Based on the fact that squeeze casting can form complex thick wall castings with dense internal structure and solution heat treatment, this process has developed into an important production method for high-grade castings, such as wear-resistant, pressure resistant, high-strength and toughness castings. Some new materials, such as high silicon aluminum alloy, high strength and toughness aluminum, magnesium, zinc based alloy and their composites, are also more and more used in production.
1. High silicon aluminum alloy squeeze casting
As crystallization under pressure is beneficial to the refinement of primary silicon, the elimination of porosity and the solution heat treatment, squeeze casting is an ideal advanced technology for the forming of high silicon aluminum alloy.
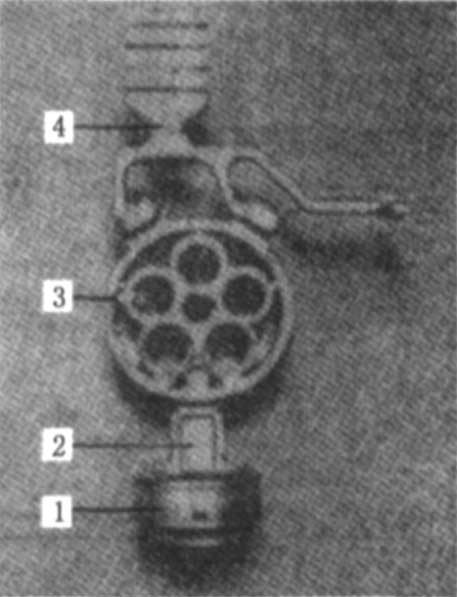
Figure is a picture of the air conditioning compressor cylinder block casting produced by dhxv350 squeeze casting machine of Toshiba, Japan. The alloy material is adc14 high silicon aluminum alloy of Japan, and the current production batch has reached hundreds of thousands of pieces per year.
2. Magnesium Alloy Squeeze Casting
Magnesium alloy castings are mostly produced by die casting process, but for castings with high quality and high mechanical properties, die casting is difficult, so magnesium alloy squeeze casting has a rapid development.
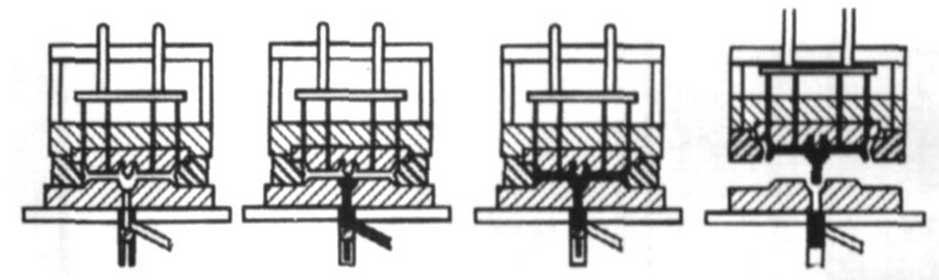
Chongqing University successfully put the motorcycle magnesium hub into batch production with its patented squeeze casting new technology.
Compared with the traditional squeeze casting, the new squeeze casting process has several innovations:
① In order to solve the problems of oxidation and cooling in the process of pouring, the heating pouring pipe was used to conduct closed quantitative pouring, and the magnesium alloy melt was isolated from the outside world;
② By adopting the mode of low pressure filling and high pressure solidification separation, the material cake in the pressing chamber is effectively reduced and the process yield is increased;
③ The traditional 3-piece-2-open structure is changed into 2-piece-1-open structure. In one process cycle, only one opening and closing structure is needed to realize pouring and taking of parts. The process flow is shortened, the process cycle time is reduced from 4-5 minutes to about 2 minutes, and the production efficiency is greatly improved.
In order to reduce the workload of process test, mold design and production debugging, the simulation and numerical optimization of the new squeeze casting process were carried out with magma software, and the optimized combination of process parameters was obtained, and the mold process structure was determined.
Magnesium alloy semi-solid casting, especially semi-solid die casting, has become a new bright spot. For this reason, the Japanese Institute of steel has designed and manufactured a magnesium alloy thixoforming machine. In reference [33], the microstructure and properties of AZ91D magnesium alloy prepared by twin-screw mechanical stirring and then squeeze casting of semi-solid propeller material were compared, which was significantly improved compared with that of conventional squeeze casting.
3. R & D and production of aluminum matrix composite
Because solidification under pressure is conducive to the infiltration and wetting of the liquid metal to the ceramic reinforcing agent, and increases its interface reaction and clamping force to the surface of the metal insert, squeeze casting is also an ideal method to provide low-cost composite and bimetal castings, which has been produced in large quantities at home and abroad.
The composite partially reinforced aluminum piston has been studied and produced by squeeze casting pressure infiltration technology in Southeast University, and has been widely used in many types of automobile engines. The reinforcing agent is alumina short fiber (δ type) and aluminum silicate short fiber (high aluminum type), and the base aluminum alloy is ZL108 and ZL109.
No.52 Institute has also carried out many researches in this field, and has made many achievements in composite piston and track shoe, and has been used in squeeze casting production.
4. Research and development of zinc base alloy and steel materials
High aluminum zinc base alloy (such as ZA27, ZA43, etc.) solidified under pressure can obviously refine its alloy structure, overcome its serious tendency of shrinkage and segregation, so squeeze casting is also the preferred production process for high-quality castings of this kind of alloy. Table 3 lists the comparison of mechanical properties and wear resistance of ZA27 alloy extrusion casting and metal mold casting respectively. It can be seen that the extrusion casting has obvious advantages. Similar results have been obtained for ZA43 alloy. It can be predicted that squeeze casting high aluminum zinc base alloy will have a good application prospect in wear-resistant parts and stamping die parts.
Although a lot of work has been done in the development and production of iron and steel squeeze casting products at home and abroad, but due to the problem of mold life, large production batches can not be formed. In recent years, Beijing Jiaotong University has cooperated with enterprises in the research of mold, coating, technology and other aspects, and has made some progress in the product development of coal mine equipment and electrified railway accessories.