The function of sand core is to form the inner cavity, hole of casting and the part that can’t produce sand in the outer mold of casting. Sand cores are sometimes used for parts of the mold that require special properties. The shape of clamp sand core is as shown in the figure
1. Design of core head
The sand core is mainly fixed on the sand mold by the core head. For the vertical core head, in order to ensure that its axis is vertical and firmly fixed on the sand mold, it must have enough core size.
Calculate the height of sand core according to the actual design measurement: l = 140mm
Core diameter: D = 65mm (considering MRA)
According to table 6-56 of foundry engineer’s manual, the initial selection of core length is: H = 25-30mm, H = 30mm
In mass production, the same cross-section columnar sand core is adopted, and the upper and lower core heads can be of the same height, so the upper and lower core heads are h = 30mm.
According to table 6-57 in the foundry engineer’s manual, the core head inclination is determined as follows: upper core head a = 10, a = 6mm, lower core head a = 5, a = 3M
The gap between the vertical core head and the core seat is s. according to table 6-58 of foundry engineer’s manual, s = 0.5mm
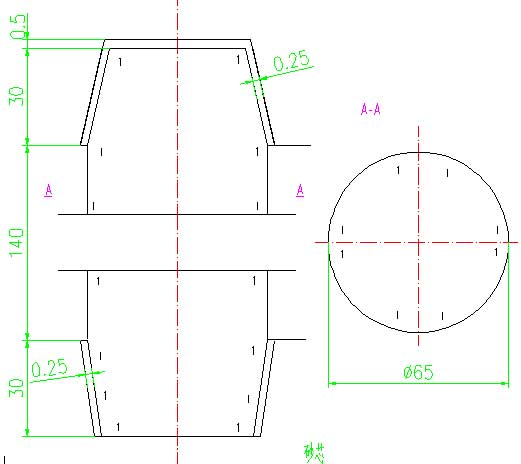
2. Core structure of pressure ring, anti pressure ring and sand collecting groove
In the mass production of wet mold, in order to speed up the core lowering, core combining and ensure the quality of casting, the pressing ring, anti pressing ring and sand collecting groove are often made on the pattern of core head.
According to table 1-43 of foundry technology manual, the dimensions of compression ring, anti compression ring and sand collecting groove are as follows:
e=2mm f=3mm r=2mm
3. Core design
In order to ensure that the sand core does not crack, deform or break by the impact of liquid metal in the process of core making, handling, core matching and pouring, the core bone is usually embedded in the sand core to improve its rigidity and strength.
Because the size of the sand core is small and resin sand is used, the strength of the sand core is good and no core bone is placed in the sand core.
4. Exhaust of sand core
During the casting process of sand core, the binder and the organic matter in the sand core need to burn (oxidation reaction) to release gas, and the residual moisture in the sand core needs to be evaporated by heating to release gas. If the gas can not be discharged out of the mold, it will cause porosity in the casting. Ventilation needle, ventilation template, wax line, nylon pipe, manual excavation and other methods can be used for exhaust.
5. Negative number of cores
In the process of spring sand, the large clay sand core expands to all sides, and the size around the sand core increases due to coating and deformation during drying. In order to ensure the accuracy of casting size, the length and width of the core box are subtracted by a certain amount, which is called the negative number of sand core.
Because the negative number of sand core is only used for large clay sand core, the sand core in this design is small sand core without negative number of sand core.