The design of the gating system directly affects the quality of investment castings. The gating system is generally composed of a gate cup, a sprue, a transverse sprue, and an inner sprue. Due to the unique structure of the ball valve, changing the structure and size of the pouring system can effectively reduce the overall shrinkage defects of investment castings.
The pouring position of investment castings refers to the position of investment castings in the mold during pouring. The determination of the pouring position is an important part of casting process design, which is related to whether the quality of investment castings can be guaranteed, as well as the dimensional accuracy and molding process of investment castings. Based on the structural characteristics of the ball valve, a gate is installed on the same side of any two end faces of the investment casting, and there is a high possibility of shrinkage or porosity on the other end face. Therefore, an inner gate is opened on each end face of the investment casting to avoid the formation of large shrinkage defects at the corners of the investment casting. At the same time, this design also ensures that the important processing surface of investment castings should face downwards or be in a side elevation design requirement.
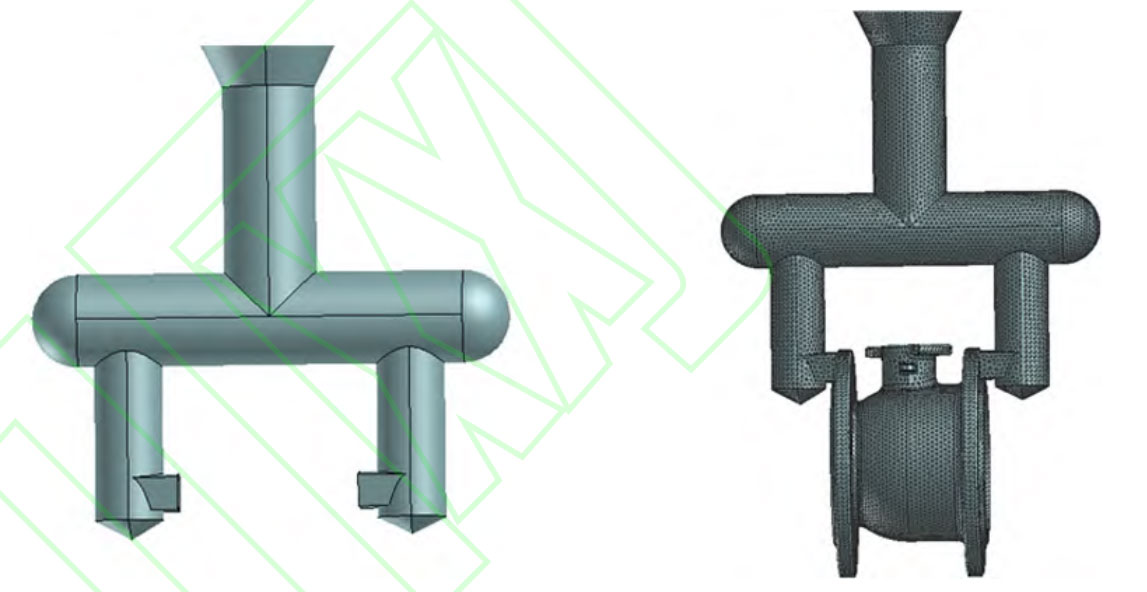
According to the relative position of the inner gate in the investment casting, the pouring form of the 304 stainless steel ball valve this time is the top pouring type. The designed sprue has a length of 100 mm and a diameter of 24 mm, with a cross-sectional area of 1.4 times the total cross-sectional area of the inner gate. It is easy to use gravity for filling and reduces shrinkage. A buffer is installed at a distance of 30 mm from the bottom of the transverse gate to the inner gate. The cross-sectional shape of both the vertical and horizontal sprues is circular. The cross-sectional shapes of the internal pouring channel generally include rectangular, circular, circular, fan-shaped, gap type, etc. Considering the structure of investment casting and the fact that there are eight threaded holes on the flange surface of the ball valve, it is more reasonable to use a sector shaped inner runner cross-section. According to the design principles, the length of the inner gate should be as short as possible for easy cutting, usually 10-15mm. To ensure convenient cutting, the length of the sector shaped inner gate is designed to be 12mm. One inner gate is arranged on each end face on both sides, so the number of inner gates is 2. The structure of the pouring system is shown in the figure.