Pouring temperature is the temperature at which the liquid metal enters the gate. If the pouring temperature is too high, it will not only waste energy, but also lead to defects such as coarse grains in the internal structure of the casting and poor feeding effect of the riser. If the pouring temperature is too low, it will affect the fluidity of the liquid metal and lead to casting defects such as insufficient pouring, especially for the casting with complex structure. The liquidus temperature of 20CrMoH used in this casting is 1511 ℃, the casting size is small and the structure is relatively complex. According to different experience, the recommended pouring temperature is 1650 ℃. The main effect of pouring temperature on casting defects is shrinkage defects. In order to further study the influence of pouring temperature on the shrinkage defects of spiral bevel gear casting described in this paper, the pouring scheme of central top injection mold is simulated with pouring temperature as a variable.
The distribution of shrinkage porosity in the tooth surface and riser section of gear blank casting at different pouring temperatures. As can be seen from the observation diagram, when the pouring temperature is At 1530 ℃, there are serious shrinkage defects on the tooth top surface of the gear blank casting, and the casting defects at the root of the tooth shape can be seen in the cross section, which shows that the casting temperature is too low and the cooling and solidification speed of the casting is too fast, resulting in a large number of defects; then with the increase of the casting temperature, the casting defects gradually reduce; when the pouring temperature reaches At 1640 ℃, the shrinkage defects of castings have been obviously improved, both on the tooth surface of castings and inside of castings, the shrinkage defects are relatively slight; when the pouring temperature is raised, the status of the defects is basically unchanged.
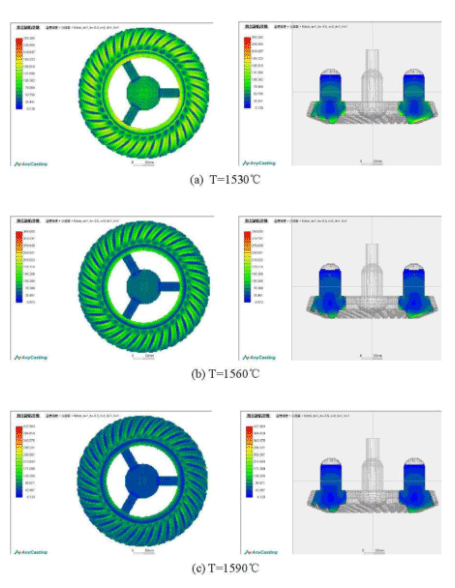
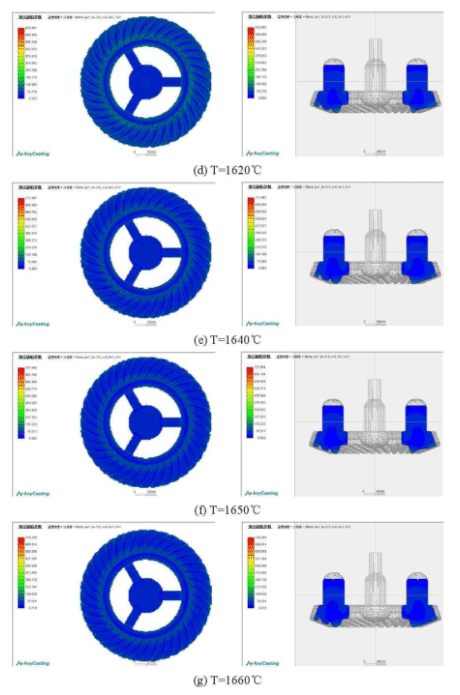
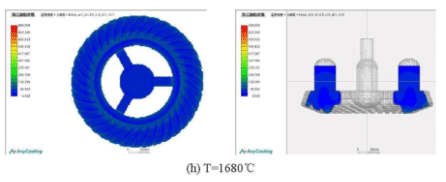
To sum up, in a certain temperature range (1510 ~ 1640 ℃), the higher the pouring temperature, the smaller the shrinkage defects of gear blank casting; when the pouring temperature reaches 1640 ℃, the least casting defects. The higher the pouring temperature is, the more energy is needed, so 1640 ℃ is the best pouring temperature.