Generally speaking, the gap between the alloy melt and the die is reduced and the heat transfer is accelerated under the action of pressure. The higher the pressure is, the faster the solidification rate of the alloy liquid is, which inhibits the growth of primary particles and secondary solidified particles in the slurry, thus achieving the effect of grain refinement. In addition, the phase diagram changes and the melting point increases when the alloy solidifies under pressure. According to Clausius Clapeyron equation.
Where p is the pressure, TM is the melting point of the alloy under standard atmospheric pressure, and the melting point of nz30k alloy is about 643 ℃. Δ V is the volume change of the alloy liquid from liquid phase to solid phase, QM is the latent heat of solidification
Where P0 is the standard atmospheric pressure and TM Δ V / QM can be regarded as a constant
The undercooling of the alloy solidified under pressure can be calculated by the following formula:
Where Δ t0 is the undercooling of the alloy at standard atmospheric pressure. In addition, the expression of heterogeneous nucleation rate is as follows
Where n is the number of atoms per unit volume, K is the Boltzmann constant, h is the Planck constant, and Δ g * is the activation energy of heterogeneous nucleation
Where f (θ) = (2-3cos θ + cos3 θ) / 4, σ is the surface tension. The relationship between surface tension σ and pressure P is as follows
Where σ 0 is the surface energy at standard atmospheric pressure and ε is the adiabatic compressibility coefficient
Where CP is the specific heat at atmospheric pressure, CV is the constant volume specific heat, ρ is the density, μ is the sound velocity of the atom. The relationship between Q and P is as follows
Q0 is the activation energy when the pressure is 0. In conclusion, the heterogeneous nucleation rate of alloy melt during pressure solidification is as follows:
It can be seen from the above formula that the nucleation rate n of heterogeneous nucleation is related to pressure and undercooling. Under the pressure, n increases with the increase of pressure, which has a significant grain refinement effect. According to the melting point and density of nz30k alloy, the heterogeneous nucleation rate of nz30k alloy under different pressure can be calculated. Because of the small contact angle between Mg and Zr, the value of F (θ) calculated by as cast microstructure is about 1.7 × 10-5. The results are shown in Fig. 1. When the undercooling is less than 13.8 ℃, the nucleation rate of the alloy melt increases with the increase of pressure. Therefore, the particle size of secondary solidification particles decreases significantly with the increase of pressure. Secondary solidification particles are formed by solidification of residual liquid phase in semi-solid slurry. The decrease of size and the increase of pressure mean that the residual liquid phase is easier to flow to the edge of casting in the forming process. The action time of PDS mechanism of primary particles is longer and the deformation degree of particles is larger. At the same time, the density of the alloy increases correspondingly. Similarly, based on the existing heterogeneous nucleation theory and the influence of pressure on the diffusion activation energy, Han et al. Proposed a quantitative model to calculate the nucleation rate, and calculated the nucleation rate of A356 aluminum alloy during solidification under different pressures. Compared with this model, the calculation of Δ g * is different. If the effect of pressure on surface tension is considered in this paper, according to the formula, the surface tension is about 2.2 times of that of 0 MPa when forming at 120 MPa.
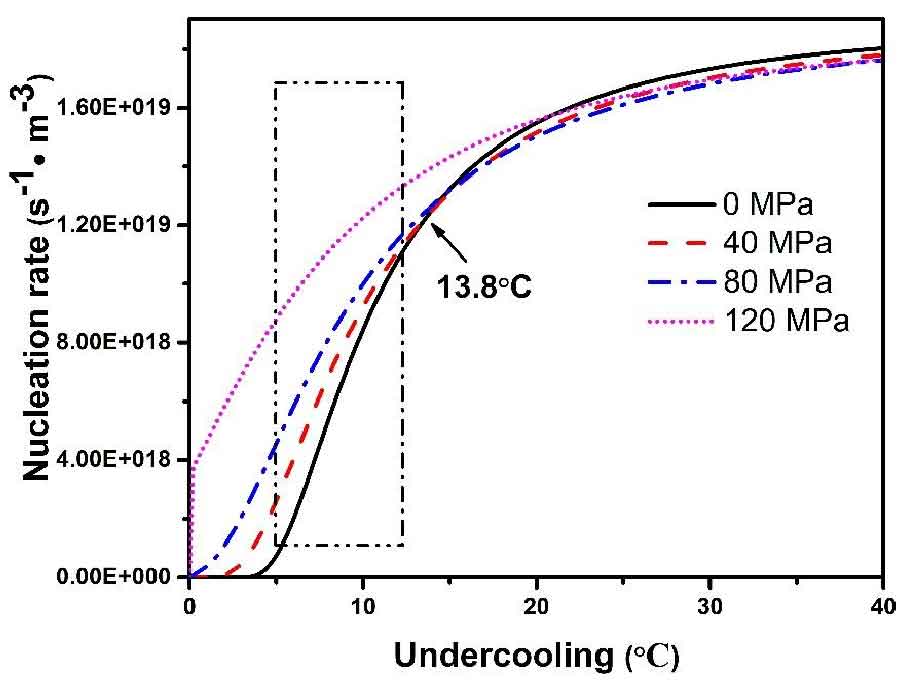
As shown in Fig. 2, in addition to refining the grains, the pressure exerted during the solidification of the alloy melt also affects the morphology and composition of the second phase. When the pressure increases from 0 MPa to 120 MPa, the second phase between the particles almost completely dissolves into the matrix, and the Nd and Zn elements in the second phase decrease correspondingly, which indicates that the solid solubility of Nd and Zn in α – Mg increases with the increase of pressure. Therefore, with the increase of pressure, the second phase transformation between α – Mg particles in the alloy structure becomes smaller and the lattice constant decreases. In addition, the diffusion coefficient of Zn in MG is larger than that of Nd in mg. Therefore, when the pressure increases to 40 MPa, more Zn is dissolved in α – Mg, and when the pressure is 80 MPa, almost all Zn is dissolved.
The mechanical properties of the as cast alloy increase with the increase of pressure from 0 MPa to 80 MPa. Based on the above analysis, the main reason for the gradual improvement of mechanical properties of the alloy is the refinement of primary particles and secondary solidification structure. Another important factor is the densification of the alloy structure. With the increase of pressure, the fluidity and feeding ability of slurry are enhanced, and the defects such as porosity and shrinkage cavity are greatly reduced. Therefore, the denser the alloy structure is, the higher the mechanical properties are. In addition, plastic deformation can also improve the mechanical properties of the alloy. When the pressure is increased to 120 MPa, the plastic deformation of the alloy is intensified, and the crack is easy to propagate along the deformed particles, resulting in the decrease of the tensile strength of the alloy. However, due to the smaller grain size, the yield strength and elongation of the alloy are also improved.