The performance of the die forged connecting rod is reliable. The inspection method is simpler than that of the cast connecting rod, and it can be mass produced on the automatic line. There are many dimensions and specifications of the die forged connecting rod. For example, the die forged connecting rod produced by Brockhaus manufacturer of zuige in pleten, Germany, has a mass of 100g, a total length of 125mm, and a center distance of 90mm between two holes; The connecting rod with a mass of 8.7kg has a total length of 450mm and a center distance of 300mm between two holes. The main material is AFP steel. The connecting rod produced by alfin and Kessler machine works in Arlen, Germany for the newly developed high-power marine diesel engine has a blank mass of 1100kg, a total of 2150mm, a maximum width of 670mm and a thickness of 287mm, a large and small head hole diameter of 300mm and 200mm respectively, and is made of 42CrMo4 steel. The size of each side of the square head steel ingot is 360mm. During the production of the connecting rod, the quality distribution, pre forging, precision forging, tempering and shot peening shall be carried out first, and then other processing shall be carried out. The production methods of die forged connecting rod include:
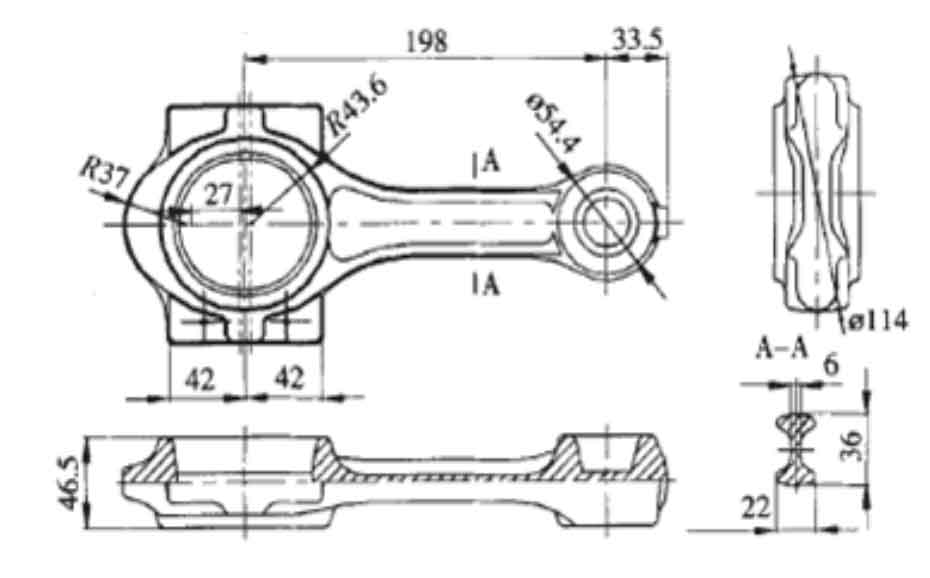
- Single piece die forging of Dalian rod. When large pieces of connecting rod are produced in small batches, the connecting rod can be rolled as a single piece and then forged. After four rolling stages, the Dalian rod is pre pressed, fine pressed, punched and deburred twice on a 40Mn press.
- Integral or split die forging of two-piece straight-line connecting rod. The split connecting rod is rolled and preformed for 4 times, and then the initial pressing, pre extrusion, fine pressing and deburring are carried out on a 31.5MN press. The overall connecting rod is rolled for 4 times, and then the pre pressing, fine pressing, punching and deburring are carried out twice on a 20Mn press.
- For integral or split die forging with two pieces arranged in parallel, rolling forming can be omitted for the die forging connecting rod with two pieces arranged in parallel, but its flash loss is more than that of the die forging connecting rod arranged in a straight line, and the fiber distribution is also worse.
- In addition, the advanced production process of using high carbon non quenched and tempered steel to adopt the controlled cooling after forging, and using the expansion and fracture method (i.e. separation method) to separate the connecting rod big end instead of the traditional quenching and tempered steel to produce car connecting rod by using quenching + high temperature tempering is an advanced technology for the production of car parts abroad in the 1990s.
- Powder metallurgy connecting rod: among connecting rods of various materials, powder metallurgy connecting rod has advantages in hardness, wear resistance and strength. For example, the powder metallurgy connecting rod with the mass of 400g and the material of Sint F30 has high precision and small quality error. The subsequent processing is more than 50% less than the traditional casting connecting rod or die forging connecting rod.
Powder metallurgy is a newly developed process, and some foreign engines have been well applied, such as Toyota Motor Company in Japan, KREBSOGE company in Germany, Ford Motor Company in the United States, etc. all use engine connecting rods made of powder metallurgy. The small connecting rods of air compressors, motorcycles and various compressors are mainly cast aluminum alloy connecting rods, and the amount is also large.