In order to better study the fatigue wear resistance of gray cast iron brake material, after every 150 thermal cycles, simulate the braking of brake drum during fatigue, and conduct sliding friction for 20 hours. The load is 100N, the friction speed is 0.15m/s, the friction pair is ceramic brake pad material, and the matrix hardness is 61.6 hv0.5. The effect of carbon content on the wear properties of Laser Biomimetic gray cast iron was studied by measuring the wear amount of different carbon content and comparing the wear morphology.
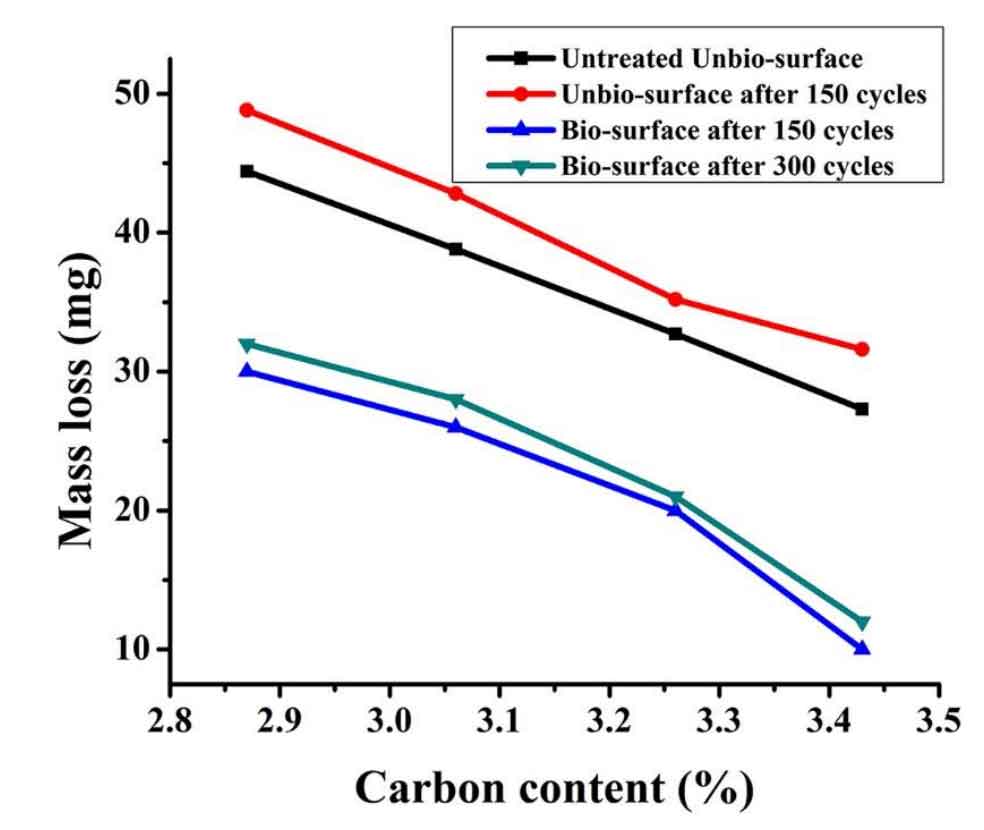
Figure 1 shows the wear amount of gray cast iron on non bionic surface and bionic surface under different cycle times. It can be seen from Figure 1 that with the increase of carbon content, the wear amount of gray cast iron on the non bionic surface gradually decreases. The reason may be that on the one hand, the increase of carbon content makes the matrix pearlite more complete and the overall hardness is also improved; On the other hand, the amount and size of graphite increase with the increase of carbon content, which plays a certain role in lubricating the friction and wear of gray cast iron. Therefore, with the increase of carbon content, the matrix hardness increases and the wear of gray cast iron decreases. The figure shows that after 150 thermal cycles, the wear of gray cast iron on the non bionic surface is higher than that without thermal cycle. Although the above shows that after the friction and wear of gray cast iron, the hardness of the worn surface of gray cast iron due to work hardening is slightly higher than that without treatment, before the wear of gray cast iron, the hardness of the matrix structure is reduced due to the thermal cycle. Under the same pressure and friction pair, the plowing is stronger and the wear debris is more. Therefore, the wear of gray cast iron on the non bionic surface after 150 thermal cycles is higher than that without treatment. However, from the figure, we can also see that with the increase of carbon content, the reduction of non bionic surface wear tends to slow down. The reason may be related to the increasing number of cracks and graphite pits formed in the process of thermal fatigue.
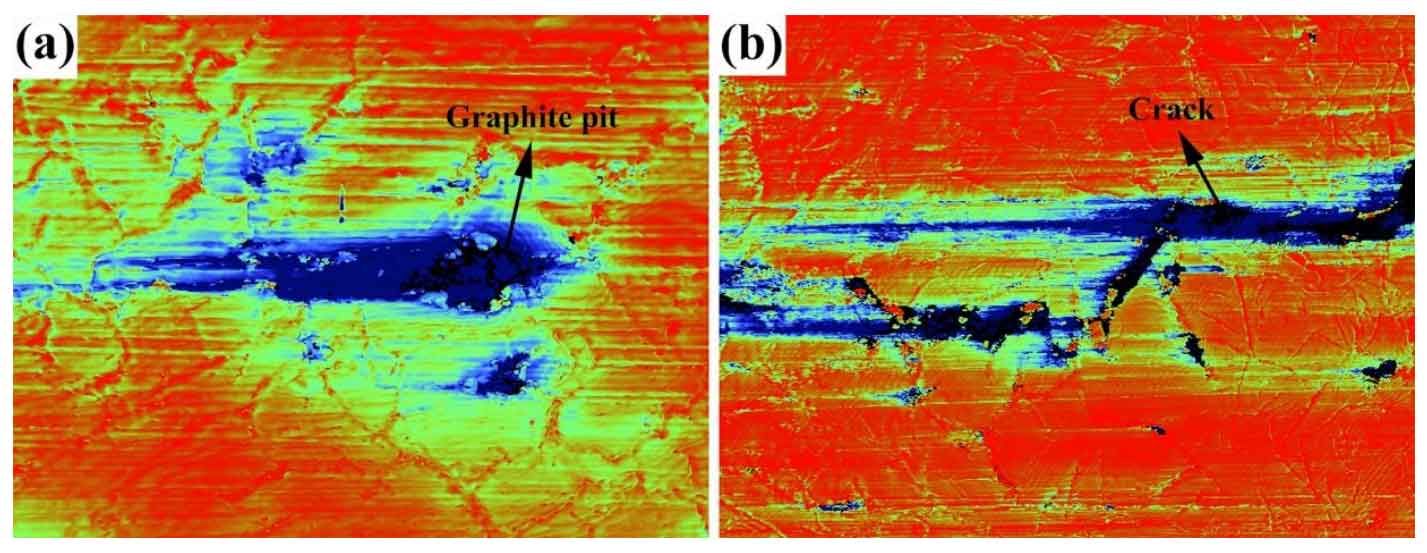
Figure 2 shows the wear morphology of gray cast iron at graphite pits and cracks. In the process of thermal cycle, the bonding strength between the surface graphite and the matrix is reduced due to thermal expansion, cold contraction and oxidation. The graphite is not closely combined with the matrix and separated from the matrix, forming a large number of graphite pits on the friction surface; With the increase of carbon content, the number of graphite pits increases gradually. Through the elemental analysis of the graphite pit with EDS (as shown in Figure 3), it is found that the content of iron element decreases greatly and the content of oxygen element increases at the graphite pit, indicating that there are a large number of iron oxide particles at the graphite pit, and the same phenomenon can also be seen at the crack. This shows that during the friction process, a large number of oxide particles with high hardness are slowly stored in the gap between the graphite pit and the crack, while the iron oxide particles are free hard phase, which ploughs around the graphite pit and the crack, increasing the wear of gray cast iron. Therefore, with the increase of carbon content, the wear amount of gray cast iron on the non bionic surface decreases gradually, but the reduction range is slightly reduced due to the existence of graphite pits and cracks.
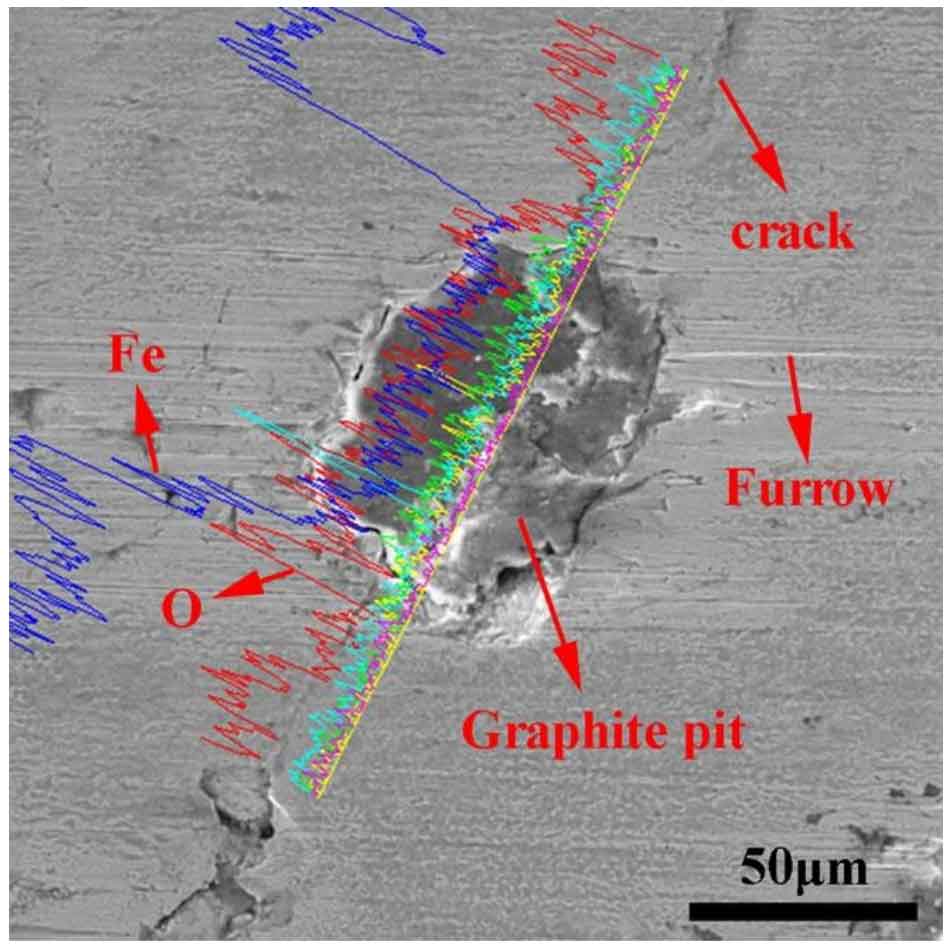
However, compared with non bionic surfaces, the wear of all bionic surfaces is significantly lower. This is because the bionic surface has the structure of soft and hard connection, which supports the friction pair on the hard phase unit, carries most of the stress, and the soft phase absorbs the wear debris produced in the friction process; As a hard unit, the bionic unit itself is in the form of white cast iron, which is extremely wear-resistant. Therefore, the wear resistance of the bionic surface is greatly improved compared with the non bionic surface. As shown in Figure 4, it is the wear morphology of gray cast iron at the junction of bionic surface unit and matrix. From the figure, it can be seen that the furrow in the unit area is very shallow, and there is almost no wear of gray cast iron, while in the matrix area, there are deep furrows, and the wear of gray cast iron is more serious. When the matrix gray cast iron is seriously worn, the unit body plays a supporting role for the friction pair due to its hard wear resistance, so as to improve the wear resistance.
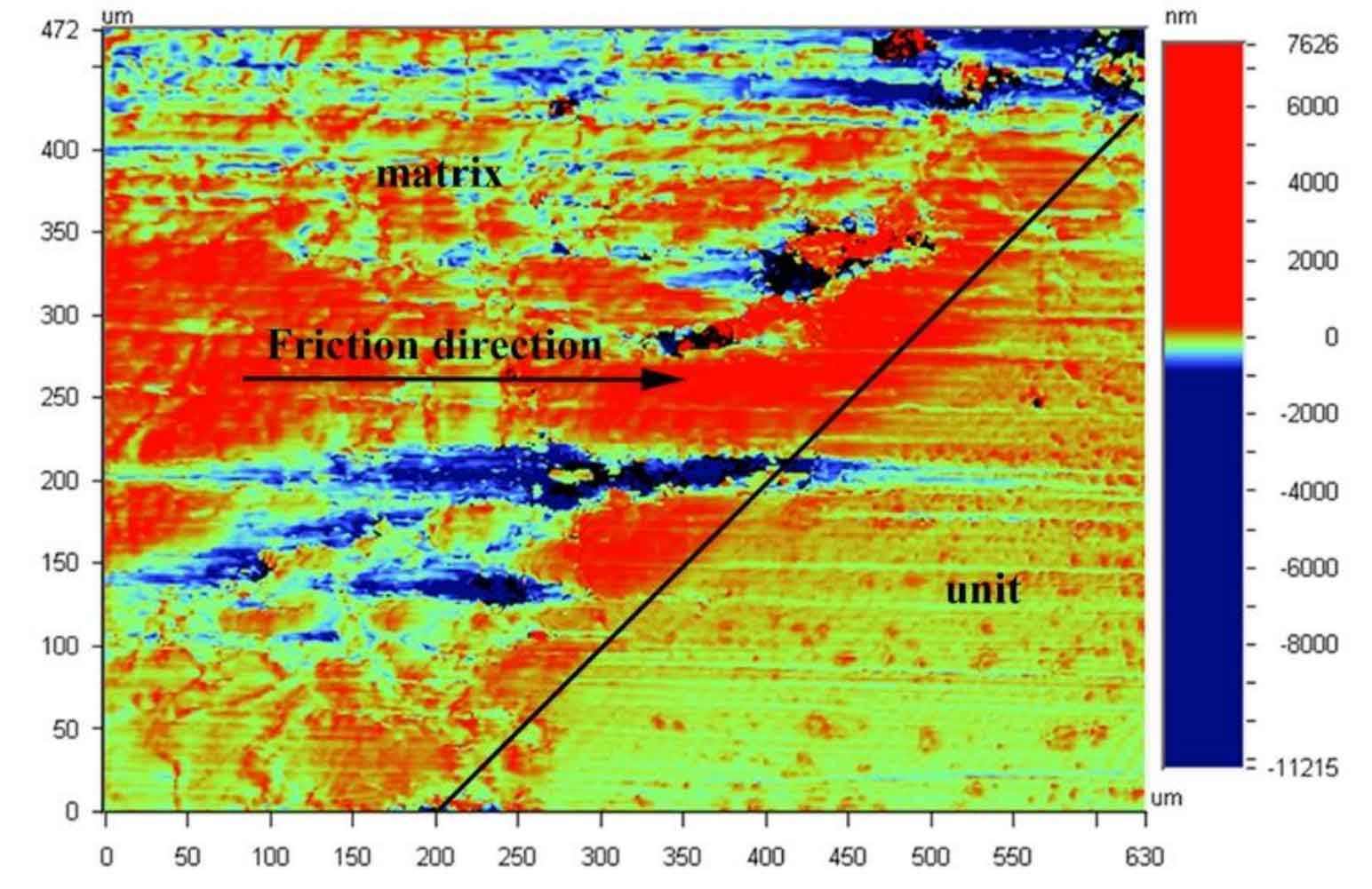
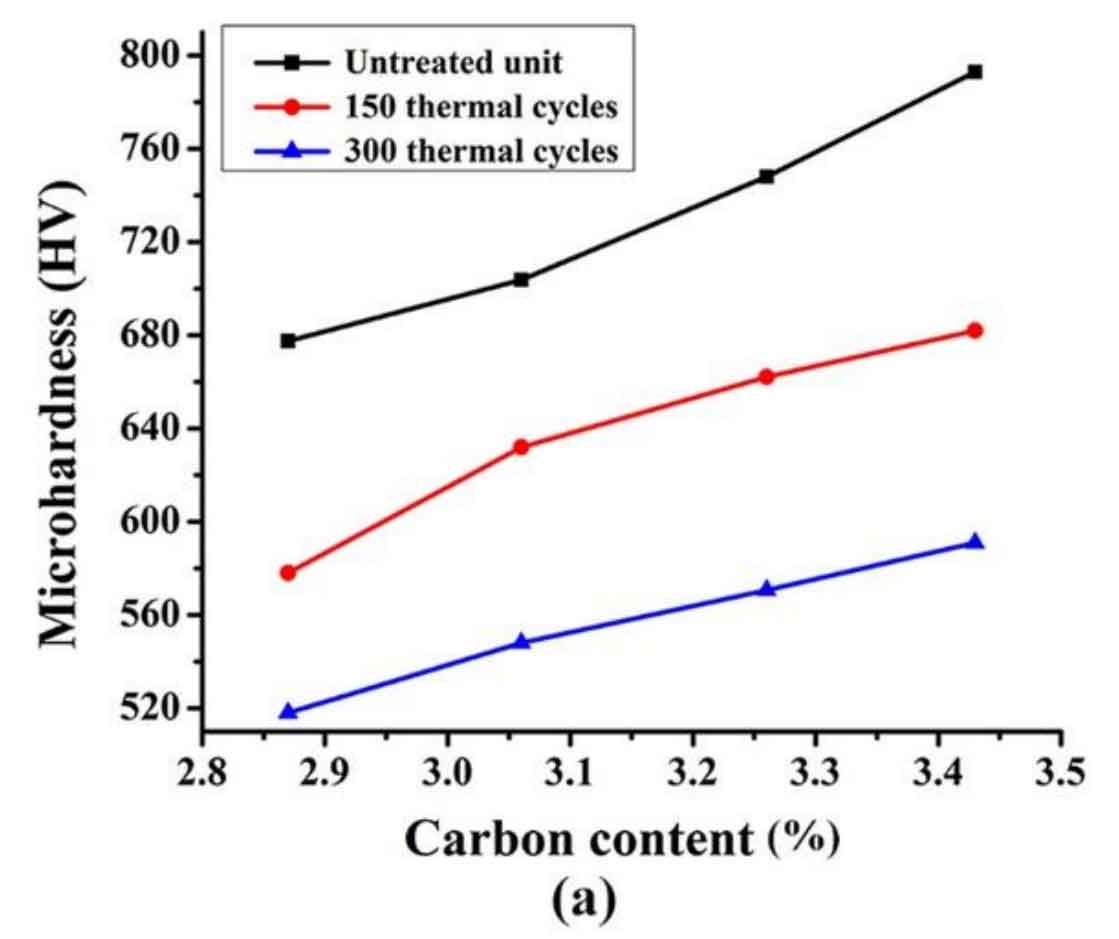
By comparing and analyzing the relationship between wear resistance and carbon content of bionic surface, we find that similar to non bionic surface, the wear amount of gray cast iron on bionic surface decreases gradually with the increase of carbon content. This is directly related to the hardness of the unit body. Fig. 5 shows that the hardness of the unit body increases with the increase of carbon content and plays a major role in resisting material wear. On the other hand, the thermal fatigue cracks and graphite pits on the bionic surface are greatly reduced due to the soft and hard bionic structure and the supporting effect of the unit on the friction pair. Figure 6 shows the wear morphology of gray cast iron in the matrix area of the bionic surface. In the bionic surface, there are few defects such as graphite pits and thermal fatigue cracks that increase the wear amount of gray cast iron, but there are a large number of matrix peeling areas, and the lower the carbon content, the more serious the matrix peeling. With the increase of carbon content and graphite surface hardness, the number of friction pits in the lubrication process increases, and the wear range of graphite surface increases. The number of thermal cycles also has a great influence on the thermal fatigue resistance of bionic surface. It can be seen from the analysis that the hardness of the unit body decreases with the increase of the number of thermal cycles, so the supporting effect of the unit body on the friction pair decreases and the wear rate of gray cast iron increases.
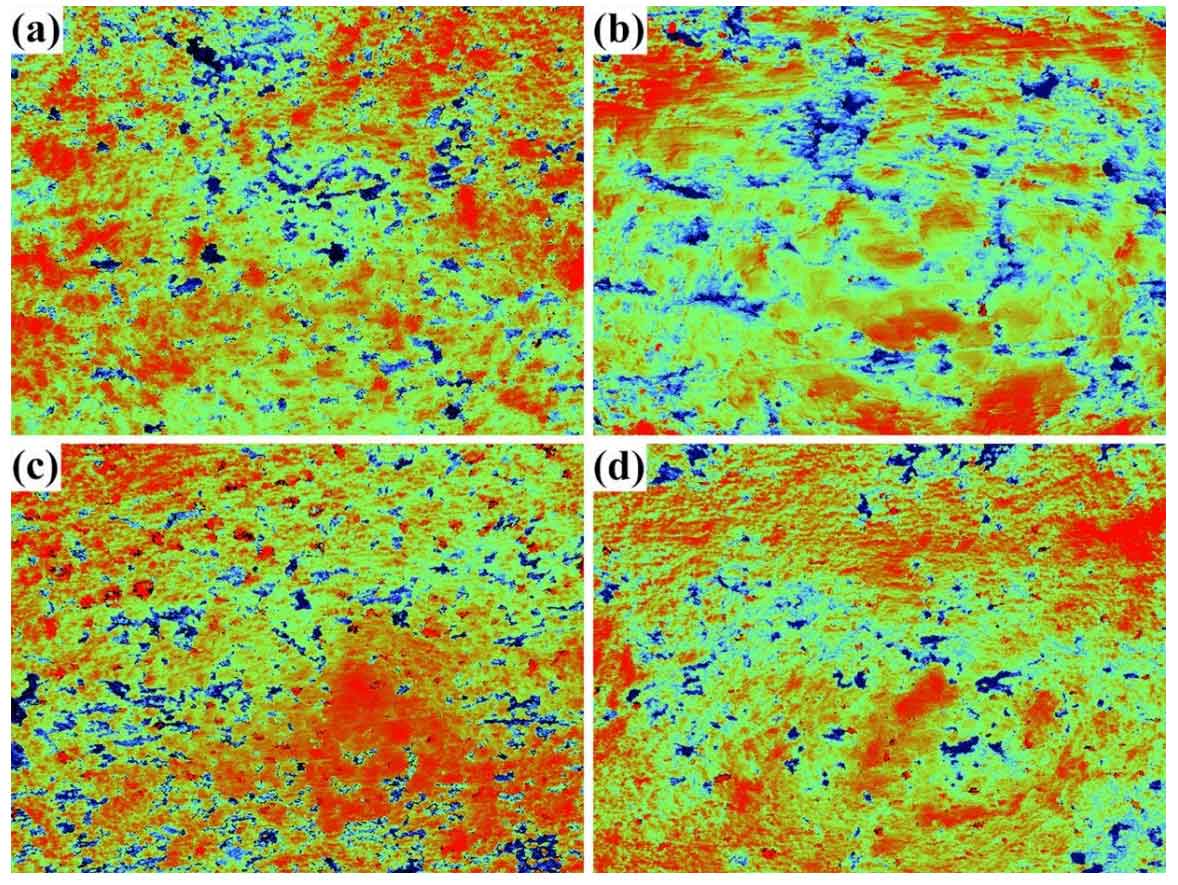