Most gray cast iron castings can become machine parts only after turning. The turning performance directly affects the processing quality and production cost of gray cast iron castings. The turning performance of materials is mainly reflected in several aspects: turning resistance, turning tool wear, chip morphology and workpiece surface roughness. Next, we will compare and analyze the turning performance of experimental gray cast iron from the above aspects.
The table below shows the cutting resistance of gray cast iron after inoculation treatment with different inoculants. The comparison diagram of cutting resistance is drawn according to the data in the table, as shown in Figure 1, where FX is the main cutting force, FY is the feed resistance and FZ is the cutting depth resistance. The cutting resistance of the sample in the turning process can reflect whether the material itself is easy to be turned to a certain extent. The greater the cutting resistance, the less easy the material is to be turned, otherwise, it is easy to be turned. Through the comparative analysis of the cutting resistance of the sample in the turning process, it can be seen that the cutting force F is C → a → B → d from small to large. Among them, the cutting force of the experimental gray cast iron sample D inoculated with silicon, zirconium and manganese is the highest, that is, the sample D is the most difficult to be turned, According to the cutting resistance, the order of turning performance of experimental gray cast iron from high to low is: C → a → B → D.
Fig. 2 shows the change curve of tool wear of experimental gray cast iron a, B, C and D with the increase of turning length during turning. The turning conditions are as follows: cutting amount AP = 0.7mm, feed rate f = 0.091mm/r, cutting speed VC = 59.3m/min and tool walking times of 3 times. It can be seen from the tool wear curve shown in Figure 2 that the four kinds of experimental gray cast iron enter the normal wear stage when the cutting length is 4300m. When turning the experimental gray cast iron sample B, when the cutting length reaches 6800m, the tool wear enters the rapid wear stage, the wear amount increases rapidly, and the tool breaks. When turning the experimental gray cast iron sample C and D, When the cutting length is 7600m, the tool enters the rapid wear stage. When turning the experimental gray cast iron a sample, the tool wear is very small. The wear amount of tools used in the four kinds of experimental gray cast iron is from small to large: a → D → C → B, that is, according to the change of tool wear with the increase of cutting length, the order of turning performance of experimental gray cast iron from high to low is: a → D → C → B.
Fig. 3 shows the tool wear morphology of experimental Gray Cast Iron Inoculated with different inoculants when the cutting length is 6800m. It can be seen from the figure that the tool wear of experimental gray cast iron samples C and D inoculated with silicon zirconium aluminum and silicon zirconium manganese is not different. The tool wear of experimental gray cast iron sample B inoculated with silicon zirconium is the most serious, and the turning tool can no longer be used, The tool wear of gray cast iron sample a inoculated with 75 ferrosilicon is the smallest. The wear of turning tool in turning gray cast iron is mainly stick corrosion wear. The wear failure is due to the formation of micro cracks on the surface of tool material due to the repeated change of stress and strain, resulting in the gradual falling off of material, but also including a certain degree of abrasive wear. According to the tool wear under actual working conditions, the order of turning performance of experimental gray cast iron from high to low is: a → D → C → B.
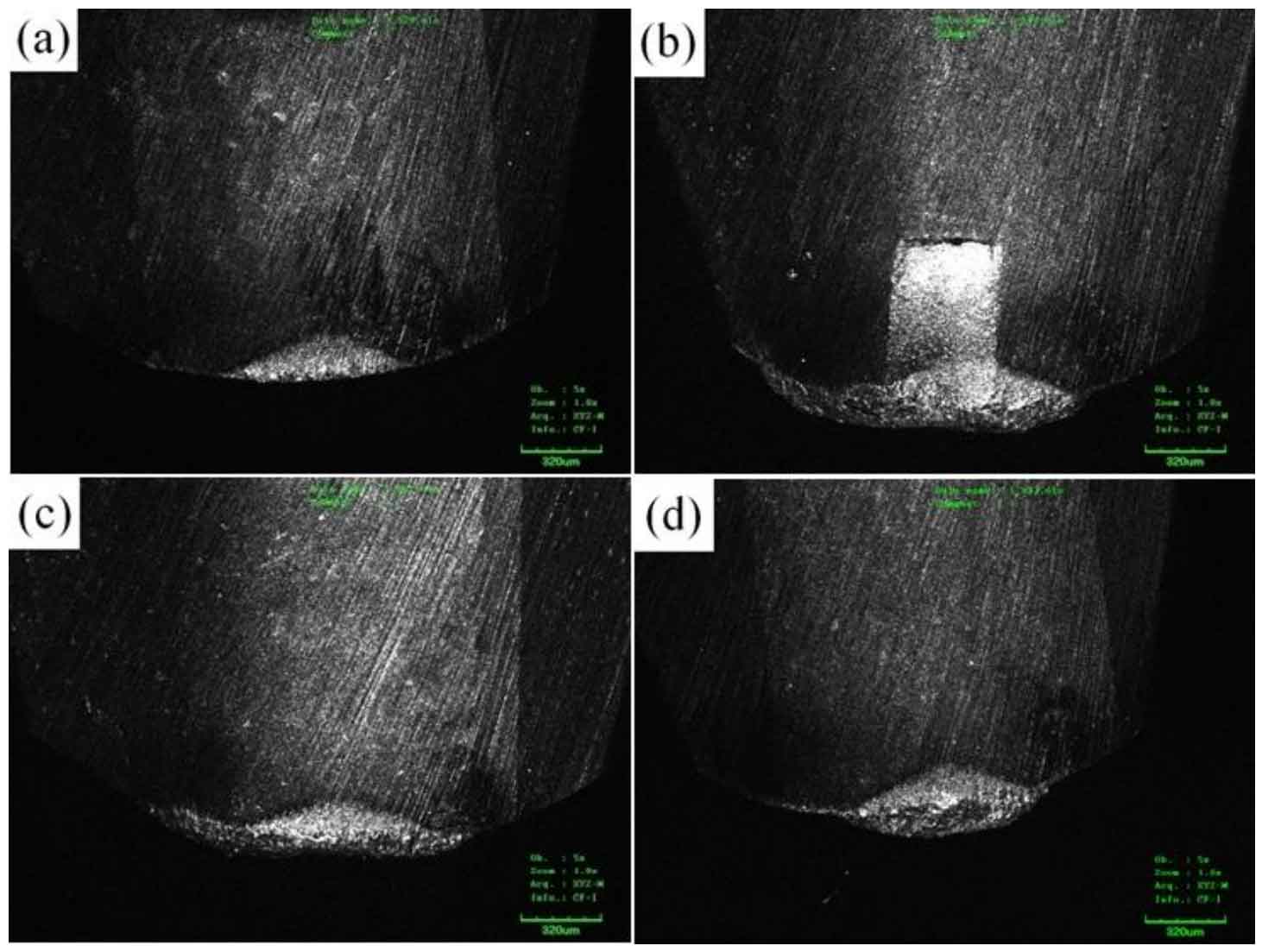
(c)sample C—Zr-Si-Al inoculation treatment;(d)sample D—Zr-Si-Mn inoculation treatment.
The surface roughness of cutting samples of gray cast iron was tested. Because the turning process is a dynamic process, the instability of cutting resistance will fluctuate the elastic deformation of cutting tools and gray cast iron, which will affect the surface roughness of cutting samples. The surface roughness of four kinds of experimental gray cast iron is a → C → B → d from small to large. The larger the surface roughness is, the worse the turning performance is. According to the turning surface roughness, the order of turning performance of experimental gray cast iron from high to low is: a → C → B → D.
Figure 4 shows the chip morphology of experimental gray cast iron a, B, C and d after different inoculation treatment. It can be seen from the figure that the thickness of chip back sawtooth of experimental gray cast iron B sample after silicon zirconium inoculation treatment is relatively thick, while the thickness of chip back sawtooth of experimental gray cast iron a sample after 75 silicon iron inoculation treatment is the thinnest, and the thickness of chip back sawtooth of experimental gray cast iron a sample after silicon zirconium aluminum The thickness of sawtooth on the chip back of C and D samples of experimental Gray Cast Iron Inoculated with silicon, zirconium and manganese is in the middle. The thinner the sawtooth thickness on the back of the chip, the better the turning performance. According to the chip morphology, the order of turning performance of experimental gray cast iron from high to low is: a → D → C → B. From the above comparative analysis of the variation curves of tool wear of experimental gray cast iron a, B, C and D with the increase of cutting length in the cutting process, we know that the tool wear is from small to large: a → D → C → B. It can be seen that the thickness of sawtooth on the back of chip has a certain corresponding relationship with the tool wear of gray cast iron. The thinner the sawtooth thickness on the back of the chip, the smaller the tool wear. Because the graphite in cast iron has solid lubrication and graphite particles exist on the chip surface, it will reduce the friction between cutting tools and chips, reduce chip removal resistance and cutting power consumption. In addition, the graphite sheet destroys the continuity of base metal and is also conducive to short chip and chip removal. Therefore, when there is a large amount of graphite in the structure of gray cast iron, it is conducive to the deformation of cutting layer metal, It can reduce the cutting resistance in the cutting process and make the chip thickness thinner, so as to improve the cutting performance of gray cast iron.
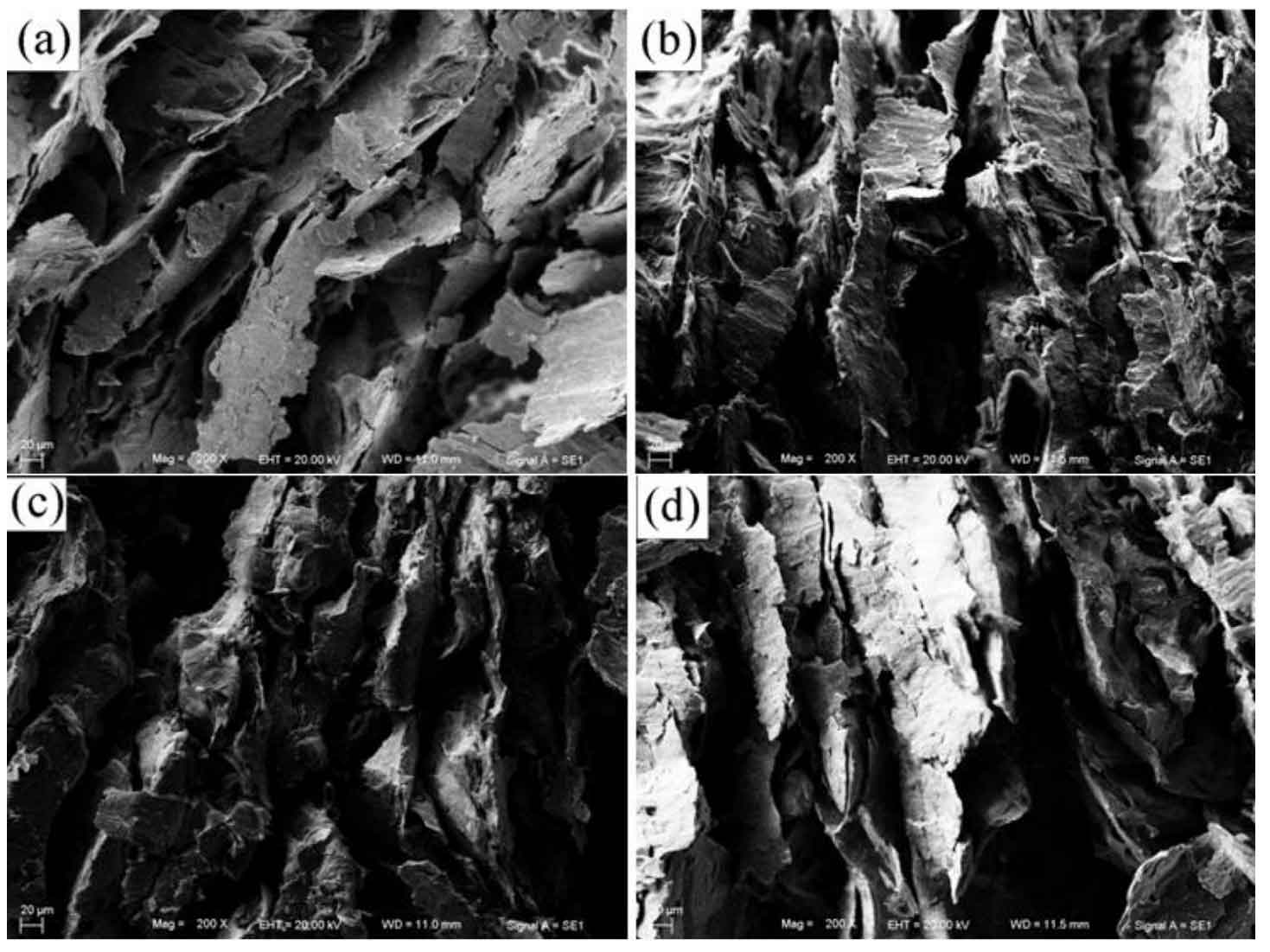
(c)sample C—Zr-Si-Al inoculation treatment;(d)sample D—Zr-Si-Mn inoculation treatment.
Because there is no unified index to measure the turning performance of gray cast iron, we use the comprehensive evaluation method to compare the turning performance of various experimental gray cast iron. The method is to give different scores to each measurement index according to the order of index values, reflecting the cutting performance of gray cast iron from good to bad, and give values of 1, 2, 3 and 4 respectively. Because each measurement index has different influence on cutting performance, we give different weights to each measurement index. Then, according to formula 3-1, the comprehensive measurement index k of the turning performance of four different experimental gray cast iron is calculated. The higher the K value, the better the turning performance of this kind of gray cast iron. On the contrary, the greater the K value, the worse the turning performance of this kind of gray cast iron.
Where:
K – comprehensive value of turning performance;
δ— Weight of sub indicators;
X — score of sub indicators.
Through the above analysis of various factors affecting the turning performance, according to the calculation, we can conclude that after inoculation with different inoculants, the turning performance of the experimental gray cast iron from high to low is as follows: sample a (75 ferrosilicon inoculation) → sample C (silicon zirconium aluminum inoculation) → sample D (silicon zirconium manganese inoculation) → sample B (silicon zirconium inoculation).