Cement rotary kiln is the main equipment of cement clinker dry process and wet process production line. Driven by the external power, the rotary kiln body makes the rotary movement driven by the gear. Generally, the size of the gear on the larger rotary kiln is also very large. For this kind of large-scale gear, the casting method is usually used to produce the gear blank first, and then the blank is processed. The traditional casting process is based on trial and error, which is not only difficult to reflect the scientificity of the casting process, but also can not adapt to the modern production because of the long test cycle and high cost of trial and error method. Computer simulation technology provides a more effective way to design the gating system, so that the casting process can be simulated on the computer, which not only reduces the cost, but also shortens the test cycle.
At present, all the simulation software in the market is based on the verification of the existing process, so it is difficult to use computer software alone to design the casting process system. The simulation software of viewcast, which i s developed by WTCM foundry center in Belgium, is a software integrating simulation and design. The software can simulate the fluid flow and heat transfer in the process of mold filling and solidification, and design the pouring and feeding system through the simulation results. Taking the cast steel gear as an example, this paper describes the general process of casting process design by using view CAS software.
As shown in the figure is a three-dimensional solid diagram of the large gear. The diameter of the casting is 5300mm. Due to the large size of the casting, the casting is cast in the form of 1 / 2 piece. It can be seen from the figure that the gear is of spoke type and the casting size is large. It can be judged that if there is no feeding measure, the intersection of the spoke and the outer ring gear of the gear will definitely produce casting defects, because these are the hot spots of the casting. In order to avoid this situation, a feeding riser with a diameter of 440mm and a height of 650mm is designed at the intersection of each spoke and outer ring gear. In order to effectively supplement, these risers are designed as insulation risers.
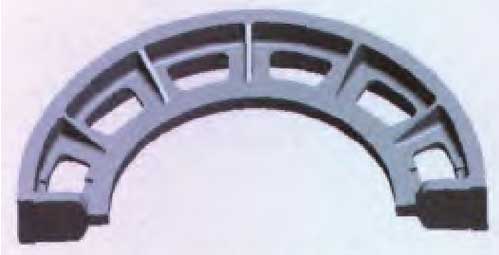
For the pouring system, in order to make the liquid metal fill into the casting as soon as possible, multiple internal sprues are selected for pouring. The distribution of internal sprues is that there is an internal sprue at each spoke to enter the casting. The pouring system and feeding system of process scheme I are shown in Figure 2. Figure 2A shows the riser system of the gear casting, figure 2B shows the grid division of the casting, the red part is the casting and riser system, and the green part is the insulation material outside the insulation riser.
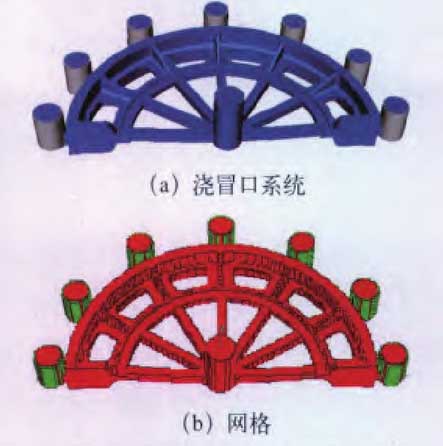