1.Graphite morphology
Figure 4 shows the graphite morphology of two groups of gray cast iron samples. It can be seen from the figure that the morphology of different alloyed graphite is different. The graphite form of sample 1 is relatively fine curved flake A-type graphite (Fig. 4 a)), while the graphite form of sample 4 is relatively coarse and flat A-type graphite with massive C-type graphite (Fig. 4 b)). The addition of Cu will affect the graphite morphology, and it is easy to produce a certain amount of C-type graphite (block graphite is added in the middle of A-type graphite). The graphite content of sample 4 (20.42%) measured by metallographic analysis software is less than that of sample 1 (21.55%).
Sample 1 contains more graphite, which plays a good role in lubricating the tool, reduces the friction between the workpiece and the tool, reduces the wear of the tool, and increases the service life of the tool. Moreover, the fine curved flake A-shaped graphite structure can improve the deformation of chips, so it is easy to break chips. Therefore, the cutting performance of gray cast iron of the workpiece is good, so the cutting performance of sample 1 is good (Fig. 1, 2 and 3). Sample 4 contains not only less graphite, but also massive C-type graphite. Compared with type a graphite, massive C-type graphite is not conducive to tool lubrication and chip breaking, which aggravates tool wear. With the increase of the friction force on the tool, the machining performance is poor (Fig. 1, 2 and 3). Therefore, the machining performance of copper alloyed gray cast iron is worse than that of multicomponent alloy.
2.Pearlite structure
Figure 5 shows the pearlite structure of two groups of gray cast iron samples. It can be seen from a) and b) in Fig. 5 that the matrix structure of gray cast iron treated by multicomponent addition and copper alloying is pearlite structure. Moreover, there is no obvious difference between the pearlite of the two groups of samples. Under high-power scanning electron microscope, as shown in C) and D) in Fig. 5, there is no obvious difference in flake spacing and lamellar structure of pearlite of gray cast iron treated by multicomponent addition and copper alloying, and the carbides of the two kinds of gray cast iron are large, small and very uneven. Pearlite matrix should have a certain influence on the machinability of gray cast iron, which can not be well quantified from metallography and scanning photos. However, it can be seen that the microhardness distribution of copper alloyed gray cast iron matrix is very uneven, indicating that the pearlite matrix structure is also very uneven, resulting in poor machinability of copper alloyed gray cast iron.
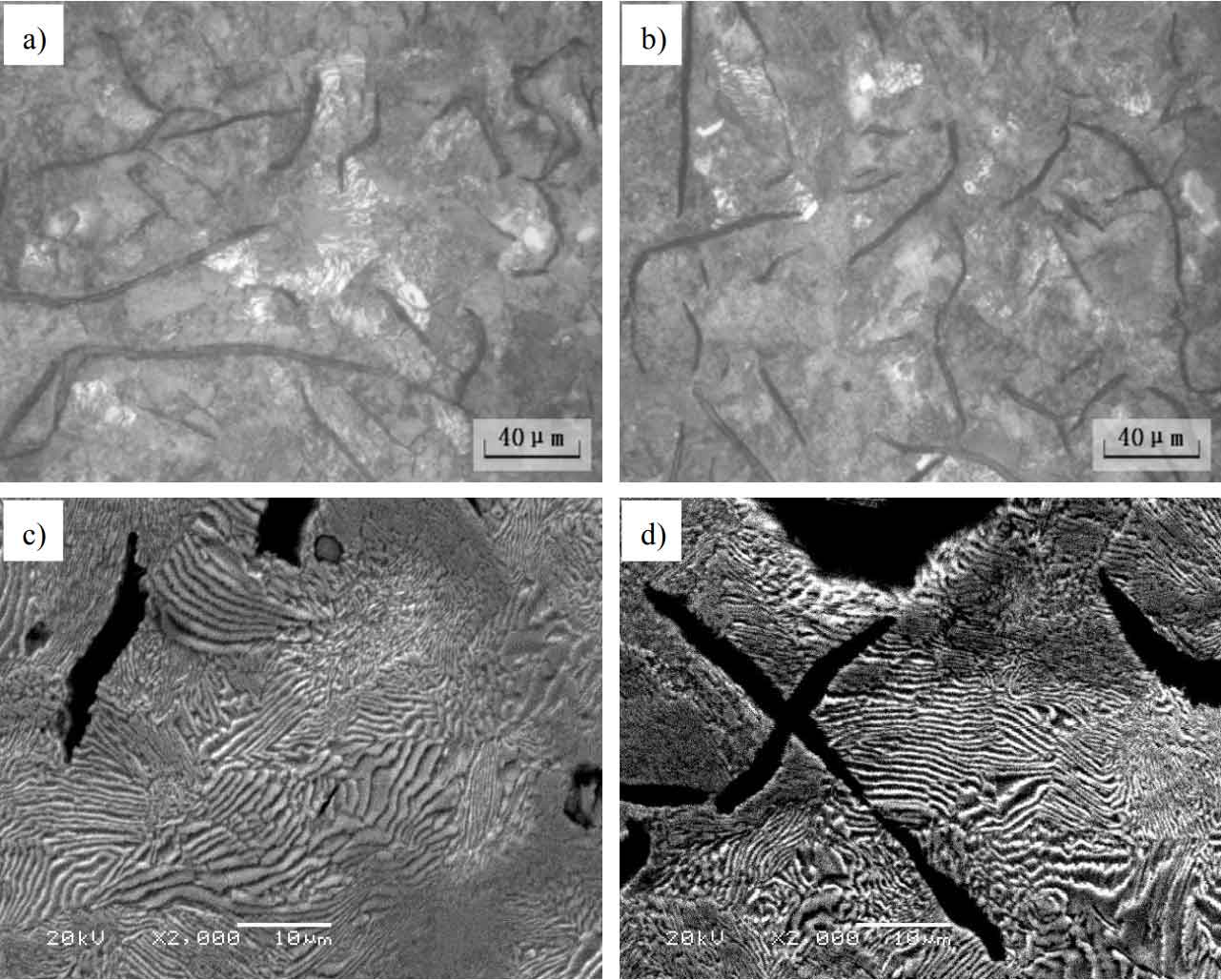
According to the above analysis, the effective way to improve the machinability of medium and high strength gray cast iron is to improve the microstructure uniformity of gray cast iron and obtain fine flake type a graphite with uniform distribution. This requires not only improving the metallurgical quality of molten iron to facilitate the control of graphite nucleation, but also selecting appropriate inoculants and inoculation methods. The addition of alloy elements should be as few as possible or more favorable alloys, so as to obtain gray cast iron with excellent strength and processability.