With the development of semi-solid theory and the promotion of semi-solid forming technology, more and more kinds of semi-solid die-casting products have been developed. At present, semi-solid die-casting products can be defined into three categories
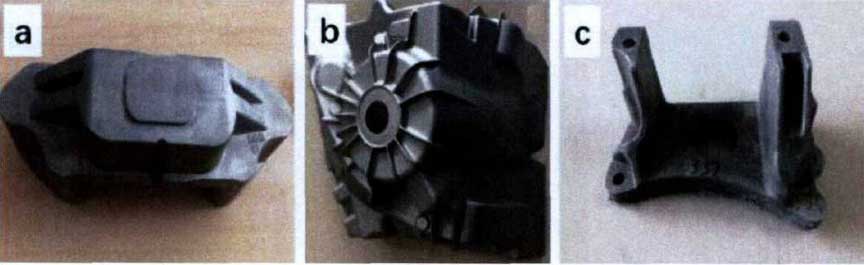
(1) The thickness of thick wall products is more than 10 mm. For example, calipers, as shown in Fig. 1 (a), have a maximum thickness of 40mm;
(2) The thickness of thin wall products is less than 5mm. For example, the damping tower is shown in Fig. 1 (b), and the thinnest part is about 4mm;
(3) The thickness of the middle wall products is 5mm-10mm, such as the left middle bracket, as shown in Figure 1 (c);
In different types of products, the typical defects have certain regularity, and the types and causes of defects are not the same. On the basis of the existing production experiments, through a large number of observation experiments, it is found that:
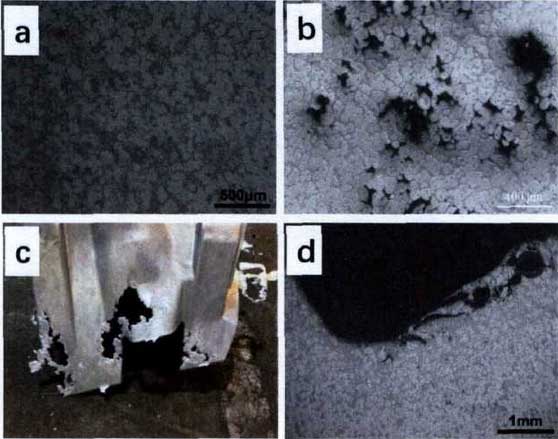
(1) In thick wall products, due to the thickness of some parts, it is easy to produce incomplete feeding in the filling process, resulting in shrinkage and porosity defects. As shown in Fig. 2 (b), the solid-liquid segregation defects are easy to occur in some characteristic parts of this type of products, as shown in Fig. 2 (a);
(2) In thin-walled parts, such as shock absorber, due to the large and thin-walled products, in order to complete the mold filling in the pouring process, the speed of the punch is usually accelerated during the casting process. In this way, although the defects of poor filling can be avoided, the stability of slurry flow front will be reduced, resulting in turbulence, and other defects, such as flow instability, will be produced, as shown in Fig. 2 (c);
(3) In the middle wall products, the thickness is between the thin wall and the thick wall, and the filling process can achieve the complete filling effect by keeping the middle and low speed. Due to its complex structure, it is easy to produce air entrapment defects in some parts such as right angle bends due to the change of card flow direction, as shown in Fig. 2 (d).
Two kinds of typical defects, shrinkage cavity, shrinkage porosity and solid-liquid segregation in thick wall products were studied.