The wax impregnation process plays an important role in improving the strength and surface quality of the specimen. According to the previous experimental research, the wax molecules enter into the SLS prototype along the gap of PS particles, which mainly improves the strength of the sintered specimen, but little improves the surface quality of the specimen. Therefore, the second wax impregnation method is adopted in this experiment. The specific process is as follows: the first soaking temperature is 65 ℃ and the soaking time is 20s; the second soaking temperature is 75 ℃ and the soaking time is 4S. According to the previous wax immersion test, after one-time wax immersion, the sample will have a certain volume change due to the entry of high-temperature wax liquid, while the second wax immersion has a short action time and the original PS on the surface of the sample after one-time wax immersion The results show that the porosity of the particles is greatly reduced, and the wax layer with a certain thickness is uniformly adhered on the surface of the specimen after the second wax immersion, but it has no effect on the overall volume change of the specimen. Therefore, this paper studies the first wax leaching and the second wax leaching respectively.
Among them, the dimensional accuracy of wax pattern after one wax immersion is the relative error of wax pattern relative to SLS prototype
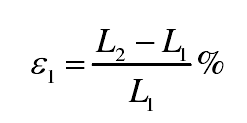
Where,
ε 1 – the relative dimension error of the wax pattern relative to the SLS prototype after one-step wax soaking;
L2 – the size of the wax pattern after a single wax immersion, mm.
It can be seen from Figure 1 that the relative dimension error of wax pattern relative to SLS prototype changes with the change of test position, which indicates that the size of specimen has an effect on the dimension error of wax pattern after one-time wax immersion, and the relative dimension error of Z direction decreases gradually with the increase of Z direction dimension, which indicates that the smaller the Z direction dimension is, the wax liquid will completely soak the sintered part in the same wax immersion time With the increase of Z-direction dimension, the volume expansion caused by wax liquid is relatively large, and the volume expansion caused by wax liquid is relatively small. With the change of test position, the error in Y direction will increase. During this period, with the change of test position, the size in Z direction will gradually increase, the plane in Y direction will also gradually increase, and the volume change will further increase. The error of X direction decreases with the change of test position, mainly with the increase of Z dimension. Combined with the analysis of the relative error results of SLS prototype relative to CAD model, it is not difficult to find that the position 1 in X direction is mainly affected by the warpage deformation of SLS prototype, and the position 2 in X direction is mainly affected by the effect of wax liquid on the volume of specimen With the increase of temperature, the infiltration of wax in the X direction decreases, and the volume increase caused by wax decreases.
It can be seen that the relative error of X, y and Z dimensions is x < Z < y, which indicates that the relative error of each dimension of the specimen after one-time wax immersion is different. The main performance is that the more the wax liquid infiltrates, the larger the volume expansion of the specimen will be. The average relative error of X direction is negative, which indicates that after a wax soaking, the X direction decreases with the wax liquid entering, so that the size shrinkage of X direction is larger than the volume increase of X direction with the solidification of wax liquid. The size error transfer rule from wax pattern to SLS prototype is as follows.
The transmission law of X direction is as follows

The transfer law of Y direction is as follows

The transfer law of Z direction is as follows

Where, ε 2x, ε 2Y, and ε 2Z are the relative errors of X, y, and Z three-dimensional average dimensions of the wax pattern relative to the SLS prototype after one wax immersion. It is considered that the effect of the first wax immersion is that the wax liquid enters into the SLS prototype to strengthen the specimen, while the second wax immersion is mainly to improve the surface quality of the specimen. Therefore, it is necessary to study the relative size error of the specimen after the second wax immersion compared with that after the first wax immersion.
It is not difficult to find in Figure 2 that the relative errors of dimensions at different test positions are all positive after the second wax immersion, which indicates that the size of the specimen increases in different degrees at different positions after the second wax immersion. The relative errors of dimensions at these five test positions range from 0.268 to 0.788. Through analysis and calculation, the average relative errors of dimensions in three directions are 0.547%, 0.529% and 0.529% respectively 589%, the thickness of wax layer on one side is 0. 0100 mm to 0. 0683 mm, and the average value is 0. 0392 mm. The results show that the relative error of X and Y directions is smaller than that of Z direction, which is mainly due to the existence of XY sintering surface in Z direction, resulting in the pores between PS particles in this plane being smaller than those in other planes, so the wax liquid in XY plane adheres more to the surface of the specimen, which leads to the larger relative error of Z direction. The results show that the relative error of X-direction dimension increases all the time. The main reason is that with the increase of Z-direction dimension, the x-direction wax penetrates further through the secondary high-temperature wax, resulting in a certain volume increase. However, with the increase of Z dimension, the relative error of Y and Z dimensions first increases and then decreases. Due to the secondary high temperature wax liquid, some wax liquid infiltrates into the specimen, which leads to the increase of specimen volume. Accordingly, through the analysis of the relative error of the size of the primary and secondary wax impregnation, it is not difficult to find that the volume of the sintered parts will increase in the primary wax impregnation, especially when the size of the sintered parts is smaller, the corresponding size increases more. However, the second wax immersion mainly acts on the surface of the specimen, and the relative error of the three-dimensional dimension of the specimen is not obvious after the second wax immersion. If the difference of the three-dimensional dimension is within the allowable range, it is considered that there is no difference.