The progress of machine tool casting in China in the past 30 years can be seen in China International Casting Expo.
(1) Material of machine tool casting. Before the 1980s, almost all of the machine tool castings in China were gray cast iron, with grades of HT200 and HT250, 1-2 lower than that of foreign countries. HT300 castings can be produced after 1990s, and ht350 castings can be produced at the beginning of 21st century. In 2009, 11 machine tool foundries with certain scale were investigated. The results show that 100% of them can produce HT300 castings and 55% of them can produce ht350 castings. Figure 1 shows the machining center bed made of HT300. Modern high-precision machine tools have higher and higher requirements for the material rigidity of machine tool castings. In recent years, the use of ductile iron with high strength and high modulus of elasticity to produce machine tool castings is also increasing in China. All kinds of machine tools use ductile iron castings. Carbon steel with high rigidity can also be used in the production of large machine tools, which has the advantages of no pattern, low cost, short manufacturing cycle and simple process. Figure 2 shows the steel structure column of 246t large vertical car produced by Zhongxin heavy machinery casting and forging company.
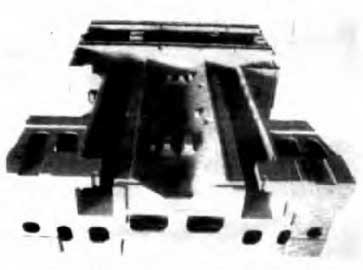
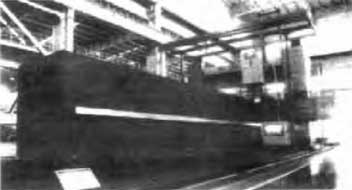
(2) The trend of the improvement of structural rigidity and thin wall of machine tool casting. In order to improve the anti deformation ability of machine tool, not only the elastic modulus of material should be increased, but also the structural rigidity of casting should be continuously improved. Double wall or multi-layer wall structure is often used in the stressed machine tool casting. Figure 3 shows the profile of the multi wall column on the German machine tool. In order to reduce the weight of machine tool, the thin wall of machine tool casting is an inevitable trend. Figure 4 shows the thin wall worktable cast by Sino Japanese joint venture Hanhe company.
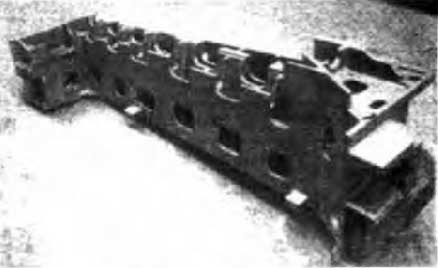
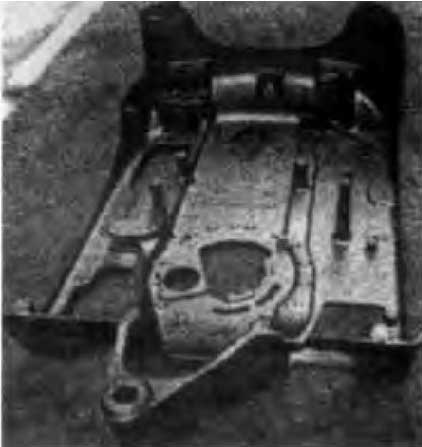
(3) The development of heavy and super heavy machine tools and the large-scale casting of machine tools. With the development of ship, aviation, petroleum, mine, chemical industry and metallurgy, the demand for heavy machine tools is increasing day by day. The growth of gross industrial output value of heavy machine tool industry in China from 2000 to 2009. It can be seen that the total output value of China’s heavy machine tool industry increased by an average of 43.38% in 2002-2008, 13.7 times higher than that in 2000.
At present, China has successfully manufactured the heavy-duty CNC gantry turning and milling composite machine tool with a workbench width of 16.2 m, the 16 m CNC vertical turning and milling composite machine tool, the CNC Floor Boring Machine with a boring bar diameter of Φ 260 mm and the super heavy gantry milling machine with a length of 60 m and two mobile gantry frames. The single weight of the column, cross frame, workbench, bed and frame of such machine tool can reach 40-160 t. Figure 5 shows the 135 t nodular cast iron crossbeam produced by Beijing No.1 Machine Tool Plant, and Figure 6 shows the working table (1 / 2) of 28 m vertical lathe produced by Wuhan heavy machine tool plant.
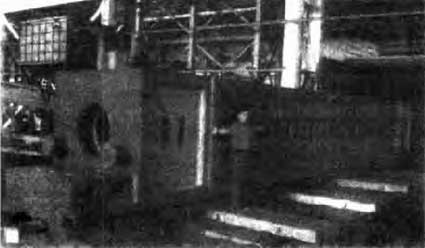
(4) The variety of machine guide ways. Before 1980s, in order to improve the wear resistance of bed, workbench, column, beam and other guide rails. Low alloy antifriction cast iron is widely used in domestic machine tool castings.
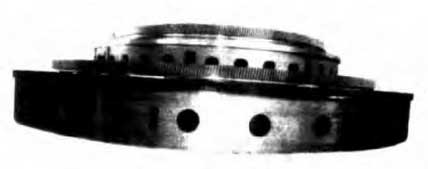
At that time, in addition to the use of alloy cast iron, there were also some machine tools using hardened guide rail. With the development of precision and large-scale machine tools, the guide ways of machine tools have developed to various types. Many machine tools have adopted inlaid steel guide ways, linear guide ways and hydraulic guide ways. According to incomplete statistics, China’s machine tool casting output has reached 2.2-3 million tons, and there is a trend of continuous growth.