It has been proved that different types of carbides have different hardness. The purpose of different casting processes is to obtain more M7C3 type compounds with high hardness. In the study of directional solidification, it is found that the hardness of hexagonal end face [0001] of M7C3 carbide is higher than that of straight side face [1010], and the wear resistance is better. Under the pressure, the nucleation of carbides is greatly improved, the equilibrium distribution coefficient is changed, and the distribution of solute elements in the melt is also changed. These factors may lead to the morphology and phase transformation of carbides. X-ray diffraction (XRD) experiments were used to characterize the phase composition of the samples under different pressures. Through the calibration and comparison of the diffraction peaks, the effect of pressure on the type of carbides was revealed.
The X-ray diffraction (XRD) patterns of chromium white cast iron samples with different compositions cast under normal pressure and pressure are shown in the figure( α- Fe Cr, 520-512 (austenite) and 05-0720 (M7C3) were determined accurately.
The CR / C of low chromium hypoeutectic alloy is less than 3.5, and there should be only m3c carbide in the solidified structure under normal pressure casting. However, according to the calibrated diffraction peak, as shown in figure (a), in addition to m3c type carbides, there are smaller (42.611) diffraction peaks of M7C3 in this experimental condition, which indicates that the surface of M7C3 is low
A small amount of M7C3 carbide appears in chromium white cast iron. In addition, in addition to carbide phase, martensite and other austenite transformation products appear. It is found that the solidification structure is composed of m3c, M7C3, austenite phase and a small amount of austenite transformation products.
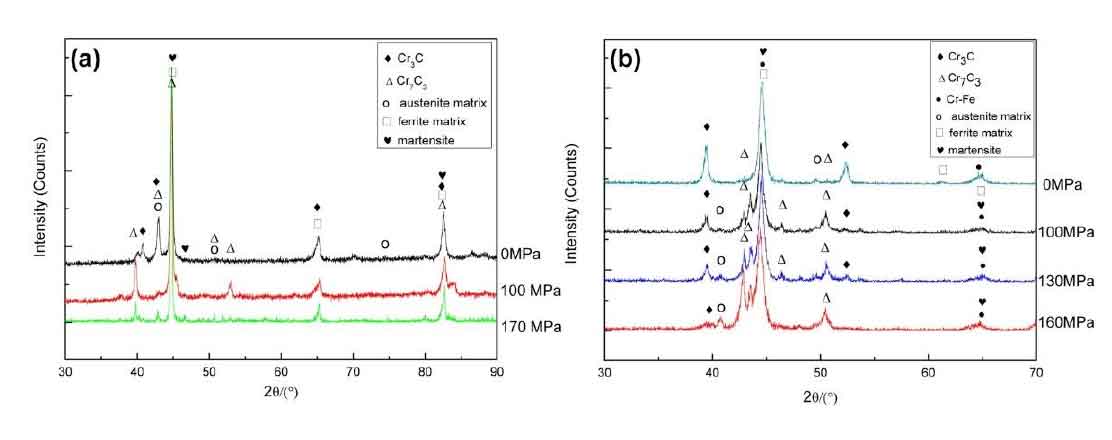
According to the composition ratio of the experimental materials, the CR / C of the near eutectic alloy 2 # is between 7 and 8. According to the figure (b), two types of carbides, M23C6 and M7C3, may appear under the conventional casting conditions. According to the corresponding jcpds, the diffraction peak of M23C6 decreases with the increase of pressure, and the peak of M23C6 decreases with the increase of pressure
The main diffraction peak of 7C3 changes from narrow to wide, which indicates that the content of M23C6 decreases, the content of M7C3 increases or the grain size decreases.