For steel castings, in order to ensure that the riser can effectively feed the steel castings, it is necessary to ensure that the solidification time of the riser is longer than the solidification time of the steel castings, and the amount of feed liquid provided by the riser should not be less than the sum of the liquid shrinkage, solidification shrinkage, and cavity expansion of the steel castings in the area to be fed. Therefore, when designing steel castings, the company requires that the amount of feeding liquid in the riser be greater than or equal to 1.2M for castings, which is greater than 1/3 of the weight of the part of the steel castings being fed and the weight of the concealed riser. In addition, it is necessary to ensure that sufficient liquid metal can be provided while ensuring the smooth feeding channel between the riser and the steel castings during the entire solidification process.
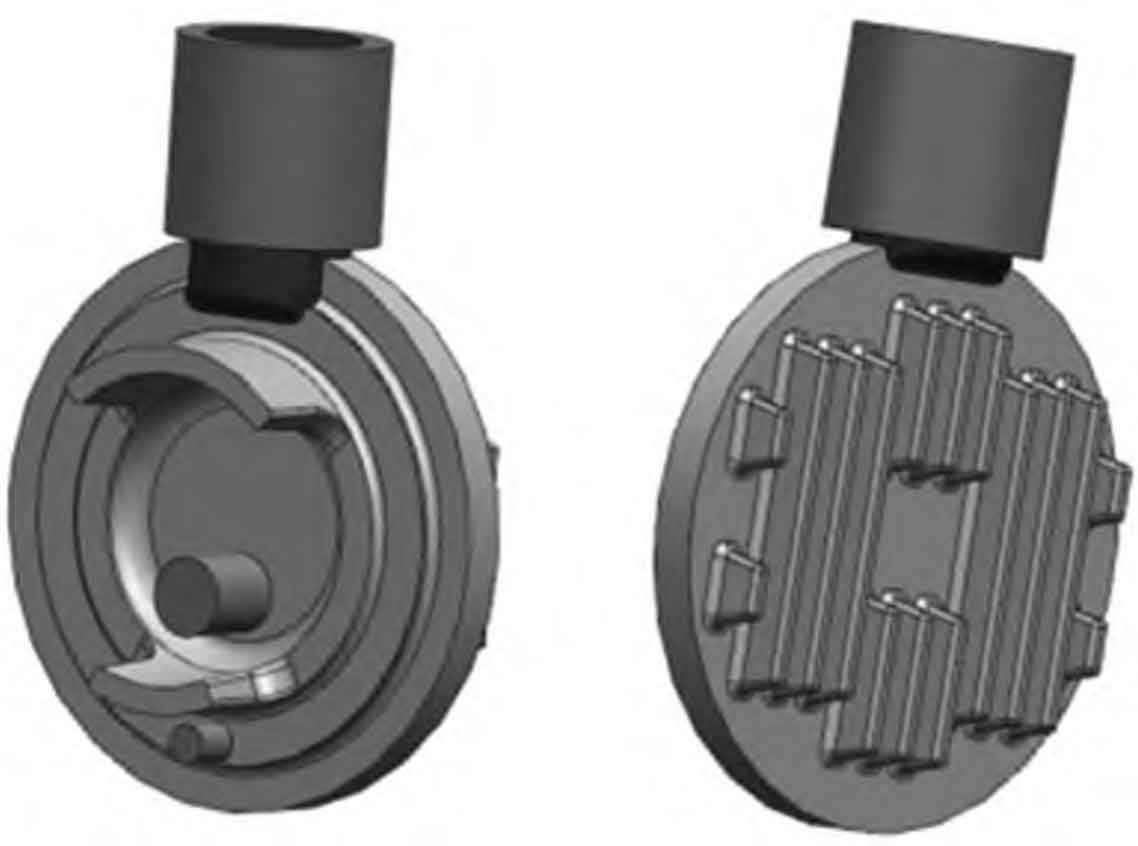
By analyzing the distribution of hot spots in the structure, pouring position, and thick position of steel castings and combining with CAE simulation software, it is determined to use one top riser, and then determine the size of the riser through the modulus of the steel castings. At the same time, through the combined use of cold iron and subsidies, it is ensured that the steel castings are free of shrinkage cavities and porosity defects, ensuring internal quality. As shown in the figure, it is a riser chill design for the pump gland product.