The selection of chemical composition should be considered from two aspects: ensuring good mechanical properties and casting properties of castings. The basic common elements in nodular cast iron include carbon, silicon, phosphorus, sulfur and manganese. Carbon and silicon are the main elements that determine the graphite morphology and mechanical properties of nodular cast iron. Carbon content affects the spheroidizing effect to a certain extent. Generally, the higher the carbon content, the more graphite precipitates and the more graphite balls. Higher carbon content can reduce the volume of shrinkage porosity and shrinkage defects and make the casting structure more compact. However, when the carbon content is too high (more than 4.3 wt.%), a better effect of preventing shrinkage and porosity can not be obtained, but serious graphite floating may occur. Moreover, because the graphite morphology of nodular cast iron is spherical, the effect of carbon content on the mechanical properties of nodular cast iron is not as significant as that of flake graphite. The increase of carbon content will lead to the decrease of hardness and the increase of elongation. As shown in Figure 1, when the carbon content is about 3%, nodular cast iron obtains the best tensile strength.
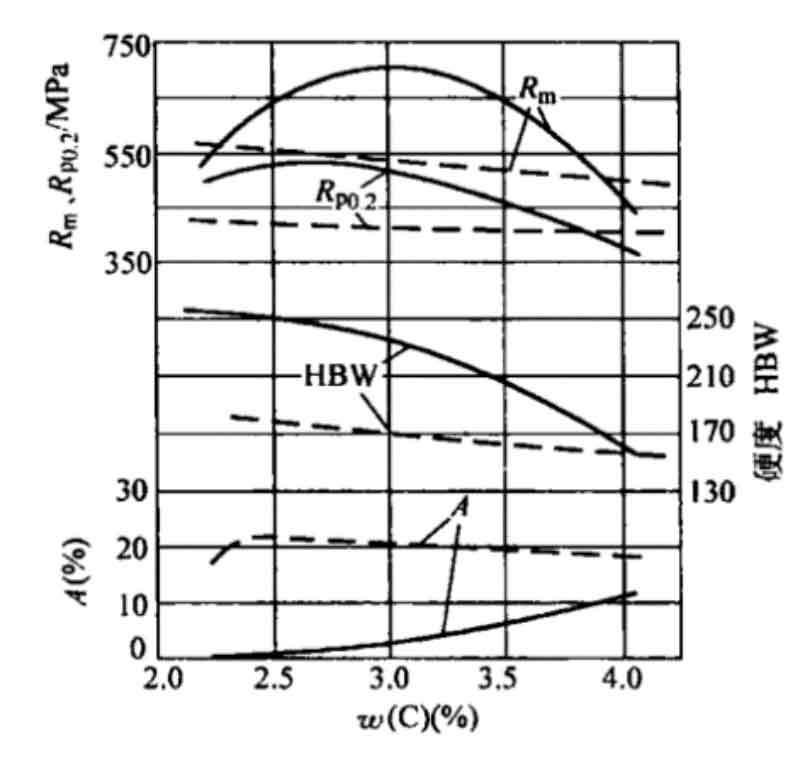
Silicon is also an element that promotes graphitization. The inoculation of silicon will change the proportion of ferrite and pearlite in nodular iron matrix. However, when the silicon content exceeds 3 wt.%, the impact toughness decreases sharply. Generally, in order to simplify the expression, the content of carbon and silicon elements is usually expressed as carbon equivalent CE in a specific proportion, that is, CE = (c + 0.3si)%. Increasing the carbon equivalent can increase the fluidity of the liquid metal, but it will also increase the tendency of shrinkage porosity. Therefore, in order to ensure the filling force and minimize the shrinkage volume, the best mass fraction of carbon equivalent is controlled in the range of 4.2 wt.% to 4.8 wt.%.
Manganese is an element forming carbide and pearlite, which can improve the strength and hardness of materials. However, when the manganese content is too high, carbide segregation is easy to appear at the grain boundary, which reduces the plastic toughness of the casting and increases the white tendency of nodular cast iron during solidification. Therefore, when producing high toughness nodular cast iron, the manganese content is generally required to be kept at a low level as far as possible, and the manganese content of Pearlite Nodular Cast iron used as cast is generally selected at 0.3wt%~ 0.5 wt.%。
Phosphorus in nodular cast iron mainly comes from metal charge. Phosphorus has no effect on spheroidization, but it is a harmful element that can be dissolved in liquid iron and reduce the eutectic carbon content of iron carbon alloy. Due to the porridge solidification characteristics of nodular cast iron, segregation is easy to occur when the phosphorus content is close to 1 wt.%. In addition, phosphorus can also aggravate the shrinkage porosity tendency of castings, making castings easy to cold crack. Figure 2 shows the curve of the mechanical properties of as Cast Ferritic Nodular Cast Iron with the phosphorus content. When the phosphorus content exceeds 0.07 wt.%, the elongation after fracture of the casting decreases significantly. Therefore, some chemical standards of nodular cast iron usually require that the phosphorus content is not greater than 0.07 wt.%. However, for castings with large section thickness, phosphorus eutectic will occur when the phosphorus content is 0.04 wt.%, which significantly reduces the plasticity and impact toughness of the material. Therefore, the phosphorus content should be controlled below 0.05 wt.% as much as possible.
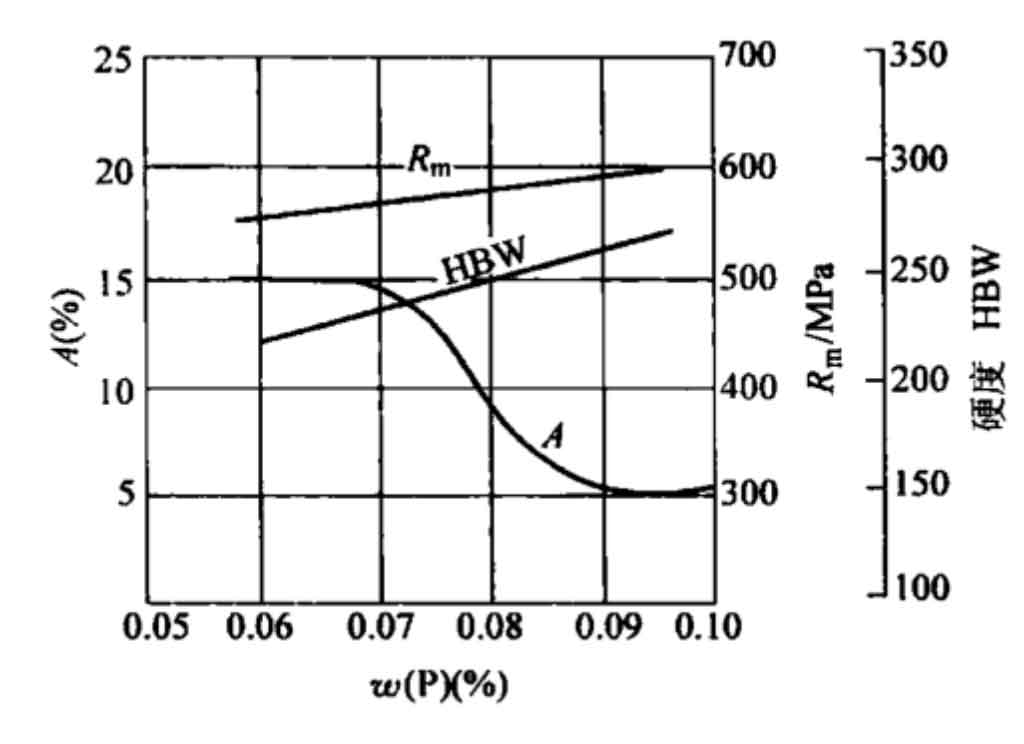
Like phosphorus, sulfur is brought into nodular iron through metal charge and fuel, which has a strong interference with graphite spheroidization. Sulfide in molten iron is the main component of molten slag. If it cannot be removed in time, spheroidization recession will occur inside the casting. Therefore, the sulfur content is generally controlled below 0.018 wt.%.
In addition to the above basic elements, the addition of copper, magnesium, chromium, nickel, molybdenum and other alloy elements to nodular cast iron is also conducive to adjusting the casting structure and improving the physical properties. Copper and nickel are stable pearlite elements, but because nickel is expensive, copper is often used to replace nickel in production. At the same time, copper is an element that promotes graphitization. Although its graphitization ability is weaker than that of carbon and silicon, the addition of copper can weaken the anti graphitization effect of some carbide forming elements. It has been confirmed that increasing the content of copper can reduce the size of eutectic, which is helpful to improve the strength of castings, but the impact toughness will be significantly reduced if the mass fraction of copper exceeds 1 wt.%.
Chromium can strengthen mechanical properties to a certain extent, but it has strong affinity with carbon. In order to avoid the formation of chromium rich carbides with strong binding ability with phosphorus eutectic and severe damage to impact properties, the chromium content is generally controlled below 0.05 wt.%. Magnesium is a spheroidizing element and a strong anti graphitization element. Too low magnesium residue will easily lead to poor spheroidization, and too high magnesium residue will lead to casting defects such as white mouth and shrinkage porosity. After years of development and application of nodular cast iron, people have found that the addition of some trace elements is also conducive to the formation of castings with denser microstructure and better properties. Tin is an element that promotes the growth of pearlite and has strong ability to stabilize pearlite. Moreover, the compound addition of tin and copper can significantly promote the role of the two elements.
Increasing the proportion of pearlite in tin matrix can not only improve the tensile strength of castings, but also improve the impact toughness of materials. However, it should be noted that if the tin content exceeds 0.07 wt.%, it will seriously interfere with the spheroidization of graphite, deteriorate the shape of graphite and affect the properties of materials.
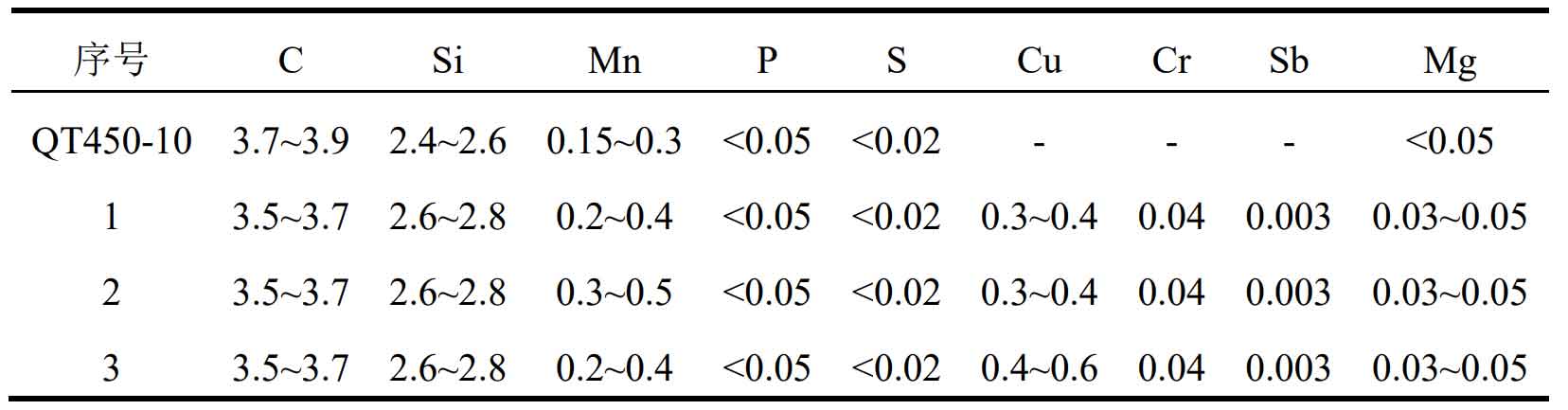
Based on the above analysis, according to the chemical composition range of QT450-10 nodular cast iron and the specific structure and performance requirements of high strength and toughness as cast nodular cast iron automobile hub support, the chemical composition range of three groups is preliminarily designed as shown in the table.