When the high temperature molten iron is poured into the furan resin self hardening sand mold, the furan resin, curing agent and other raw and auxiliary materials in the molding sand will decompose at high temperature to produce a large amount of gas, and at the same time, the gas wrapped in and involved in the molten iron will overflow. The volume of gas increases with the increase of temperature, resulting in the increase of air pressure at the metal mold interface. When the local gas pressure at the interface When p gas is greater than the counter pressure ∑ P (∑ P = P static + P resistance + P cavity) on the surface of molten metal, the gas in the mold can invade into the molten metal and become bubbles at the initial stage of solidification. If the temperature and viscosity of molten metal are favorable for the bubbles to float up and overflow, there will be no Blowholes in the castings, otherwise, the blowholes will be formed at the invasion site.
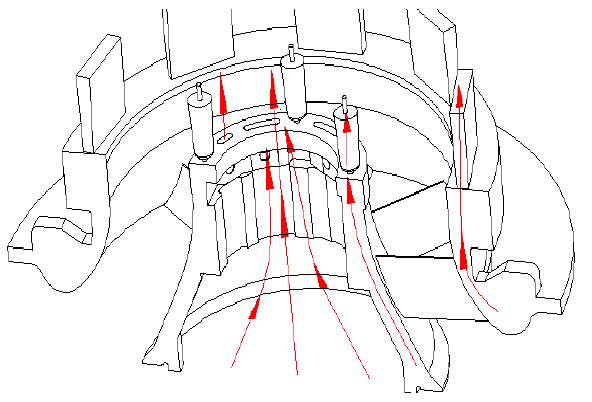
In addition to reducing and controlling the real gas production of gas sources such as mold and reasonable gating system, the air permeability of sand mold wall or sand core should be increased, such as pricking air holes, setting vent and exhaust branch in sand core. The inlet cylinder is provided with an exhaust channel in the sand core, and the gas in the exhaust channel of the sand core is led to the preset position of the upper box for exhaust through nylon exhaust rope. At the same time, the riser is set at the necessary position to ensure the smooth exhaust passage. The channel and direction of sand core exhaust in the compressor inlet cylinder are shown in the figure.