With the development of industry, higher requirements are put forward for the performance and service life of structural parts made of 5083 aluminum alloy plate. When the end customers process and anodize the parts after accepting the products, they find that there is a serious oxidation color difference in the parts, which leads to doubts about the quality of the parts and the existence of organizational heterogeneity.
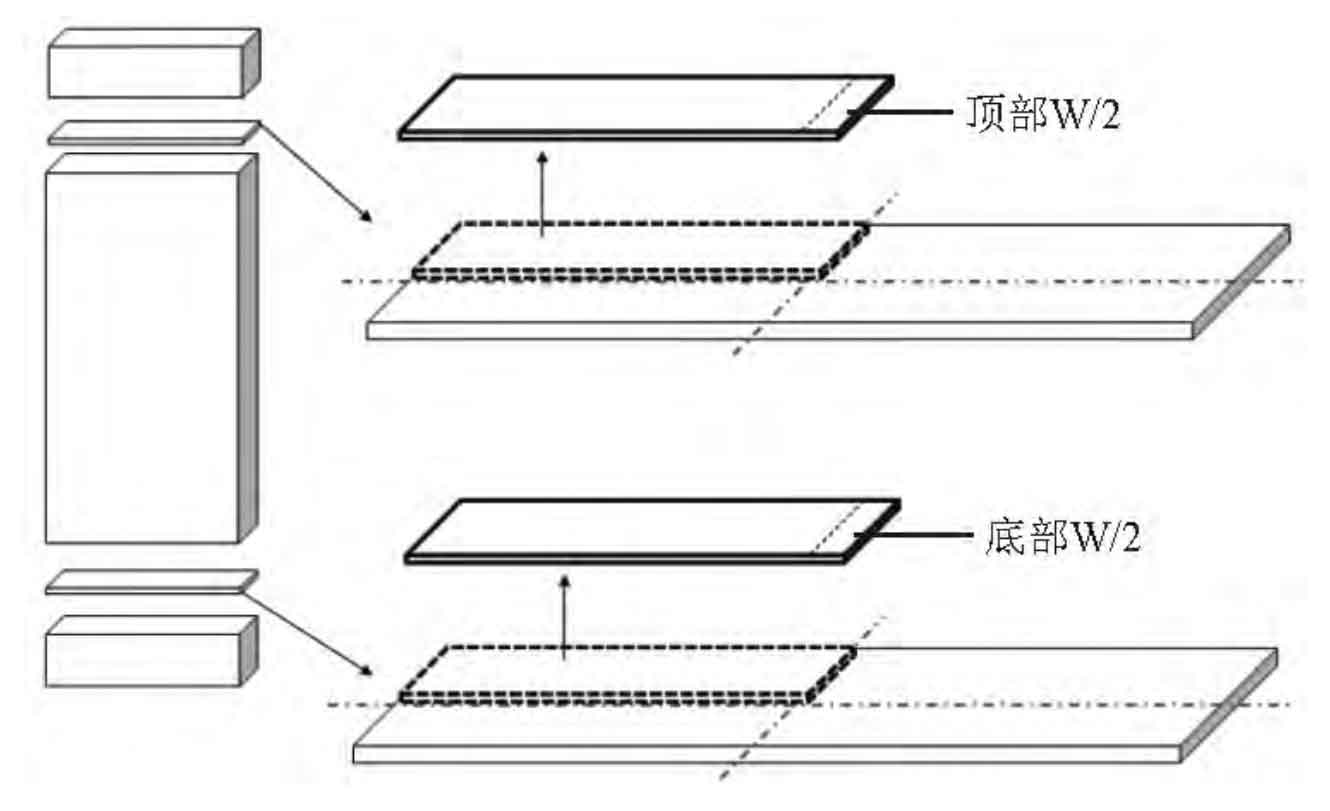
Through the preliminary analysis of the color difference of anodic oxidation, it is considered that the main factors causing the color difference are:
① Porosity, oxidation color difference caused by discontinuous defects such as hydrogen porosity and shrinkage porosity in local position of ingot caused by casting;
② Grain size, oxidation color difference caused by abnormal grains in specific parts during casting;
③ The size of primary phase, the oxidation color difference caused by the oversized second phase formed in the non-equilibrium solidification process of ingot;
④ Component segregation, oxidation color difference caused by component segregation caused by temperature supercooling and component supercooling in the casting process;
⑤ The insoluble phase of the master alloy and the oxidation color difference caused by the incomplete melting of the Al Mn, Al Cr and other master alloys added to the smelting alloy;
⑥ Oxidation slag inclusion refers to the oxidation slag inclusion caused by the oxide film on the melt surface introduced due to improper operation during casting.
Analyze the possible causes in order to provide reference for solving the problems. Through SEM observation and EDS analysis of the formation of oxidation color difference, it is considered that the unreasonable setting of Cr is the main cause of color difference. In view of the problem, the solution measures are given to overcome the color difference problem.