Through macroscopic observation and analysis of graphite floating, under the same wall thickness and pouring conditions of inlet cylinder, the top graphite floats when the carbon equivalent CE is more than 4.72% in 400mm thick large section. The results show that the graphite morphology is good in the range of 4.36-4.72% for CE, and different degrees of graphite floating appear in the range of 4.72-4.89%. With the increase of CE value, the thickness of graphite floating layer will increase, and the graphite morphology will become worse. There is no graphite floating in the section with thickness of 150 mm and 70 mm, which indicates that the critical carbon equivalent CE value will be increased with the decrease of wall thickness.
Analyze the strength test results, record the data, and analyze the tensile properties of three groups of test blocks with different Si content, as shown in Figure 1.
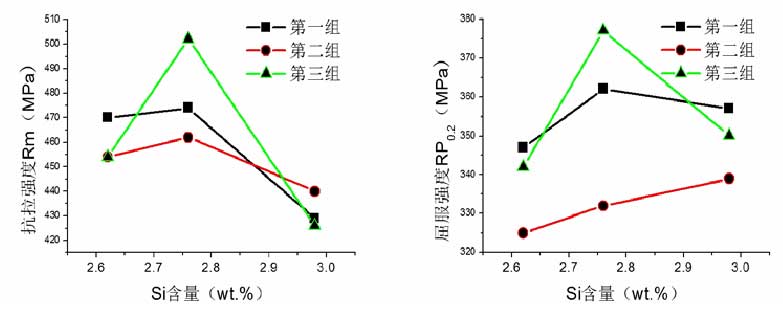
It can be seen from the trend chart in Fig. 1 that the addition of Si element can effectively improve the spheroidizing quality of nodular cast iron, which has an important impact on the number and roundness of graphite balls. However, if the content of Si element is too high, it will lead to graphite distortion, broken graphite and other defects. The experimental results show that the graphite balls with Si content ≤ 2.8wt.% are uniform and well spheroidized. The deformed graphite with Si content of 3.0wt.%, such as broken graphite and worm like graphite, can be found in the block with 3.0 wt.%, which leads to the decline of mechanical properties and seriously affects its use.
(1) The casting composition and melting process control parameters are determined.
(2) The carbon equivalent of fcd450 is 4.4-4.7%, which can not only ensure that there is no chill and graphite floating, but also obtain the dense structure of the casting body.
(3) The solidification curves of nodular cast iron castings with different C contents are quite different. The eutectic plateau of low carbon is obviously smaller than that of high carbon, and the liquid shrinkage is large. The chemical composition of the intake cylinder casting is C ≈ 3.7wt.%, Si ≈ 2.8wt.%, which can not only ensure the minimum tendency of shrinkage porosity and abnormal distortion graphite, but also ensure that its physical and chemical properties meet the requirements of acceptance standard.