In this test, the method of variable control was adopted. Under the condition of other parameters unchanged, the boosting pressure was set to 200bar, 500bar, 800bar and loobar respectively for die casting.
According to the sample preparation and detection methods, the semi-solid die casting samples were analyzed by sawing, polishing, fluorescence, detection and metallographic observation. The effect of pressurization pressure on shrinkage cavity and porosity is shown in Fig. 1, and Fig. 2 shows the metallographic photos of typical positions under 200bar and looobar pressure.
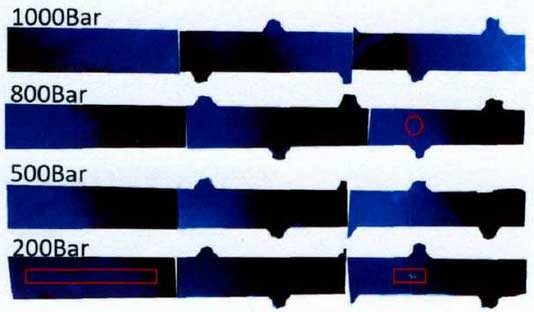
It can be seen from Fig. 1 that when the pressurization pressure is low (200bar), there are obvious shrinkage and porosity defects at the bottom and top of the sample, which show bright spots and aggregation spots under fluorescence, and black holes in metallographic photos (Fig. 2Ab). When the pressure is increased, the phenomenon is obviously improved, the shrinkage porosity defects in the lower area disappear, and the shrinkage porosity defects in the upper part disappear The area also changed from large area shrinkage porosity to point like shrinkage cavity. Under the fluorescence observation, the aggregation spots change into bright spots. When the pressurization pressure increases to looobar, there are no bright spots or aggregation spots in the whole area of the sample under fluorescence observation, and the black holes completely disappear under microscopic observation (Fig. 2c, d), which means that the shrinkage cavity and porosity defect have completely disappeared. Through the actual production verification, when the pressure is loobar, the cylindrical sample without shrinkage cavity and porosity can be produced stably.
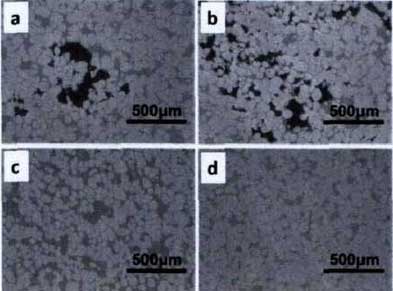
In the process of fluorescence analysis, it can be found that all bright spots appear in the “center” region along the filling direction of the sample, that is to say, the shrinkage cavity and porosity defect appear in the “feeding channel”. This is consistent with the previous literature research, the formation of shrinkage porosity is due to insufficient feeding. In this experiment, when the pressurization pressure is 200 bar, there is not enough force to push the feeding channel at the material handle at the end of solidification due to the small pressure at the end of solidification. With the increase of pressurization pressure (500800bar), the feeding channel was improved in the process of solidification shrinkage at the end of solidification. The shrinkage cavity and porosity in the feeding channel are obviously improved. When the pressure increases to loobar, there is enough force to push the material handle to strengthen the feeding channel. The feeding can be carried out smoothly in the process of solidification and shrinkage. Finally, shrinkage cavity and porosity will not occur after solidification.