1 Inspection for fleshy defects of castings
The contour of the two blanks is clear, and there is no obvious shrinkage cavity in the isolated liquid phase area, but there is an obvious “sarcoma” in one part of the blank relative to the outer contour of the outlet box, as shown in the figure. Carefully observe the defect position, the shape is irregular, indicating that the coarse sugar is obviously mixed with sand particles. This part has an opening in the similar part of the outer contour of the motor shell, but there is no similar defect in other parts.
Cause analysis; in sand filling direction, the direction of sand falling is consistent with the direction of the runner. Through the diagram, we can see that there is a bar on each side of the defective parts. Although there are vibratory treatments after the sand fall, these two bars obstruct the movement of the sand particles, causing the compaction degree of this part not enough. Finally, the casting coating will be destroyed after the liquid metal enters, and the metal liquid will be mixed with the sand grains. Sarcomas formed after coagulation.
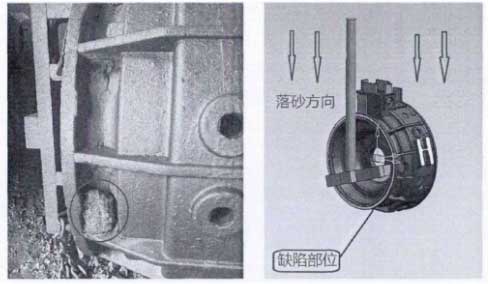
Solution: under the condition that the installation of motor shell parts will not interfere with this part, make an inclined plane of the defective part pit so that the sand can flow in. At the same time, when filling the sand, let the operator manually fill this part with some sand first. Under the control of the process, the defects of this part were eliminated by the subsequent casting.
2 Casting sintering
After solving the problem of the external mold of the casting, the internal wall thickness of the casting is checked by slicing after machining.
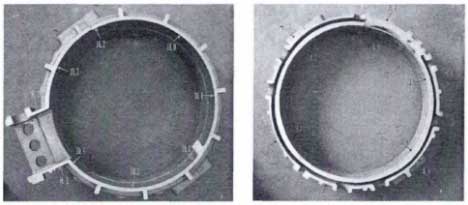
The design wall thickness of the small end face is 10 ± 0.5, and the anatomical result is ideal. The design wall thickness of the inner part of the water chamber reaches 7. The wall thickness of the water chamber is obviously not up to the standard. The sand core is seriously deformed, causing the inner wall to be thick and the outer wall to be too thin. Moreover, there is serious sintering near the water inlet in the upper right corner of the figure, and there is partial wall penetration.
Cause analysis: the water jacket core is too thin to bear the compaction pressure, resulting in the fracture of the sand core in the water inlet hole, resulting in sintering, wall penetration, and overall deformation after the fracture of the sand core, resulting in the uneven thickness of the inner and outer walls of the whole water chamber.
Solution: in the original design, only the core bone is added at the disconnection of the core head ring of the water jacket, and the strength of the core head is enough, but the part of the water jacket is too fragile. After research, it is decided to add a core bone with a diameter of 3.8 at the water inlet and outlet of the water jacket core, as shown in Figure 5-14. After the core bone is added, the strength of the water jacket core is effectively improved, and the sintering situation does not appear. After several rounds of trial production, the wall thickness of the water chamber has reached the standard.
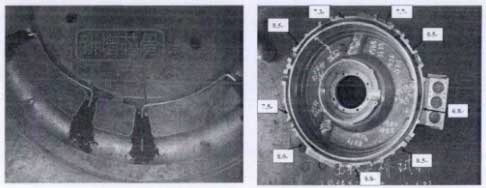