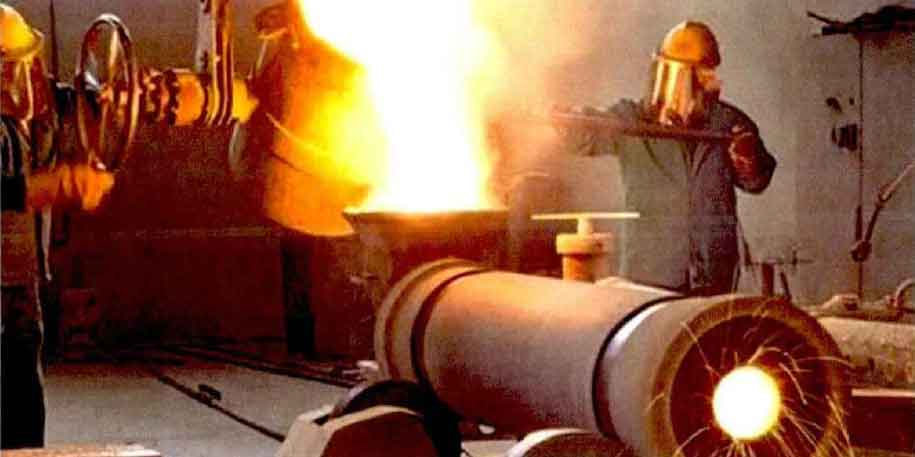
In addition to composite rollers and composite pipes, ring parts such as bearing rings and flanges are used as key connecting, slewing and supporting basic parts in the manufacturing fields of major equipment such as high-speed railways, ocean going ships and deep space exploration. They have many varieties, large quantities and wide applications. Different from the long axis / tube components such as composite roll and composite seamless pipe, the traditional manufacturing process of disc-shaped bimetallic ring parts is to insert and assemble the single ring parts after centrifugal casting respectively, or to assemble the single ring parts through upsetting, punching and other processes for rolling forming. The process flow is lengthy, and there are problems such as interface warping, large cracking tendency, poor internal and external contact quality and low bonding strength. With the development of bimetallic centrifugal casting composite technology in recent years, the centrifugal casting process can not only directly produce key basic components such as composite rollers and composite pipes with high hardness and wear resistance, but also produce bimetallic centrifugal casting ring billets with excellent performance and quality, which can be formed into high-performance bimetallic composite rings after direct hot rolling, as shown in the figure.
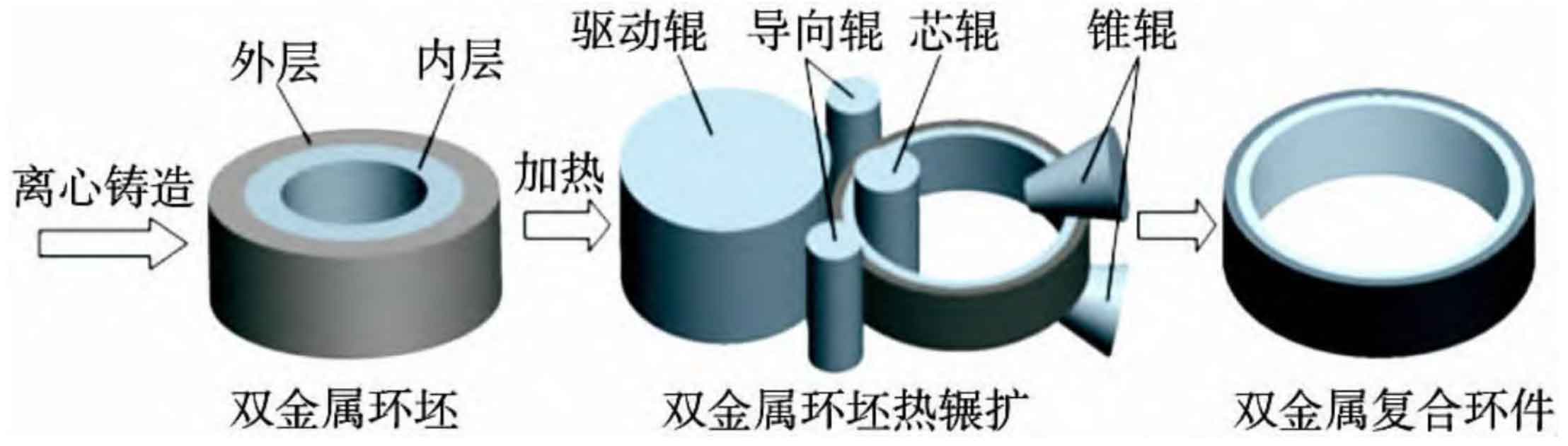
As the bimetallic ring is a disc-shaped composite component with small height diameter ratio, the vertical centrifugal casting process can be used to metallurgical combine the outer layer and inner layer of two metals of different materials to form a bonding layer of a certain width, and then hot rolled into a bimetallic composite ring with increased bonding layer width and improved performance. In the process of vertical centrifugal casting, the thickness ratio of inner and outer layers can be adjusted according to the actual needs to give full play to the respective performance advantages of inner and outer materials. When one side performance requirements are high, bimetallic rings can replace rare and precious metals to solve the problems of poor interface contact quality and low bonding strength in the production of traditional bimetallic rings. However, the vertical centrifugal casting process is usually used for bimetallic ring billets. The metal flow filling law, the deformation behavior of inner and outer metals and the control of bonding interface in the centrifugal casting process are obviously different from those in the horizontal centrifugal casting of long shaft / tube composite rolls and composite tubes. The key to realize the metallurgical bonding between the interfaces of bimetal composite rings is to control the interface microstructure, the thickness of inner, outer and bonding layers, and the element diffusion behavior of bonding layers. By studying the key technologies such as the centrifugal casting theory and quality control of bimetallic composite ring billets, the microstructure evolution mechanism and performance control of bimetallic composite centrifugal casting billets, a short process manufacturing method and quality control scheme for centrifugal casting bimetallic rings are constructed, which can not only provide an efficient and low-cost production method for heterogeneous bimetallic rings such as low carbon steel / stainless steel, aluminum / steel and aluminum / magnesium, It can also provide a theoretical basis for the research and development of short process manufacturing technology similar to aluminum based bimetallic composite components, and realize the integrated short process shape control / controllability manufacturing of high-performance bimetallic composite components.
Therefore, in the future, the bimetallic centrifugal casting composite technology should also focus on the following aspects: the interface bonding quality of the bimetallic composite components of centrifugal casting is greatly affected by the flux. A reasonable flux can reduce the defects such as interface pores and slag inclusions. A new flux with low density, easy melting and strong applicability can be developed, which can not only prevent the oxidation of the molten metal, but also make the molten metal have the characteristics of reducibility; Bimetallic composite components are mostly made of high chromium cast iron, and there is little research on other materials. Therefore, composite components of different materials can be developed to provide more choices for horizontal and vertical centrifugal casting processes of bimetallic composite components; The bimetallic billets in the composite process of centrifugal casting are modified by means of external magnetic field and multi-element alloy modification, so as to reduce the defects of uneven composition distribution and improve the stability of transition layer, so as to obtain better ring billets; Strengthen the research on the diffusion behavior of interface elements and interface bonding mechanism, use the finite element simulation technology to simulate and analyze the bonding process of bimetal centrifugal casting, study the change law of bonding layer thickness and composition distribution, and solve the problem of internal and external structure uniformity of ring; Different heat treatment processes are used to study the causes of cracks, holes and other defects in the bonding layer of composite components and their elimination measures, so as to ensure the bonding performance of bimetal composite components.