The picture shows the microstructure of white cast iron with different wall thickness. Among them, figures (a) – (c) are the organization diagrams of samples with thickness of 20, 40 and 60mm respectively.
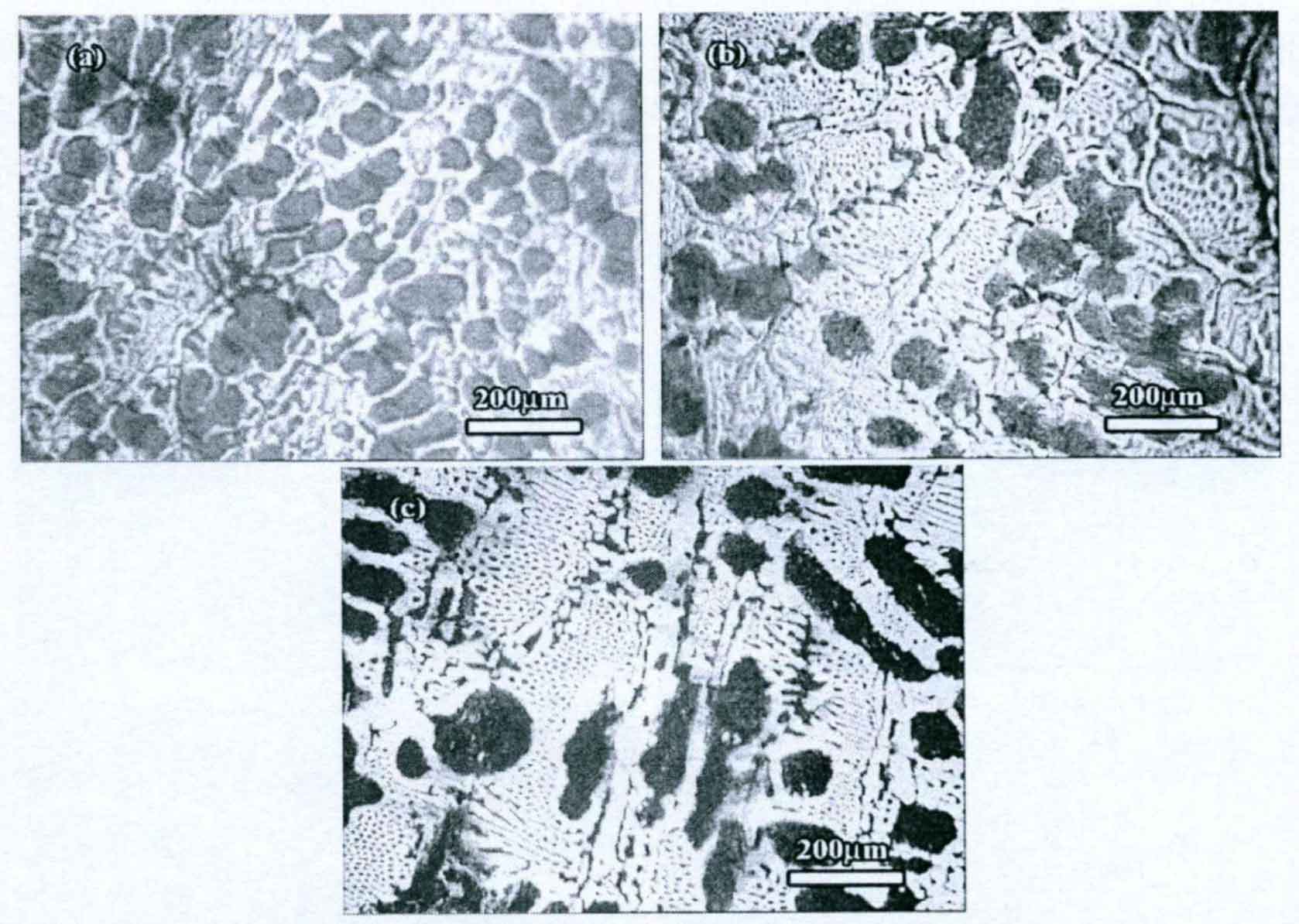
It can be seen from the figure that the structure of the casting is a typical hypoeutectic white mouth structure, and the black etchant shown in the figure is the pearlite structure transformed from primary austenite during cooling, that is, the mechanical mixture of ferrite and cementite; The white impregnated material is ledeburite, which is a mechanical mud compound composed of pearlite and cementite. When the liquid metal is cooled, when its temperature drops to the liquidus and has a certain degree of supercooling, the solidification begins. The carbon equivalent of white cast iron belongs to the composition of hypoeutectic white cast iron. When solidification occurs, primary austenite precipitates from the liquid metal, and the composition of the liquid phase is close to the eutectic point. After further cooling, when the temperature is reduced to the eutectic temperature, the remaining metal melt undergoes Eutectic Transformation to form ledeburite, which is a mechanical mixture of austenite and cementite. After cooling to eutectoid temperature, white cast iron undergoes solid phase transformation and primary austenite undergoes eutectoid transformation to form pearlite composed of ferrite and cementite.
Sample wall thickness /mm | 20 | 40 | 60 |
Ledeburite content /% | 41.8 | 53.7 | 62.6 |
In addition, it can be seen from the figure and table that the size of primary austenite increases with the increase of sample wall thickness. Primary austenite is granular austenite with random distribution and non directional arrangement. Moreover, the content of austenite decreases with the increase of sample wall thickness. This is because the primary austenite undergoes two processes: nucleation and growth. When the sample wall thickness is small, the cooling rate is faster and the undercooling degree is larger during solidification. It can be seen from the analysis that the increase of undercooling reduces the critical nucleation size of the alloy, which is conducive to the nucleation of the metal. At the same time, the increase of undercooling increases the driving force in the solidification process of the metal, which is conducive to the nucleation and growth of the metal. Finally, the content of primary austenite in the cast iron alloy increases. When the wall thickness is large, the critical nucleation radius of the metal is increased, the driving force of metal solidification is reduced, and the content of primary austenite in the alloy is reduced due to the decrease of undercooling. Due to the slow cooling rate and long solidification time of the metal, the primary austenite after nucleation grows faster and takes a long time to form the primary austenite with larger size. In addition, the more the number of crystal nuclei in the metal, the more conducive to the formation of small granular dendrites in Jinli, so there are more granular dendrites in the castings with thinner wall thickness.