The drawing shows the shrinkage pore distribution of a series of hydraulic valves made of steel-304 stainless steel with casting temperature of 1700C. It can be seen from the drawing that the maximum porosity is 75.8%. By contrast, when the casting material is nodular cast iron QT500-7, the volume of shrinkage pore is much smaller than that of material Steel-304 although the maximum porosity of the casting is larger.
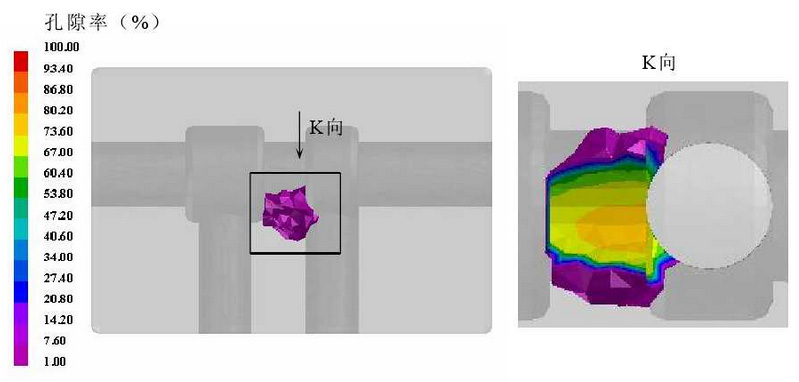
This is because steel-304 stainless steel undergoes three major contractions during solidification: liquid phase contraction, phase transition contraction and solid phase contraction. In the middle and late stages of solidification, with the continuous increase of liquid metal contraction during cooling, the pressure of liquid metal decreases, which can not compensate the non-solidified liquid metal and finally produces a large number of shrinkage holes.Volume changes during solidification are different from other alloys. Volume expansion of ductile iron occurs during solidification with precipitation of graphite. Volume expansion caused by precipitation of graphite is sufficient to compensate for part of volume shrinkage. Therefore, the volume of shrinkage holes in casting decreases.
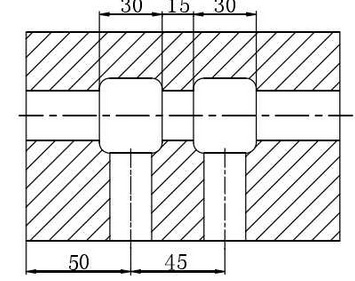
Due to the intersection of the valve bore, sinking groove and oil outlet, the casting shrinkage hole mainly appears near the two edges of the small sinking groove of the valve body near the oil outlet side. In view of this, the valve body structure is improved. As shown in the figure, the position of the oil outlet of the valve body and the size of the valve body sinking groove are changed while keeping the other dimensions unchanged.