In order to study the carburization defects of steel casting for bridge support, four sampling locations are selected, namely, near the inner gate, the center of the casting, the rib plate part and the top of the casting (the part connected with the riser), which are numbered as a, B, C and D respectively. The sampling position is shown in the figure.
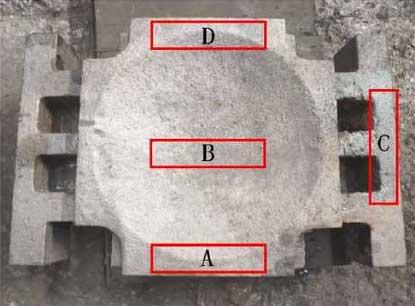
The direct attack spectrometer requires that the surface of the sample to be tested should be smooth and the roughness is between ra3.2 μ m and ra6.3 μ M. if the surface is too smooth, it is not easy to be excited. If the surface is too rough, it is easy to cause air leakage during excitation, which will affect the test results.
The foam pattern of this experiment is mainly formed by cutting and blanking. The surface of the steel castings is oxidized and the roughness is between Ra25 and m~Ra50 m, which can not meet the requirements of directly detecting chemical components. Therefore, in the detection of surface carburization, the surface of the sample blank is polished to reveal metallic luster, about 0.5mm ~ 1mm below the skin.