By adding different content of copper and different ratio of copper and chromium, the mechanical properties and cutting properties of gray cast iron were compared, and the effect of alloy element copper on the properties of gray cast iron was studied. The chemical composition of the cast sample is shown in Table 1.
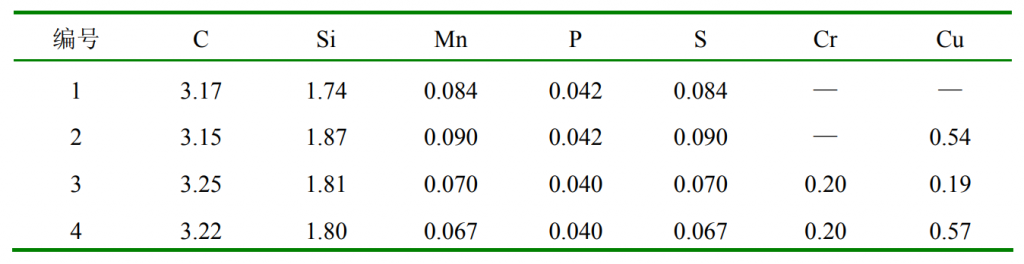
The mechanical properties of gray cast iron samples prepared under different conditions are shown in Table 2. It can be seen from table 2 that the addition of alloy elements can significantly improve the tensile strength of gray cast iron and make the sample meet the requirements of HT300. The addition of Cu and Cr can stabilize and refine the pearlite structure, so as to improve the mechanical properties of gray cast iron. It can be seen from samples 3 and 4 that the Cr content is 0.2%, and the tensile strength of gray cast iron increases with the increase of copper content. After adding alloying elements, the Brinell hardness of gray cast iron increases slightly, and the hardness of gray cast iron with different alloying treatments is basically the same. When Cu and Cr are added, the section sensitivity of gray cast iron decreases.
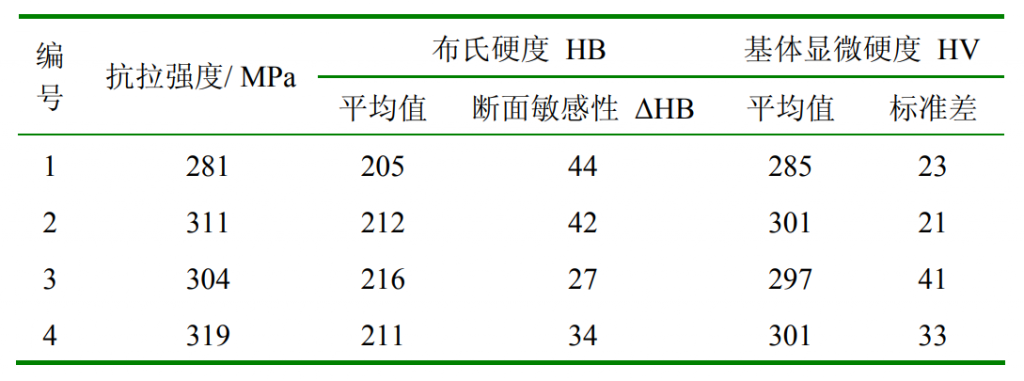
The variance of microhardness was calculated to observe the dispersion of hardness value in each part, so as to evaluate the uniformity of matrix structure of gray cast iron sample. According to the data in Table 2, the microstructure uniformity of gray cast iron becomes worse after adding 0.2% CR. When the addition amount of alloying element Cr is fixed at 0.2%, the microstructure uniformity of gray cast iron becomes better with the increase of Cu content. It can be seen that the addition of Cu and Cr Alloys can improve the non-uniformity of pearlite microhardness in the sample treated with 75sife.
The maturity (RG), hardening (Hg) and quality coefficient (QI) of gray cast iron are also used as the parameters for analysis and comparison. The results are shown in Table 3. The decrease of eutectic degree means the decrease of carbon equivalent. Although the tensile strength is improved, it leads to the decrease of liquid iron fluidity, the increase of shrinkage and internal stress, the increase of hardness and so on. Maturity (RG) is the ratio of measured strength to normal strength, RG, to represent the actual strength excess; RG > 1 indicates that the actual hardness of gray cast iron is greater than the theoretical hardness, and the size represents the range of improvement. The degree of hardening (Hg) uses the ratio Hg of the actual hardness to the normal hardness to represent the reduction of the actual hardness compared with the normal hardness; Hg < 1 indicates a lower hardness under the retention strength. Therefore, if maturity RG > 1 and hardening Hg < 1, their ratio Qi = RG / Hg > 1. Generally, Qi is 1.2-1.4, which is called the quality coefficient. The quality coefficient Qi > L indicates that gray cast iron has good casting and processing properties while maintaining high strength.
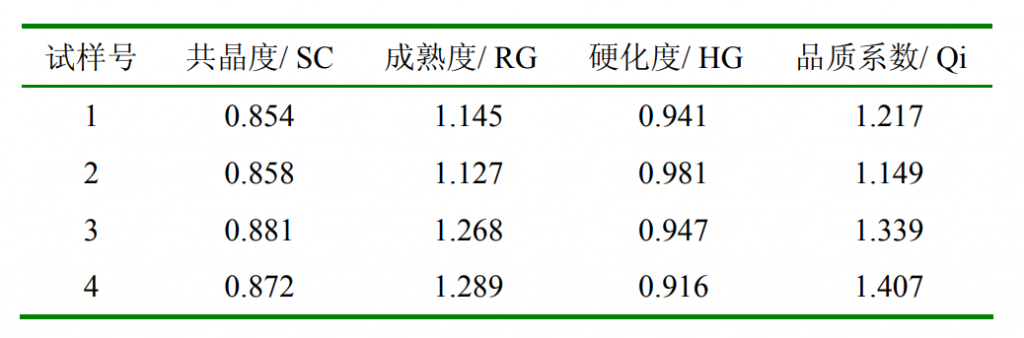
It can be seen from table 3 that the quality coefficients of the four groups of samples are greater than 1, indicating that the quality of gray cast iron in this experiment is high-quality. The maximum quality coefficient of sample 4 is 1.407 and the minimum quality coefficient of sample 2 is 1.149. The quality coefficient of the samples added with Cu and Cr increased.