The heat transfer coefficient of squeeze casting die interface is calculated by inverse algorithm. In order to obtain accurate calculation results, the measurement of the internal temperature of the die must be accurate. Therefore, a temperature measurement unit is specially designed to meet the requirements of accurate temperature measurement. As shown in Fig. 1, it is the schematic diagram of the temperature measurement unit. The temperature measurement unit is a stepped cylindrical bar made of H13 steel, which is the same as the die. Six grooves with a width of 1 mm and a depth of 1 mm are machined by EDM along the circumferential direction. These grooves can be used to place thermocouples. Each groove is spaced 60 ° along the circumferential direction. The processed stepped cylindrical bar is shown in Fig. 2 (a). The six slots are symmetrical and divided into three groups. The distances between the front end of each group of slots and the front end of the temperature measurement unit are 1 mm, 3 mm and 6 mm respectively. According to the distance, the three groups are named group A, group B and group C respectively. Thermocouples are arranged in each group of slots, so that the two thermocouples can be standby for each other, and if the temperature difference is too large, it means that there is a problem in the temperature measurement of the temperature measurement unit, and it can be replaced in time. The symmetrically arranged thermocouples are named as No.1 thermocouple and No.2 thermocouple, as shown in Fig.2 (a) and (b).
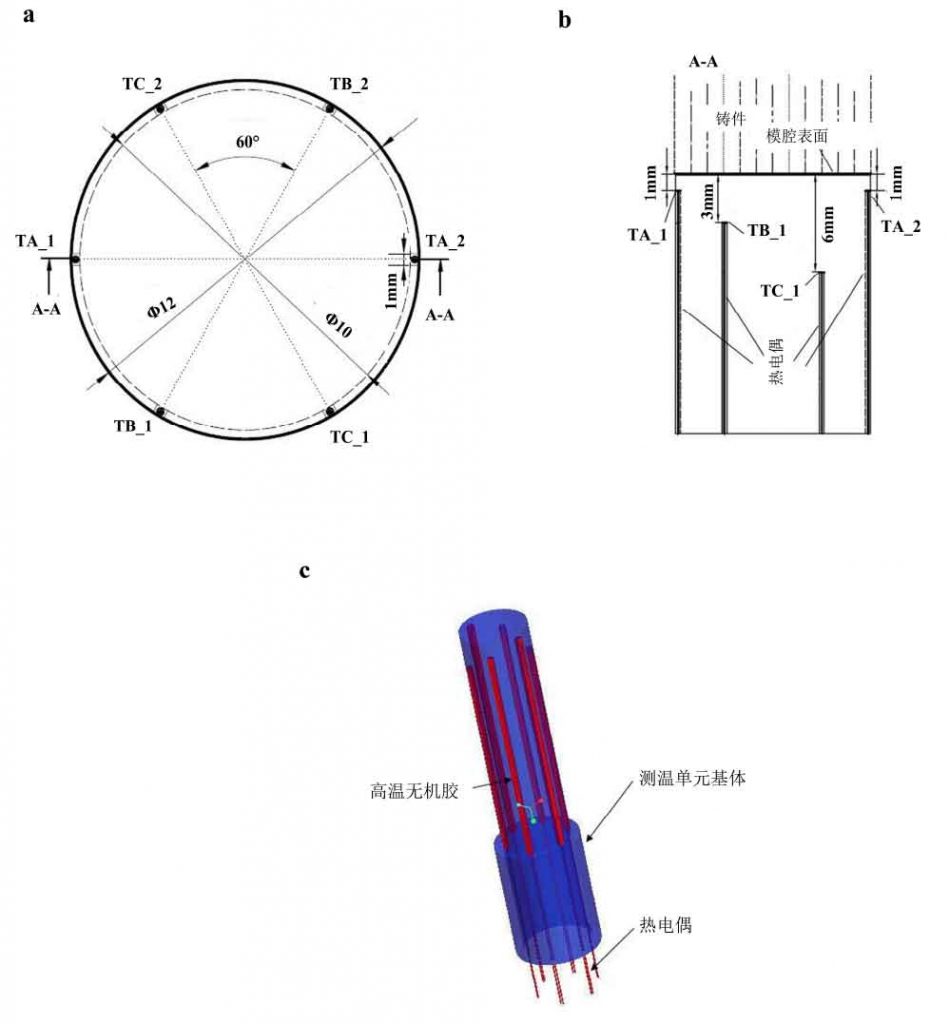
(b) Arrangement of thermocouple in temperature measurement unit A-A section
(c) Structure of temperature measurement unit
The design of the temperature measurement unit reduces the temperature field changes caused by drilling in the mold to a certain extent. Because the temperature measurement unit can be prefabricated in advance, multiple temperature measurement units can be prepared for standby, which solves the problem that the thermocouple installed by drilling holes in the mold is not easy to replace after being damaged. And the slot on the temperature measurement unit is open, which makes the placement of thermocouple much easier. The distance between the end face of the groove and the end face of the temperature measuring unit can be achieved by accurate machining, which makes the placement of the thermocouple very accurate.
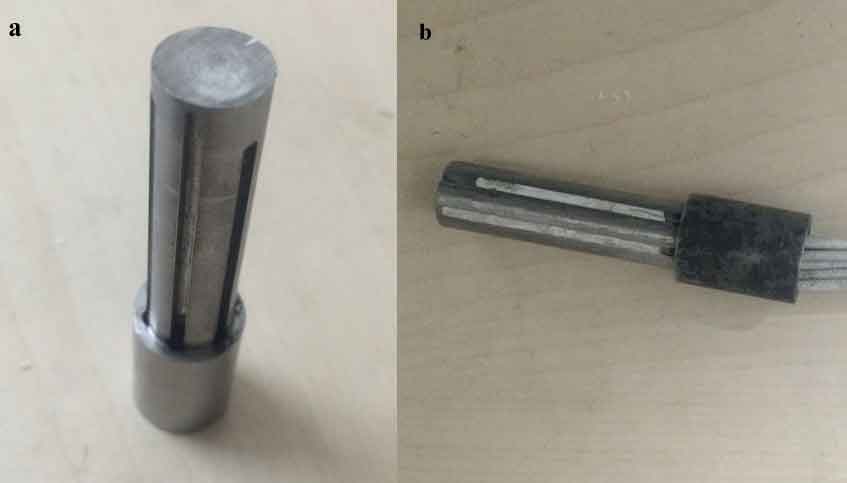
(b) The temperature measurement unit is made;
In order to measure the temperature accurately, the thermocouple needs to be in full contact with the measured medium. In order to ensure that the thermocouple temperature measuring end is in close contact with the end face of the temperature measuring unit slot, the energy storage welder is used to weld the thermocouple to the front end face of the slot. After welding, the temperature measurement unit needs to be installed on the mold. During the installation, the thermocouple solder joint is easy to fall off. Therefore, in order to prevent the thermocouple from falling off, high temperature inorganic adhesive is used to coat each tank. The completed temperature measurement unit is shown in Figure 2 (b).
In the process of squeeze casting, the temperature changes violently at the moment of pouring and pressure application, so the thermocouple must be able to make a quick response, so there are high requirements for the response time and diameter of the thermocouple. The thermocouple used in this paper is purchased from Omega Engineering Inc. the diameter of the thermocouple wire is 0.25 mm. The response time of the thermocouple is 10ms, which can meet the needs of this experiment.
Because the high temperature inorganic adhesive is easy to adhere to the surface of the temperature measurement unit, it is necessary to polish the temperature measurement unit. In order to ensure that there is no aluminum leakage during the experiment, the temperature measurement unit needs to be 0.01mm or 0.02mm larger than the design size of + 0.018012mm. The temperature measurement unit is made of H13 steel, which is the same material as the die, so that the temperature field inside the die will not be distorted due to the material properties.