Abstract
The shell casting process faces challenges due to the complex internal cavity and thin-walled structure of the shells. The traditional casting methods are time-consuming, inefficient, and costly. This study proposes the integration of sand mould 3D printing technology with low-pressure casting for the rapid and precise manufacturing of complex shell castings. The pouring system is designed conformally to achieve integrated structure forming of the cavity and blades. Numerical simulation is employed to optimize the casting process, and the results demonstrate that the proposed method significantly reduces production time and cost while ensuring high precision.
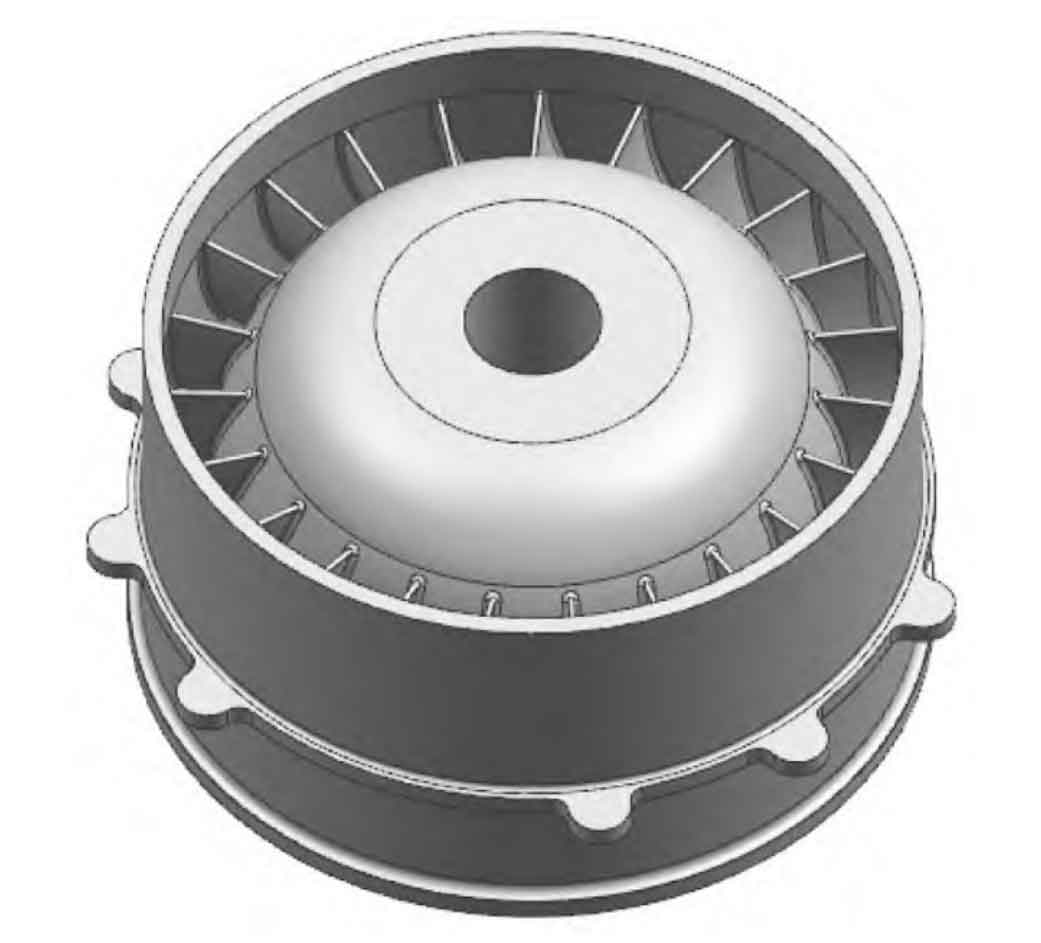
1. Introduction
Shell castings are widely used in various industries, including aerospace, automotive, and marine engineering, due to their structural complexity and lightweight properties. However, the traditional casting methods for shell castings have limitations, such as long lead times, high costs, and difficulties in achieving high precision, especially for castings with thin walls and intricate internal structures.
In recent years, sand mould 3D printing technology has emerged as a promising alternative to conventional casting mould-making techniques. This technology enables the rapid and flexible production of complex sand moulds, bypassing the need for conventional mould-making processes and significantly reducing production time and cost. Combined with low-pressure casting, this technology offers a powerful solution for the efficient production of high-precision shell castings.
This paper presents a comprehensive study on the development and verification of a shell low-pressure casting process based on sand mould 3D printing technology. The specific objectives of this study are:
- To design and optimize a conformal pouring system for shell castings using sand mould 3D printing technology.
- To simulate the filling and solidification processes of the shell casting using numerical methods.
- To experimentally verify the optimized casting process and evaluate the quality of the castings.
2. Materials and Methods
2.1 Shell Casting Design
The shell casting studied in this work has a complex internal cavity and thin walls. The casting measures 456 mm × 408 mm × 225 mm, with a maximum wall thickness of 16 mm and a minimum wall thickness of 3 mm. The internal cavity is variable in cross-section and connected by blades on both the inner and outer sides. The casting weighs 13.6 kg and is made of ZL114A aluminum alloy.
2.2 Sand Mould 3D Printing Process
The sand mould for the shell casting was produced using a binder jetting 3D printing process. An ExOne S-Max Pro printer was employed, with a build volume of 1800 mm × 1000 mm × 700 mm. The printing material consisted of silica sand bonded with furan resin. The key process parameters are summarized in Table 1.
Parameter | Value |
---|---|
Resin addition (%) | 1.50 |
Curing agent (%) | 0.30 |
Sand laying speed (mm/s) | 200 |
Resolution (mm) | 0.10 |
Layer thickness (mm) | 0.30 |
Table 1: Key process parameters for sand mould 3D printing.
2.3 Low-Pressure Casting Setup
The low-pressure casting setup consisted of a furnace, a crucible, and a low-pressure casting machine. The casting temperature was set at 735°C, and a pressure of 28 kPa was applied to ensure proper filling of the mould cavity. The mould was preheated to 90°C before pouring to reduce thermal shock and improve the filling process.
2.4 Numerical Simulation
Numerical simulation was performed using ProCAST software to optimize the pouring system and predict defects during the casting process. The simulation included the filling and solidification phases, with the aim of minimizing shrinkage porosity and ensuring proper feeding of the casting.
3. Results and Discussion
3.1 Pouring System Design and Optimization
A conformal pouring system was designed for the shell casting, as shown in Figure 2. The pouring system consisted of a main gate, runner, and ingates distributed around the casting. The ingates were designed to follow the contours of the casting blades, ensuring smooth metal flow and improved feeding.
The pouring system was optimized through numerical simulation, with the cross-sectional areas of the main gate, runner, and ingates adjusted to ensure even filling and minimize turbulence. The final pouring system design had a cross-sectional area ratio of 1.0:4.0:4.6 for the main gate, runner, and ingates, respectively.
3.2 Filling and Solidification Simulation
The filling and solidification processes were simulated using ProCAST. The simulation results indicated that the metal flowed smoothly into the mould cavity, with a maximum velocity of 23 mm/s. The temperature distribution during solidification was uniform, with the casting solidifying before the pouring system, allowing effective feeding and minimizing shrinkage porosity.
3.3 Experimental Results
The optimized sand mould was printed and assembled for casting. The mould was preheated to 90°C, and the metal was poured at 735°C under a pressure of 28 kPa. The casting was allowed to cool naturally for 12 hours before de-moulding.
The cast shell was inspected using X-ray radiography and dimensional measurements. The X-ray images showed no significant defects, confirming the effectiveness of the optimized pouring system. The dimensional accuracy was within ±0.9 mm, meeting the required tolerance of CT6 grade.
3.4 Microstructure and Mechanical Properties
The microstructure and mechanical properties of the cast shell were evaluated. The microstructure revealed a fine and uniform grain structure, indicative of good solidification conditions. The tensile strength and elongation of the casting were 328 MPa and 7.2%, respectively, showing improvements over traditional casting methods.
4. Conclusion
This study demonstrates the feasibility and advantages of integrating sand mould 3D printing technology with low-pressure casting for the production of complex shell castings. The conformal pouring system designed using numerical simulation ensured smooth filling and minimized defects. The experimental results showed that the cast shell had excellent dimensional accuracy and mechanical properties, meeting the stringent requirements of aerospace and automotive applications.