The research of gating system parameters design is to analyze the statistical law of pouring process parameters, mainly including flow coefficient μ 3 and pouring time t.
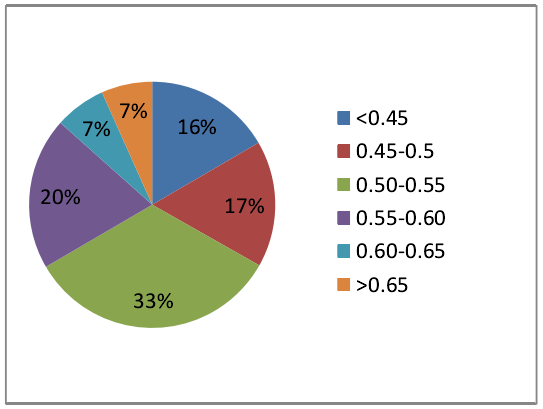
The flow coefficient μ 3 represents the flow state of molten metal in the mold cavity, which is one of the important process parameters to measure the gating system. According to the pouring time of cylinder block iron castings in production and based on the theory of large hole outflow, the statistical law of flow coefficient μ 3 of cylinder block iron castings is analyzed. The distribution of flow coefficient μ 3 is shown in Figure 1, and the statistical situation is shown in Figure 2.
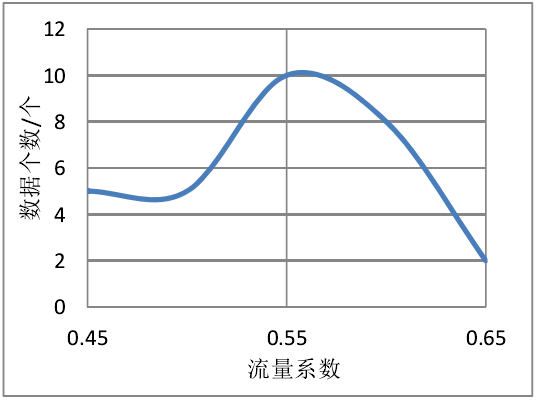
It can be seen from Figure 1 that the discharge coefficient μ 3 is mainly distributed between 0.45 and 0.60, accounting for 70%. It is recommended to use flow coefficient μ 3 = 0.50 ~ 0.60, bottom injection type μ 3 = 0.50, middle injection type μ 3 = 0.55, step type μ 3 = 0.50 ~ 0.55.
The pouring time is another important parameter to measure the gating system. The pouring time of cylinder body iron castings refers to the time from the beginning of liquid metal entering the cavity to the time when the cavity is completely filled. Pouring time is related to casting material, casting quality, sand strength and other factors. Based on the discussion of the theoretical pouring time of cast iron castings and the analysis of the empirical formula, the judgment criteria and formulas of pouring time suitable for slow casting, fast casting and medium speed casting are recommended.
The pouring information of 30 samples, including casting mass (unit: kg) and pouring time for production (unit: s), were collected, and the average value of statistical pouring time and pouring type were determined. The results of statistical distribution are shown in Figure 2.
According to the statistics, the mass of casting is 38 kg ~ 9100 kg, and the pouring is 12.00 s ~ 105.00 s. The statistical distribution curve of pouring time of cast iron castings for cylinder block is shown in Fig. 3. The thick solid line represents the statistics of casting time of cylinder block iron castings, and the fine solid line is the trend line.
It can be seen from the statistical cases that the pouring time has a positive correlation with the quality of cast iron castings, and it increases with the increase of the quality of cast iron castings, and decreases when m = 1000 kg. When m = 4 000 kg, the pouring time prolongs with the increase of casting quality, and the curve tends to be flat. At present, in the production of cast iron castings for cylinder block, slow casting method is mainly used for small cylinder block, medium speed casting method is generally used for medium-sized cylinder block iron castings, and fast casting method is usually used for large cylinder block iron castings.
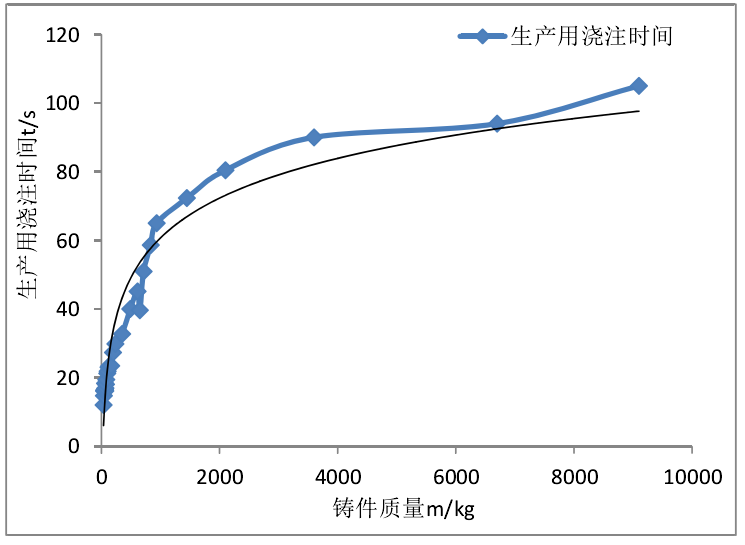
In order to avoid the gate overheating caused by too long pouring time, it is suggested to adopt the rapid casting process for cylinder body castings with more than 1000 kg. The piecewise function curve of pouring time and casting quality was fitted
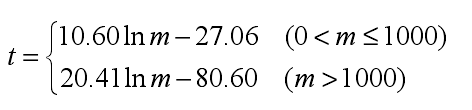
However, in practical production, the pouring time is generally based on empirical formula,
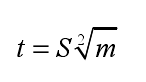
Where s is the relation coefficient
The distribution of relationship coefficient between casting quality and pouring time shows a negative correlation between the value of relation words and casting quality in any quality range, that is, the closer the quality is to the upper limit, the closer the value of relation words is to the lower limit; the closer the quality is to the lower limit, the closer the value of relation words is to the upper limit.