The pouring position of the casting is the position of the casting in the mold when pouring. The pouring position not only has an important influence on the quality of castings, but also has a close relationship with the structure of process equipment (such as pattern and core box), the process of core lowering, mold closing and even cleaning, and also affects the machining. The selection of pouring position shall be determined according to the size, structural characteristics, alloy performance, production batch, on-site process conditions and synthesis of castings [3]. In order to ensure the quality of castings, the molding process and pouring process should be simplified as much as possible. At the same time, we should pay attention to the following principles:
1.The important processing surface of pouring shall be downward or in the form of side elevation
In general, it is more likely to form defects such as porosity and inclusions on the top of the casting, while the downward bottom and side facades of the casting are relatively smooth, so the possibility of defects is less.
2.Try to make the large plane of the casting face down
It can not only avoid porosity and slag inclusion, but also prevent sand inclusion defects in large plane.
3.The casting shall be fully filled
For castings with thin-walled parts, the thin-walled parts shall be placed in the lower half or below the inner sprue to avoid defects such as missing pouring and cold insulation. When the area of the thin wall part of the casting is large, inclined casting can be used to ensure that the casting can be filled.
4.It should be conducive to sequential solidification
The thick part or local thick part of the casting shall be placed on the top or side of the mold to facilitate the placement of risers and realize the sequential solidification from bottom to top.
5.Try to reduce the number of sand cores and make them stable
Avoid the use of hanging sand, hanging core or cantilever sand core to facilitate core lowering, inspection, fixation and exhaust.
In this design, the support platform plays the role of supporting and bearing load in the work. The lower flange has large stress and should be wide. According to the important processing surface or large plane, it should face down or form side elevation. In order to avoid defects such as pouring failure and cold insulation, horizontal pouring of the support platform can make the processing surface at both ends in the side elevation, so as to ensure the quality and accuracy of the casting, and is conducive to core laying, inspection, fixation and air exhaust. The schematic diagram is as shown in the figure.
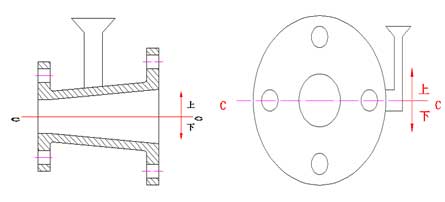