This article focuses on the casting process design and development of a nodular cast iron motor shell. It details the product characteristics, the determination of the casting process, including (molding method), pouring system design, and the application of risers and chills. Through simulation analysis and trial production, the problems of shrinkage defects are solved, and finally, a qualified casting process is obtained. The research provides valuable experience and reference for the casting production of similar motor shells.
1. Introduction
With the development of urban rail transit, the demand for high-quality motor shells is increasing. The motor shell, as an important part of the traction system, requires high casting quality to ensure its performance and reliability. In this study, the casting process of a QT500 – 7 nodular cast iron motor shell is designed and optimized to meet the technical requirements.
2. Product Description and Technical Requirements
The motor shell has a thin-walled barrel structure with a contour size of 760 mm×500 mm×580 mm and a mass of about 160 kg. The main wall thickness is 10 mm, and the maximum wall thickness is 90 mm. It is produced by the resin sand hand molding process. X-ray flaw detection is required for the casting, with the acceptance standard of level 2 in key areas and level 3 in non-key areas. There are several isolated hot spots in the product, mainly distributed at the contact points between the inner ring ribs and the barrel wall, the upper and lower mounting brackets and the barrel wall, the safety bracket and the barrel wall, and the junction box and the barrel wall.
3. Casting Process Design
3.1 Molding Method Determination
There are two ways to place the pouring position: vertical placement (the axis of the barrel is perpendicular to the ground) and horizontal placement (the axis of the barrel is parallel to the ground). Vertical placement requires more sand cores around the barrel wall, and the bottom gating system is adopted, which makes the iron liquid filling stable, but it is difficult to solve the hot spots at the mounting brackets. Horizontal placement uses the HALF parting along the axis of the barrel, with relatively fewer sand cores, and it is easy to solve the hot spots at the mounting brackets, but difficult to solve those at the inner ring ribs. Considering the product’s use requirements, the horizontal HALF parting method is finally adopted.
3.2 Pouring System Design
After determining the parting method, there are two schemes for the iron liquid inlet: setting an annular horizontal runner at both ends of the lower barrel and using a flat runner to introduce the iron liquid; setting a horizontal runner along the parting surface from the barrel wall and using a flat runner to introduce the iron liquid. The first scheme has a stable filling process but a low casting process yield; the second scheme is prone to turbulence during filling but has a high process yield. After comprehensive consideration, the second scheme is adopted. The existing sand box size is: upper mold 1000 mm×980 mm×480 mm, lower mold 1000 mm×980 mm×340 mm. One casting per mold, and the pouring system is designed with 2 ingates to introduce the iron liquid into the cavity. After determining the process scheme, the specific process parameters are calculated as follows:
Parameter | Formula | Value |
---|---|---|
Pouring time (t) | 25 s (G≈180 kg, K = 1.85) | |
Liquid level rising speed (V) | 1.92 cm/s (c = 48 cm) | |
Restrictor cross-sectional area (阻) | 12 cm² (μ = 0.48, H = 35 cm) | |
Cross-sectional areas of each element of the pouring system | 直横内 | Straight runner: 14 cm² (40mm straight runner); Horizontal runner: 18 cm²; Ingate: 6 cm² |
3.3 Application of Risers and Chills
Without the use of chills and risers, the casting solidification process is preliminarily simulated by MAGMA software to predict the hot spot positions and corresponding moduli. The simulation results show that there are several large hot spots in the casting, and shrinkage defects are predicted. According to the simulation results and product technical requirements, chills and exothermic and insulating risers are placed at the corresponding hot spots. The exothermic and insulating risers are selected according to the specifications and the hot spot moduli at the placement positions. It should be noted that the hot spot modulus at the placement position will increase after the riser is placed. Generally, the riser is selected by enlarging the modulus of the hot spot part of the casting by 1.2 – 1.3 times.
4. Trial Production and Results
Before trial production, the solidification process of the preliminarily determined casting process scheme is simulated. The simulation shows that the selection and placement of the risers form a temperature gradient field from low to high, playing a role in local sequential solidification, and the last solidification part of the casting is in the top riser, indicating a small possibility of shrinkage defects in the casting. However, after the first trial production, the casting is detected by X-ray, and shrinkage defects are found in the contact area between the junction box and the barrel wall, exceeding the level 3 standard of the non-key area specified in the technical requirements and not meeting the customer’s acceptance requirements. The reason for the defect is that there is an isolated liquid phase area in this region, which cannot be fully fed by the iron liquid, resulting in shrinkage defects. After analyzing the cause of the defect, two chills are added at the contact position between the junction box and the barrel wall to accelerate the solidification speed of this region, reduce the isolated liquid phase area, and reduce the area of shrinkage defects. After the optimization, the casting passes the X-ray, mechanical property and other tests, meeting the customer’s acceptance standards. The chemical composition and mechanical properties of the casting are shown in the following tables:
Element | C | Si | Mn | P |
---|---|---|---|---|
Measured value | 3.64 | 2.83 | 0.38 | 0.029 |
Element | S | Cu | Mg | |
Measured value | 0.01 | 0.40 | 0.045 |
Mechanical property | Tensile strength (MPa) | Yield strength (MPa) | Elongation (%) | Hardness (HBW) |
---|---|---|---|---|
Technical requirements | ≥500 | ≥320 | ≥7 | 170 – 230 |
Measured value | 570 | 423 | 15.5 | 200 |
5. Conclusion
The application of simulation software in the casting process design simplifies the design process, especially in the calculation of moduli. In determining casting defects such as shrinkage, it is necessary to combine the isolated liquid phase area during the solidification of the metal liquid. The research on the casting process of the nodular cast iron motor shell provides a reference for the production of similar products, and continuous improvement and optimization of the process can improve the quality and production efficiency of the casting.
In the actual production process, it is also necessary to pay attention to the control of raw materials, the operation 规范 of the production process, and the quality inspection of the casting to ensure the stability and reliability of the product quality. Future research can focus on further optimizing the casting process parameters and exploring new materials and technologies to meet the higher requirements of the development of the motor shell manufacturing industry.
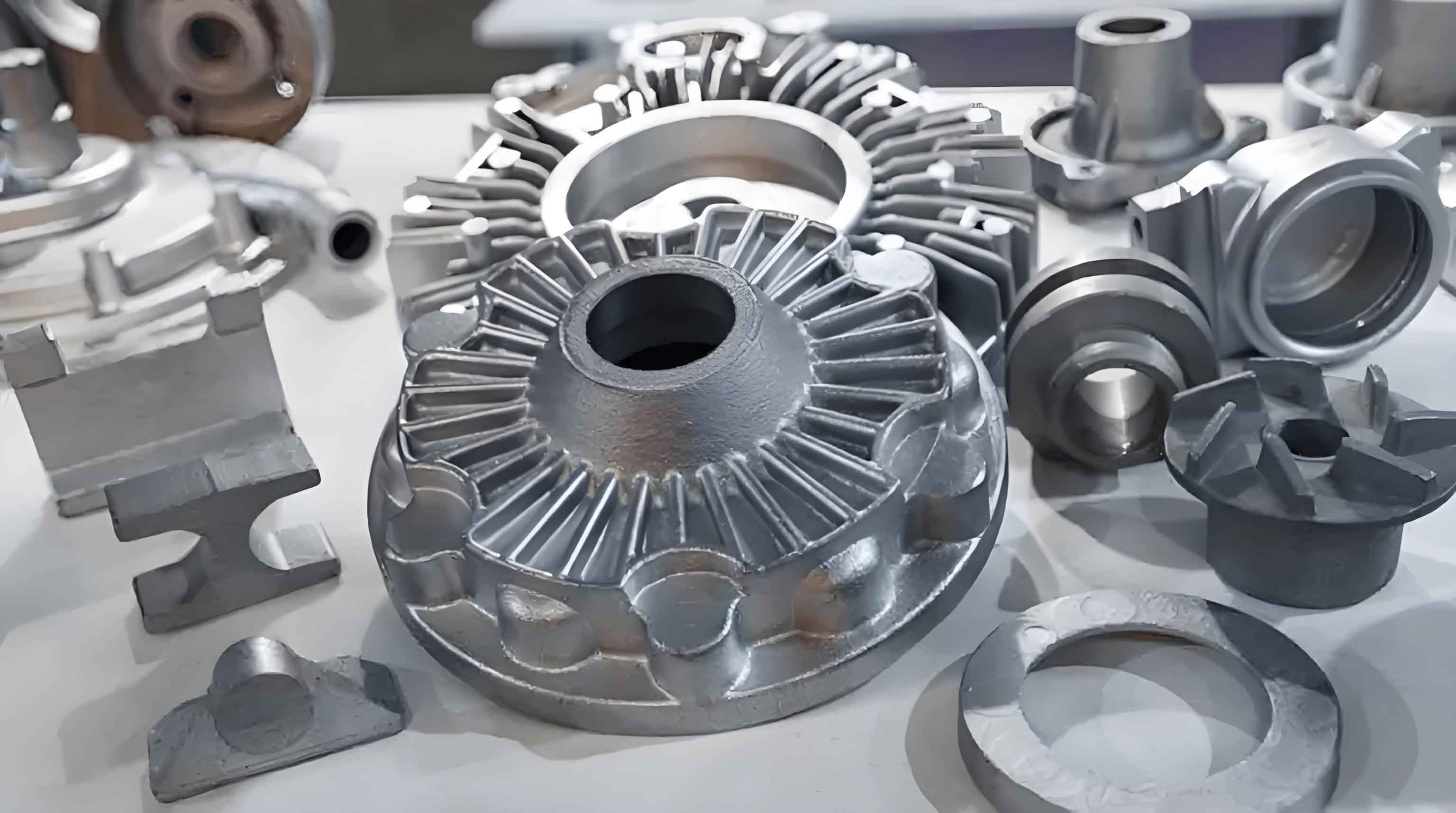