas volume and pressure continue to increase, the gas cannot flow outwards due to the solidified shell. Since the temperature inside the casting is higher, the metal has good fluidity and low resistance, so the gas flows inward, forming an invasive porosity with a large – inside – and – small – outside shape.
5.2 Impact of Invasive Porosity on Crankshaft Performance
The presence of invasive porosity not only reduces the effective bearing area of the crankshaft material but also causes local stress concentration, which deteriorates the mechanical properties of the defect area and significantly reduces the fatigue strength of the crankshaft.
5.3 Fracture Process of the Crankshaft
When the mining vehicle operates at full load, the bending and torsional stresses near the fillet of the crankshaft journal become too large. The stress exceeds the fatigue limit of the area with invasive porosity, which promotes the rapid formation and propagation of fatigue cracks. As a result, the 7th crank fractures instantaneously. After the fatigue fracture of the 7th crank, the crankshaft continues to rotate due to inertia, causing the 8th crank to be instantaneously overloaded in a short time, and then the 8th crank also fails and fractures instantaneously. This also leads to the cracking of the rear end of the cylinder block, the bending of the 4th connecting rod, and the fracture of the camshaft of the 4th cylinder.
6. Improvement Measures
Although the production process of the crankshaft meets the requirements, to prevent similar failures in the future, the following improvement measures are proposed:
6.1 Control of Molding Sand and Core Sand
Strictly control the content of gas – generating substances and moisture in the molding sand and core sand. The molding sand laboratory should test the volatile content of the molding sand daily. For ductile iron, the volatile content of the molding sand should be controlled within 2.3 – 2.5. If it exceeds the upper limit, the molding sand control room should be notified in a timely manner to adjust the molding sand ratio.
6.2 Optimization of Sand Mold Ventilation
Adjust the parameters of the automatic air – hole punching machine to increase the depth of the air – holes punched on the surface of the sand mold to 30mm from the cavity surface. This can enhance the exhaust capacity of the sand mold and facilitate the rapid discharge of gases generated during pouring.
6.3 Strengthening of Furnace Charge Management
Control the quality of furnace charges. The furnace charges must be dry and free of surface rust. During smelting, increase the high – temperature standing time of the molten iron. Raise the temperature of the electric furnace to 1500 – 1520°C and stop the power for 3 – 5 minutes. After spheroidization, increase the number of slag – skimming operations from 2 times to 3 times to reduce the amount of liquid slag in the molten iron.
7. Conclusion
- In this study, through a series of analyses including macroscopic inspection, SEM, metallographic microscopy, and EDS, it was determined that the hole – like casting defect at the intersection of the 7th crank and the 4th connecting rod fillet of the four – cylinder crankshaft was the crack source of the crankshaft fracture, and this defect was an invasive porosity. The main elements of the dark – colored substance in the hole were C, O, and Fe.
- The gases generated by the combustion of water, organic substances in the molding sand and core sand invaded the surface layer of the casting at the specific position of the 7th crank, forming invasive porosity.
- Although only the moisture of the molding sand and core sand and the quality of the furnace charges were improved in this study, without in – depth research on the crankshaft process, operation method, and materials, these aspects can be the focus of future research. By implementing the proposed improvement measures, it is expected to effectively improve the quality of QT900 – 5 ductile iron crankshafts and reduce the occurrence of similar failures.
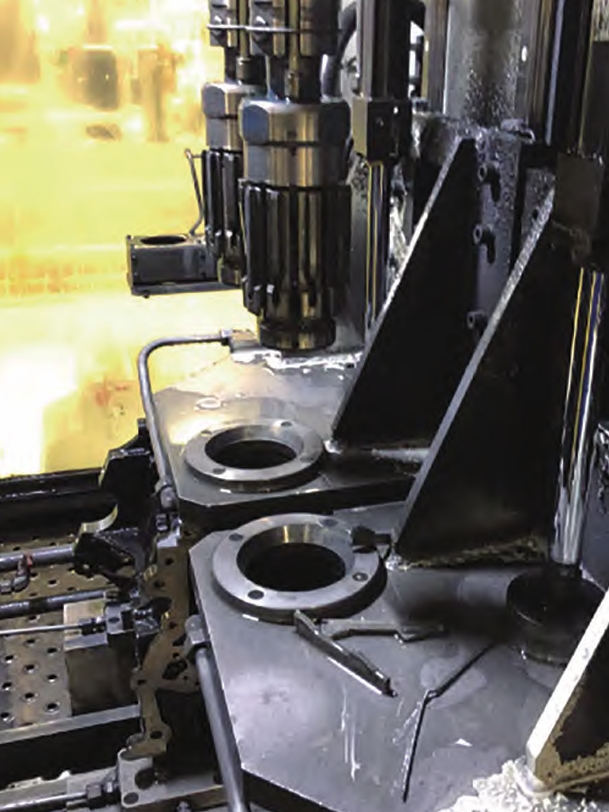