Generally speaking, the higher the pouring temperature is, the better the fluidity of alloy liquid is, and the more favorable to mold filling. Therefore, properly increasing the pouring temperature is easier to realize complete mold filling. However, if the pouring temperature is too high, it is easy to cause the alloy liquid to oxidize and splash. At the same time, it also increases the mold temperature, increases the mold cooling and film removal time, which will have a certain impact on the production efficiency of the product.
Considering that the reasonable pouring temperature range of the material used in the axle housing is between 1 540 ~ 1 590 ℃, and the temperature range of the solid-liquid two-phase zone is about 1440 ~ 1510 ℃, the difference of pouring temperature has a certain influence on the distribution of thermal stress of the casting, the higher the temperature makes the stress concentration of the axle housing more obvious, and the lower temperature is prone to the phenomenon of insufficient pouring. Considering that the material used in the axle housing is zg40mn, and the other parameters are the same, the local temperature change of the casting is studied when the pouring temperature is 1 540 ℃ (green line), 1560 ℃ (red line) and 1580 ℃ (blue line).
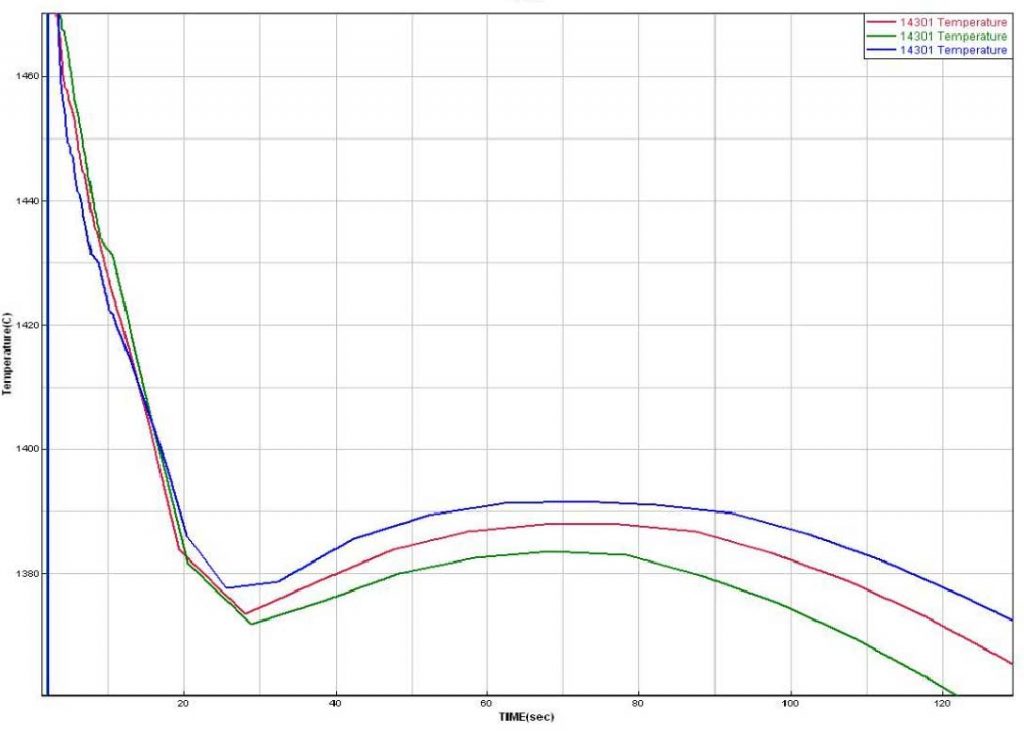
It can be seen from the figure that in the 20-30 seconds filling simulation stage, the temperature of the 1580 ℃ blue curve decreases rapidly, which is conducive to rapid filling, and the cooling rate is relatively fast in the temperature range. In the later stage of solidification, the solidification rate of 1580 ℃ blue curve is slower than that of 1540 ℃ green curve and 1560 ℃ red curve, and the relatively slow solidification speed can avoid the generation of hot cracks and reduce the tendency of stress concentration, which is conducive to the solidification of castings. Therefore, the pouring temperature is set at 1580 ℃.